In the rapidly evolving field of electronics, flexible printed wiring boards (FPCB) represent a groundbreaking advancement in the design and functionality of electronic devices. These boards, which combine flexibility with electronic circuitry, have become crucial in modern technology due to their unique properties. This article explores the comprehensive details of flexible printed wiring boards, including their manufacturing process, applications, advantages, and challenges.
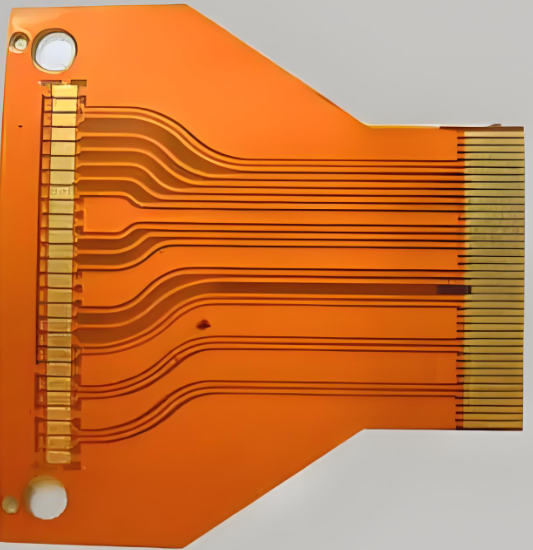
What is a Flexible Printed Wiring Board?
A flexible printed wiring board, or FPCB, is an electronic component that allows for bending and conforming to various shapes while maintaining its electrical functionality. Unlike traditional rigid printed circuit boards, FPCBs are made from flexible materials such as polyimide or polyester films. These materials provide the board with the ability to flex and bend without compromising its structural integrity. The manufacturing process involves several steps, each crucial to ensuring the board’s performance and reliability.
The initial step in manufacturing an FPCB is the preparation of the flexible substrate. This involves coating the flexible base material with a thin layer of conductive copper. The copper is then patterned using techniques such as etching or deposition to create the circuit pathways. After patterning, the board is covered with a protective layer to shield the circuits from environmental factors such as moisture and mechanical stress. The final step involves curing the board to ensure that the protective and conductive layers are firmly bonded.
Applications of Flexible Printed Wiring Boards
Flexible printed wiring boards are utilized in a diverse range of applications, each benefiting from their unique attributes. Their adaptability allows them to be used in environments where traditional rigid PCBs would be impractical or impossible.
- Consumer Electronics
Flexible printed wiring boards are widely used in consumer electronics, such as smartphones, tablets, and wearables. The compact and adaptable nature of FPCBs allows them to fit into the slim and compact designs of modern electronic devices. In smartphones and tablets, FPCBs are often used in connectors, display assemblies, and flexible antennas. Their ability to conform to the device’s shape enables a more efficient use of space, contributing to the sleek and compact designs of these devices.
- Automotive Industry
In the automotive industry, FPCBs are employed in various applications, including dashboard displays, lighting systems, and sensors. The flexibility of these boards allows them to be integrated into complex and compact spaces within vehicles. Additionally, FPCBs are designed to withstand harsh environmental conditions, such as high temperatures and vibrations, making them suitable for use in automotive systems that operate under demanding conditions.
- Medical Devices
Flexible printed wiring boards play a crucial role in medical devices, such as pacemakers, hearing aids, and diagnostic equipment. The ability of FPCBs to conform to irregular shapes is particularly valuable in the design of portable and wearable medical technologies. Their flexibility allows for the integration of electronics into compact and ergonomic designs, enhancing the functionality and comfort of medical devices.
- Aerospace and Defense
In the aerospace and defense industries, FPCBs are used in applications that require lightweight and adaptable components. Aerospace systems, including avionics and satellite equipment, benefit from the reduced weight and space-saving properties of FPCBs. In defense applications, FPCBs provide the durability and flexibility needed for equipment that must perform reliably in challenging environments.
Advantages of Flexible Printed Wiring Boards
The adoption of flexible printed wiring boards offers several significant advantages over traditional rigid PCBs, making them a preferred choice in many applications.
- Space Efficiency
One of the most notable advantages of FPCBs is their space efficiency. Their ability to bend and conform to various shapes allows for the optimal use of available space within electronic devices. This is particularly important in applications where space is limited, such as in compact consumer electronics or small medical devices. By utilizing FPCBs, designers can create more compact and efficient layouts, maximizing the use of available space.
- Reduced Weight
FPCBs are generally lighter than rigid PCBs due to their flexible materials and construction. The reduction in weight is advantageous in applications where weight is a critical factor, such as in aerospace and automotive industries. Lighter components contribute to overall weight reduction, which can enhance performance and fuel efficiency. The reduced weight of FPCBs also facilitates easier handling and integration into various designs.
- Enhanced Durability
The flexibility of FPCBs provides enhanced durability compared to rigid PCBs. FPCBs are less likely to crack or break under stress, making them suitable for applications that involve movement or vibration. This increased durability is valuable in harsh environments and demanding applications, such as automotive and aerospace systems. The ability of FPCBs to withstand mechanical stress contributes to their long-term reliability and performance.
- Design Flexibility
FPCBs offer greater design flexibility compared to traditional rigid PCBs. Their ability to conform to various shapes and sizes allows designers to create more complex and innovative designs. The flexibility of FPCBs enables integration into tight spaces and unconventional shapes, leading to more creative and efficient product designs. This design flexibility is particularly beneficial in applications where traditional rigid PCBs may not be feasible.
Challenges of Flexible Printed Wiring Boards
Despite their advantages, flexible printed wiring boards also face several challenges that must be addressed to ensure optimal performance and reliability.
- Manufacturing Complexity
The manufacturing process for FPCBs is more complex than that for rigid PCBs. The need to handle and process flexible materials requires specialized equipment and techniques. Additionally, ensuring the reliability and consistency of flexible materials can be challenging, as they may have different properties compared to rigid substrates. The complexity of the manufacturing process can impact production efficiency and cost.
- Cost Considerations
FPCBs can be more expensive to produce than rigid PCBs due to the specialized materials and processes involved. The cost of flexible materials and the need for precision in manufacturing can contribute to higher production costs. This cost consideration is significant for large-scale production runs or budget-sensitive projects. Manufacturers must balance the benefits of FPCBs with their associated costs to determine their suitability for specific applications.
- Thermal Management
Managing heat dissipation in flexible printed wiring boards can be more challenging than in rigid PCBs. The flexibility of the material may affect its thermal conductivity and heat dissipation properties. Effective thermal management solutions must be incorporated into the design to ensure reliable performance and prevent overheating. Designers must consider the thermal characteristics of FPCBs and implement appropriate measures to address heat dissipation.
- Mechanical Stress
Although FPCBs are designed to be flexible, they are still subject to mechanical stress during use. Repeated bending and flexing can lead to wear and potential failure of the board. Designers must consider the mechanical stress that the FPCB will experience and incorporate measures to minimize the risk of failure. Proper design and material selection are essential to ensure the long-term durability and reliability of FPCBs.
Future Trends and Developments
The field of flexible printed wiring boards is continually evolving, with ongoing research and development aimed at addressing existing challenges and exploring new possibilities. Some of the key trends and developments in this area include:
- Advanced Materials
Researchers are exploring new materials that offer improved performance and durability for FPCBs. Advanced materials with better thermal and mechanical properties could enhance the capabilities of flexible boards and expand their range of applications. The development of innovative materials may lead to FPCBs with enhanced reliability, flexibility, and performance characteristics.
- Integration with Flexible Electronics
The integration of FPCBs with flexible electronics is a significant area of interest. Flexible electronics, such as organic light-emitting diodes (OLEDs) and flexible sensors, can be combined with FPCBs to create innovative and adaptable electronic systems. This integration could lead to new applications and design possibilities, expanding the potential uses of FPCBs in various industries.
- Improved Manufacturing Techniques
Advancements in manufacturing techniques are expected to address some of the current challenges associated with FPCBs. New methods that streamline the production process and improve the consistency and reliability of flexible materials could lead to more cost-effective and high-quality FPCBs. Innovations in manufacturing technology may enhance production efficiency and reduce costs.
- Environmental Considerations
As environmental concerns continue to grow, there is an increasing focus on developing eco-friendly materials and processes for FPCBs. Sustainable practices and recyclable materials are being explored to reduce the environmental impact of PCB manufacturing and disposal. The adoption of environmentally friendly practices may contribute to the overall sustainability of the electronics industry.
Conclusion
Flexible printed wiring boards have become an integral component in modern electronics, offering unique advantages such as space efficiency, reduced weight, and design flexibility. Their applications span various industries, including consumer electronics, automotive, medical devices, and aerospace. Despite the challenges associated with manufacturing and cost, ongoing advancements and innovations continue to drive the development of FPCBs.
As technology evolves and new materials and processes are explored, the role of flexible printed wiring boards is likely to expand further. Understanding the benefits and challenges of FPCBs is crucial for designers and manufacturers seeking to leverage their unique properties in the development of cutting-edge electronic products. The future of FPCBs holds exciting possibilities, with potential advancements poised to enhance their capabilities and applications across diverse fields.