Aquarite PCB is an electronic control board designed for modern aquariums. It combines advanced electronics with intelligent management and is designed to enhance the functionality and enjoyment of the aquarium. This board integrates a variety of functions such as LED lighting control, water quality monitoring and automatic feeding, providing users with a comprehensive aquarium management experience.
Its features include high integration, intelligent management and energy saving. Through the diversified performance of LED lighting, it creates fascinating visual effects for the aquarium and increases the ornamental features. It also monitors and adjusts water quality parameters in real time to ensure that fish live in an optimal environment. In addition, the pcb utilizes high-quality materials and advanced production processes to ensure product stability and reliability.
The circuit board is the core component of the Aquarite PCB, so its material selection must meet high insulation, water and corrosion resistance. Typically, high-quality insulating materials, such as polyimide (PI) or polytetrafluoroethylene (PTFE), are used to make circuit boards. These materials have good electrical properties and chemical stability, which ensures that the circuit boards remain stable and safe during long-term operation in the aquarium.
The electronic components on the PCB, such as sensors, control chips and LEDs, must also be able to withstand the humid environment in the aquarium. Therefore, all components must be selected as water and corrosion resistant types to ensure that they will work stably for a long period of time in the aquarium environment. At the same time, these components also need to comply with relevant electronics industry standards to ensure their quality and reliability.
In addition, the shell not only plays a protective role, but also affects the appearance and durability of the product. Therefore, the shell material must have good waterproof, scratch-resistant and UV-resistant properties. Common housing materials include waterproof plastic, aluminum alloy or stainless steel. These materials resist moisture, salt and UV radiation in the aquarium and maintain the appearance and performance of the product.
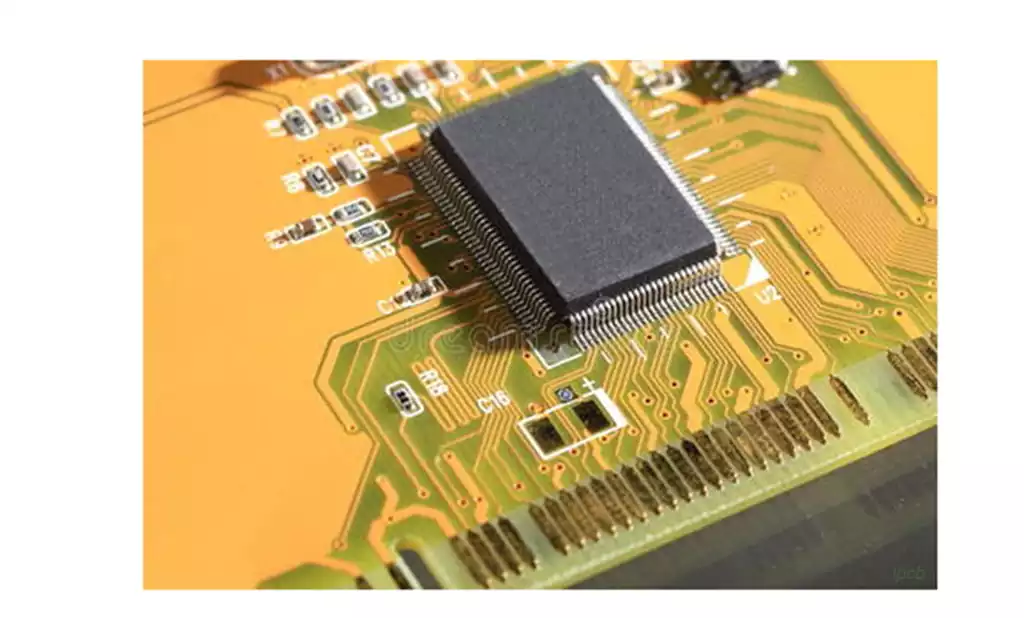
The Aquarite PCB process is a complex and delicate process designed to ensure that each board meets high quality standards:.
Substrate Cutting: The substrate is cut to the desired working size according to the design requirements. This step involves both cutting and grinding processes to ensure the exact size and flatness of the substrate.
Inner layer circuit fabrication:
Pre-treatment: Remove oil and oxides from the surface of the substrate to increase its roughness and contact area. Commonly used methods include brushing, sandblasting and chemical methods.
Inner layer coating: Coating the surface of copper foil with liquid photographic corrosion-resistant ink to form the pattern of the inner layer line.
Exposure: The pattern on the negative is transferred to the photosensitive substrate by means of a light source.
Developing: Using a weak base to react with the unsensitized ink to transfer the graphic to the substrate.
Etching: Removal of the copper layer unprotected by the ink using a weak acid to form the inner layer of the line graphic.
Deprocessing: Removes the photopolymerized ink protecting the line surface with a strong base.
CCD Punching: Punch out the required inspection holes and rivet holes using CCD positioning system.
AOI Inspection and VRS Inspection: Quality checking by Automatic Optical Inspection (AOI) and Verification Rework Station (VRS).
Press-fitting:
Browning: Increase the contact area of the copper surface and its wettability to the flowing resin by chemical treatment.
Riveting/pre-stacking: pre-stacking multiple inner laminates together using rivets to ensure stability during subsequent processing.
Pressing: Pressing of laminated boards into multi-layer boards by hot pressing.
Milling and thinning: Preliminary profiling of the laminated boards.
Drilling: Drill holes on the surface of the board for the connection between layers.
Plating: Perform hole copper plating to metallize the resin and fiber of the non-conductor part of the hole wall to facilitate the subsequent plating process.
Outer layer circuit fabrication:
Pre-treatment: Remove copper surface contaminants and increase the roughness and contact area of the copper surface.
Pressing dry film: Pressing dry film tightly on the surface of copper foil by hot pressing method.
Exposure: Transfer the line pattern on the film to the copper foil dry film by strong light.
Developing: Remove the dry film without polymerization reaction by using weak alkali to make the desired line pattern appear.
Etching: Removal of copper foil not protected by the dry film with weak acid.
De-filming: Remove the dry film of photopolymerization using strong alkali.
Outer layer inspection: Perform AOI inspection, VRS inspection, O/S electrical test, copper thickness measurement, impedance test and outer layer line width measurement.
Solder Resist Paint Process: Includes pre-treatment, painting and exposure development steps to protect the parts that are not to be soldered during soldering.
Text Printing: Printing the desired text, logo or part symbols on the board surface.
Surface treatment: Surface treatment of copper surfaces, such as electroless gold (chemical nickel gold) or gold plating, to enhance their solderability and insertion/removal properties.
Molding: Cut the PCB into the size required by the customer.
Electrical Test & Shipping Inspection: Perform flying probe test, special tester test, etc. to ensure the product meets the quality standard. Common defect inspections include short circuits and broken circuits.
Aquarite PCB is not only a technologically advanced aquarium device, but also a perfect combination of technology and aquarium life.