Welding porosity is a common defect encountered in welding production, formed by the absorption and release of gases (primarily oxygen, nitrogen, and hydrogen) within the weld seam. It not only reduces the effective cross-sectional area of the welded component but also causes stress concentration, significantly lowering the strength and toughness of the weld metal. This is particularly detrimental to dynamic load strength and fatigue strength. In some cases, porosity and inclusions can also lead to cracks.
Welding porosity is a relatively common defect in welding. From the perspective of its formation causes:
Welding materials. If the welding rod or flux is damp, moisture will be released during the welding process, leading to welding porosity; impurities such as oil stains or rust on the surface of the welding wire may also cause porosity. In arc welding, porosity is caused by excessive hydrogen and carbon monoxide in the gases produced.
Welding process parameters. Both excessive and insufficient welding current can have an impact. When the current is too high, the filler rod overheats, causing the flux coating to peel off prematurely and resulting in porosity; when the current is too low, the arc blowing force is insufficient, leading to poor metal flow in the molten pool and difficulty in gas escape, which can also cause porosity. If the welding speed is too fast, gases may not have time to escape and remain trapped in the weld, forming porosity.
Welding operating environment. Welding in a windy environment can disperse the shielding gas, causing the molten pool to lose protection and allowing air to enter, forming porosity. In confined spaces with poor ventilation, gases generated during welding can accumulate, also leading to porosity.
Types of welding porosity – Precipitation-type welding porosity
Precipitation-type porosity occurs due to differences in the solubility of gases in metal, leading to an oversaturated state in liquid metal during cooling, which causes gas precipitation and the formation of porosity. This type of porosity is typically caused by the intrusion of external hydrogen or nitrogen into the molten pool.
- Hydrogen porosity: The solubility of hydrogen in liquid and solid metal differs significantly. When liquid metal solidifies, the solubility of hydrogen gas decreases sharply from 32 mL/100 g to 10 mL/100 g, leading to gas precipitation and the formation of hydrogen pores. In the welding of low-carbon steel and low-alloy steel, hydrogen pores typically appear on the surface of the weld, with a screw-like cross-section and smooth inner walls around the edges, resembling a bell mouth. Sometimes, hydrogen pores may also appear inside the weld, especially when the flux coating of the welding rod contains a high amount of crystalline water, or when welding aluminium alloys and magnesium alloys, where the released gases fail to rise promptly and remain trapped in the weld, forming pores.
- Nitrogen pores: The formation mechanism of nitrogen pores is similar to that of hydrogen pores, primarily caused by gas release. However, nitrogen pores typically form on the weld surface and often appear in clusters, resembling a honeycomb structure. The primary cause of such pores is inadequate protective measures during welding, leading to excessive air intrusion into the welding zone.
The appearance of precipitation-type welding porosity is typically caused by the intrusion of external gases and differences in gas solubility within the metal. Understanding the causes of these pores can help welders better control and prevent welding defects, ensuring weld quality and structural reliability.
Reactive welding porosity is caused by gases produced by metallurgical reactions in the molten pool, such as carbon monoxide (CO) and water vapour (H₂O). These gases are insoluble in liquid metal and cannot escape in time, thereby forming porosity in the weld.
- Carbon monoxide porosity: Carbon monoxide porosity is caused by metallurgical reactions in the molten pool that produce carbon monoxide (CO), which is insoluble in liquid metal. When welding carbon steel, if the carbon content in the liquid metal is high and deoxidation is insufficient, CO is generated through metallurgical reactions. Although CO escapes from the liquid metal in the form of bubbles at high temperatures, causing spatter, it does not form porosity. As the molten pool begins to crystallise, the concentration of oxides and carbon within the molten pool increases, particularly at the trailing edge of the molten pool, creating conditions favourable for metallurgical reactions and resulting in the generation of more CO gas. As the temperature of the molten pool decreases, the viscosity of the metal increases, making it difficult for CO gas to escape. Especially at the dendritic depressions of the grains, CO gas finds it even harder to escape, leading to the formation of pores. These pores are worm-like in shape and distributed along the crystallisation direction.
- Water vapour porosity: Water vapour porosity typically forms during the welding of materials such as copper or nickel. The oxides of copper (Cu₂O) react with hydrogen dissolved in the copper, producing water vapour that is insoluble in liquid metal, leading to the formation of porosity. The same reaction may occur during nickel welding, where nickel oxides react with hydrogen in the metal to produce water vapour porosity. These pores typically form when water vapour fails to escape in a timely manner.
Reactive pores are primarily caused by gases generated by metallurgical reactions. These gases fail to escape during crystallisation and form pores within the weld. Understanding the formation mechanism of reactive pores can help welders reduce pore formation by optimising welding processes, thereby ensuring weld quality and structural strength.
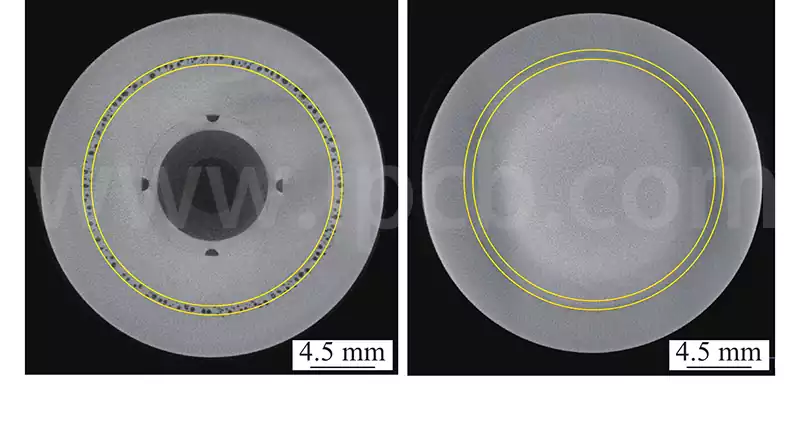
The main hazards of welding porosity:
(1) Reduced mechanical properties of the weld joint. The presence of welding porosity reduces the load-bearing capacity of the weld. Since porosity occupies a certain volume of the weld metal, it reduces the effective working cross-sectional area of the weld, thereby lowering its mechanical properties, particularly its ductility and impact toughness.
(2) Induce the formation of weld cracks. If pores penetrate the weld surface, especially the weld surface in contact with the medium, the medium remains inside the pores. When the medium is corrosive, it causes localised corrosion, causing the pores to deepen and enlarge, eventually leading to corrosion perforation and leakage, thereby compromising the weld’s integrity. In severe cases, this can result in the failure of the entire metal structure. If the pores are located at the root of the weld or are vertical, they may cause stress concentration and become a source of weld cracking.
(3) Impact on weld fatigue performance Under alternating stress, pores significantly affect the fatigue strength of the weld. However, if the pores do not have sharp edges, they are generally not considered harmful defects and are permitted to exist in the weld to a limited extent. However, according to the specifications, if the porosity exceeds the specified requirements, repair must be carried out.
Solutions for welding porosity
1) Use preheating and post-heat treatment:
Preheating reduces the temperature gradient at the welded area, decreases the solubility of gases, and promotes their escape. Post-heat treatment eliminates residual stress in the weld, improves the microstructure and properties of the weld, thereby reducing the impact of welding porosity. The temperature and duration of preheating and post-heat treatment must be selected and controlled based on the specific welding materials and methods.
2) Use active gases or pulsed laser welding:
Active gases can react chemically with gases in the molten pool to form compounds that are easier to expel, thereby reducing welding porosity formation. Pulsed laser welding technology can alter the behaviour of the molten pool, reducing the ingress of shielding gas into small holes, thereby minimising or eliminating porosity.
3) Using beam oscillation or arc oscillation methods:
Beam oscillation or arc oscillation can increase the fluidity of the molten pool, promote gas exhaustion, and simultaneously improve weld bead formation and filling effects, thereby effectively reducing the formation of welding porosity.
4) Performing repairs or re-welding:
If porosity has already formed in the weld, repairs or re-welding can be used to eliminate or reduce it. Repair involves re-welding at the porosity site, filling with welding wire or flux to make the porosity disappear or shrink; re-welding involves re-welding the entire weld to repair the original weld defects. Re-welding is typically used when there are numerous porosities or they are located in critical areas.
5) Strengthen on-site control and management:
During welding, strict control of the welding environment should be maintained to ensure compliance with welding procedures. Especially in environments with high wind speeds or humidity, measures such as wind protection or environmental monitoring should be implemented to ensure the quality of shielding gas. Additionally, comprehensive welding operation procedures and inspection systems should be established to ensure welders adhere to specified process parameters and operational methods, thereby minimising the occurrence of porosity.
6) Select appropriate welding equipment and processes:
The selection of welding equipment is also a key factor influencing welding porosity. Using suitable welding machines, shielding gas flow control devices, and welding fixtures can improve welding quality. Additionally, consider adopting more advanced welding methods, such as TIG welding (tungsten inert gas welding) and MIG welding (metal inert gas welding), which typically offer better melt pool control performance, thereby reducing the formation of welding porosity.