Paste flux is a key ingredient in solder paste, mainly used to clean the metal surface of oxides during the soldering process and to promote the wetting and flow of the solder, thus ensuring a strong and reliable joint. It usually consists of rosin, active agents, organic acids, thixotropic agents, solvents and other ingredients, which are mixed with solder powder to form a paste-like substance suitable for soldering electronic components in surface mount technology (SMT).
Common Paste Flux:
Rosin Flux:
Rosin flux is the most common type of flux. Its flux performance is weak, less corrosive, the residue is basically non-corrosive, stay on the substrate to form a protective film, but sometimes sticky and hygroscopic, generally not clean.
Water-soluble flux:
Water-soluble flux, as the name suggests, in the water solubility, strong activity, good fluxing performance, post-soldering residues can be cleaned with water. Water-soluble flux has strong de-oxidising ability, strong fluxing performance, stable storage and non-toxic. The residue after welding is easily soluble in water, no pollution to the environment. After cleaning the pcb to meet the cleanliness requirements, non-corrosive, does not reduce the electrical insulation properties.
No-clean flux:
No-clean flux refers to the flux that contains only a trace amount of harmless flux residue after soldering and does not need to be cleaned after soldering. It is not only non-toxic and odourless, less smoke, and does not pollute the environment, good solderability. As there is very little residue after soldering, it ensures dry, non-sticky pcb panels and can also be tested online. Moreover, the storage period of no-clean flux can be up to one year.
Melting Temperature Range of Solder Paste Flux
The melting temperature of solder paste fluxes usually ranges between 120-250°C, depending on the following factors:
- Alloy composition:
- Lead-free solder pastes (e.g. SAC305, Sn 96.5% / Ag 3% / Cu 0.5%) have a melting point of approximately 217-220°C (refer to IPC J-STD-006 standard).
- Lead-containing solder paste (e.g. Sn63/Pb37) has a lower melting point of 183°C (U.S. NIST data).
- Flux type:
- Rosin type fluxes have a lower melting point (120-180°C) and are suitable for precision soldering;
- Water-soluble flux melting point is higher (190-250 ℃), need to cooperate with high-temperature process.
Melting point temperature differences, mainly in the following two aspects:
Process requirements:
During reflow soldering, the solder paste needs to be completely melted at a peak temperature, which is usually about 20 to 40 degrees Celsius above the melting point of the solder paste. For example, the reflow oven temperature for lead-free solder pastes is always set in the 230 to 250 degree Celsius range to ensure that the solder is fully melted.
Manual soldering tends to use low melting point pastes, such as the Bi58/Sn42 alloy with its high bismuth content, which has a melting point of 138 degrees Celsius and has the advantage of melting quickly, making it suitable for fast soldering operations.
Reliability Considerations:
For automotive electronics and other fields that require high temperature resistance and long-term stability, high-temperature solder pastes containing silver are often used to enhance the reliability and durability of solder joints.
Low-temperature solder pastes, on the other hand, are suitable for protecting heat-sensitive components from damage caused by high temperatures, an application that has been confirmed by the Electronic Process Technology Institute 2022.
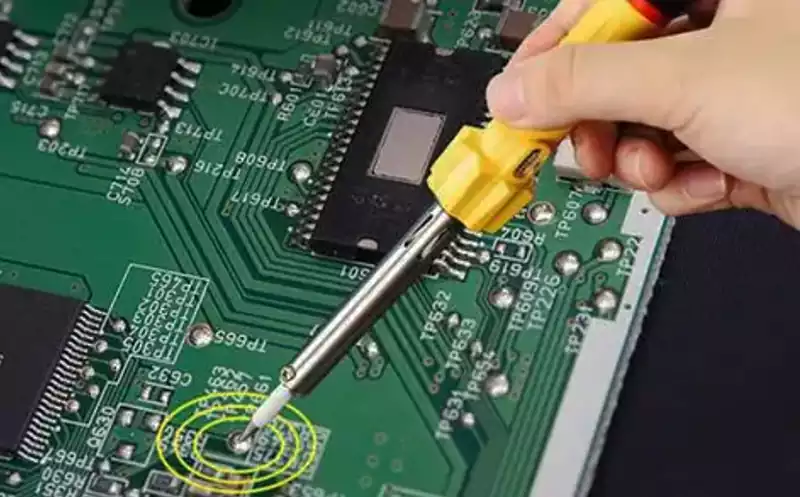
Tinning flux is a commonly used soldering material for electronic components, and its main components include the following three kinds:
- Activator: mainly composed of resin, active agent and flux, etc. Its role is to accelerate the welding process, promote the removal of metal surface oxides and activation of the metal surface, which is conducive to the contact and bonding between the metals, and to improve the welding quality and efficiency.
- Expanding agent: mainly composed of aluminium hydroxide and other substances, its role is to gradually expand in the heating process, the formation of tiny bubbles, the formation of a layer of expansion of aluminium oxide on the surface of the welded joints to protect the surface of the weldment to prevent oxidation, but also to promote the welding of the combination between the metals.
- Flux: mainly composed of active agents and chemical catalysts, etc., its role is to dissolve the oxides on the surface of the metal in the welding process, to promote the contact between the metal and the combination, improve welding quality and efficiency.
The main role of tinning flux is to enhance the welding effect and work efficiency, while protecting the surface of the weldment, specifically including:
Accelerate the welding speed: the active ingredient can accelerate the welding process, remove the oxidised film on the surface of the metal, activate the surface of the metal, which will help to make a close contact and bonding between the metals, thus enhancing the quality and efficiency of the weldment.
Protecting the surface layer of the weldment: The oxide film generated by the swelling agent can effectively protect the surface of the weldment from oxidation, while promoting a strong bond between the weld metals.
Dissolve surface oxides: Fluxes dissolve oxides on the surface of the metal during soldering, promoting good contact and bonding between the metals, enhancing soldering quality and efficiency.
Solder paste flux plays an important role in cleaning oxides, promoting wetting and protecting solder joints during the soldering process. Different types of fluxes are available to meet different process requirements, while tinning flux further enhance soldering efficiency and quality, ensuring a stable and reliable soldering process.