Solder beads refer to the small spherical or dotted solder that appears on the pads or on the metal layer on the backside after SMT circuit board assembly. The diameter of the bead is roughly between 0.2mm and 0.4mm, but there are also more than this range, mainly concentrated around the chip resistive components. The presence of solder beads not only affects the appearance of electronic products, but also causes hidden danger to the quality of the product. The reason is that the high density of modern printed circuit board components, small spacing,solder beads in the use of the process may fall off, resulting in short-circuit components, affecting the quality of electronic products.
A number of industry standards explain the problem of ‘solder beads’. The main MIL-STD-2000 standard ‘does not allow tin beads’, and IPC-A-610C standard ‘less than 5 per square inch’. In the IPC-A-610C standard, the minimum insulation gap of 0.13 mm,the diameter of the bead within the bead is considered to be qualified; while the diameter of the bead is greater than or equal to 0.13 mm beads are unqualified,the manufacturer must take corrective action to avoid this phenomenon.The latest version of the IPCA 610D standard for lead-free soldering does not provide for clearer regulation of beads, and the requirement for fewer than 5 beads per square inch has been removed. The standards for automotive and military products do not allow any ‘beads’ and the boards used must be cleaned after soldering or the beads removed by hand.
Principle of solder beads formation
1.Surface tension and wettability:
When solder paste is heated to melting point, liquid tin is formed. Since liquid tin has surface tension, it will try to reduce the surface energy, thus forming a spherical shape. If the PCB surface or component pins are not completely wetted by the liquid tin, solder beads will form in the unwetted areas.
2.Flux activity:
The main role of the flux is to remove oxides and contaminants on the PCB surface to improve the wettability of the solder paste. Insufficient or inappropriate flux activity, can not effectively remove oxides, will lead to solder paste can not completely wet the PCB surface, increasing the risk of solder beads formation.
3.Airflow impact:
In a reflow oven, the flow of air can have an effect on liquid tin. Improper airflow settings or PCB layout may cause the airflow to be too strong in certain areas, blowing the liquid tin and forming beads. In addition, temperature gradients in the reflow oven may also create airflow that affects paste flow and wettability.
4.PCB design factors:
The size, shape and spacing of the pads in the PCB design have a significant impact on the formation of solder beads. Too large or too small pad size, uneven pad shape or too close to the component spacing may lead to uneven distribution of solder paste, increasing the possibility of the formation of solder beads. PCB through holes, holes, etc. may also trap solder paste, the formation of tin beads during reflow.
5.Component pin design:
Component pin shape,length and surface treatment will also affect the wettability of solder paste.Overly long or short pins,uneven or oxidised pin surfaces may result in solder paste not being able to wet completely, resulting in the formation of solder beads. The design of some component pins may result in a large gap between the pin and the PCB, which can easily accumulate solder paste and form beads during reflow.
6.Reflow oven temperature profile:
Inappropriate reflow oven temperature profile settings may result in incomplete melting of solder paste or uneven reflow. Excessively fast heat-up rates, too long or too short holding times, and inappropriate cooling rates may affect paste flow and wettability, increasing the risk of bead formation. The temperature profile should be optimised according to the characteristics of the solder paste and components to ensure that the solder paste can be completely melted, evenly reflowed and form a good solder joint.
7.PCB surface treatment:
Oxidation, contamination or other poor treatments on the PCB surface can reduce the wettability of the solder paste. Common PCB surface treatments such as chemical nickel/gold plating,hot air levelling,organic solderability protection flux (OSP), etc., can lead to the formation of solder beads if they are improperly treated or contaminated during storage and handling. Ensure that the PCB surface treatment is of good quality and avoid contamination during storage and operation.
8.SMD accuracy:
Poor placement accuracy can cause components to shift or tilt, affecting paste distribution and flow. This can cause solder paste to build up in certain areas and form solder beads. Improve the accuracy and stability of the placement equipment to ensure that components are accurately placed on the PCB.
9.Solder paste quality and application method:
The quality of the solder paste also has an effect on the formation of solder beads. Low-quality solder paste may contain impurities, unstable viscosity, or inaccurate metal content, resulting in the formation of solder beads. Store and use solder paste correctly to avoid contamination or expiration.
10.Production environment:
Environmental conditions in the production plant such as temperature,humidity and cleanliness can also have an effect on the formation of solder beads. Excessive humidity may cause solder paste to absorb moisture and reduce its performance. Keep the production environment stable and clean, and control the humidity within the appropriate range.
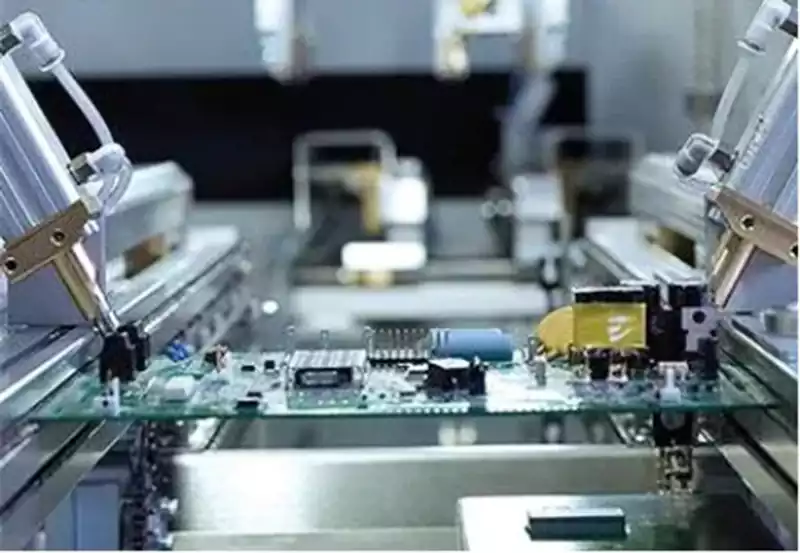
solder Methods and experiences to reduce the generation of solder beads
1.Select the solder paste suitable for the product process requirements
The selection of solder paste directly affects the quality of welding. The content of the metal in the solder paste, the oxidation of the paste, the particle size of the alloy solder powder in the paste and the thickness of the solder paste printed to the pad will affect the generation of tin beads. In the selection of solder paste, should adhere to the existing process conditions under the trial, so that both the supplier can verify the applicability of the solder paste on their own products, processes, but also a preliminary understanding of the specific performance of the solder paste in actual use.
2.Design stencil opening according to standard requirements
Correctly select the thickness of the stencil,strictly control the opening ratio of the stencil. Usually in the case of ensuring the quality of the solder joints, the choice of the thickness of the steel should be based on the PCB board pin spacing on the smallest device to determine the preferred thickness of the thinner stencil,try to avoid choosing a thicker piece of steel.The way the stencil is opened and the shape of the opening may cause some defects in the printing and soldering of the solder paste,thus causing tin beads.If the opening is not proper, when printing solder paste,it is easy to print the solder paste onto the solder resist layer,thus producing solder beads during reflow soldering.In order to solve this problem, without affecting the quality of the solder joints, we try to reduce the opening of the stencil than the actual size of the pad by 10%,the experiment proved that the appropriate reduction of the stencil opening size can effectively reduce the generation of solder beads.In addition,the shape of the stencil opening can be changed to achieve the desired effect.
3.Reduce the patch pressure
Patch pressure is also an important cause of solder beads, usually unnoticed. The influencing factors are the setting of PCB thickness in the programme item, the setting of component height in the package item and the setting of suction nozzle pressure of the mounter. If the mounting pressure is too large, it will cause the component to be attached to the PCB for a moment, the solder paste will be extruded to the pad outside or extruded to the component below the soldermask on the layer, these are extruded out of the pad outside of the solder paste in the reflow soldering will cause the solder bead. The solution to the problem is to reduce the mounting pressure to avoid solder paste is squeezed to the outside of the pad. The principle of controlling the patch pressure is just enough to be able to ‘put’ the components in the solder paste and press down on the appropriate height, the appropriate height is not to be able to squeeze the solder paste out of the pad outside!
4.Improve the components and pad solderability
Components and pads of the solderability of the solder beads also has a direct impact on the production. If the components and pads of the oxidation degree is serious, the accumulation of excessive oxides in the metal plating will consume some flux, soldering and wetting is not sufficient, will also cause the generation of tin beads. Therefore, it is necessary to ensure the incoming quality of components and PCBs.
5.Optimise the furnace temperature profile
Tin beads are generated when the PCBA passes through reflow soldering. Reflow soldering can be divided into four stages: preheating, holding, reflow, cooling. In these four stages, the preheating, holding stage is to reduce the thermal shock of the PCB and components to ensure that the solvent of the solder paste can be partially evaporated when the role of the solder paste, rather than in the reflow soldering, due to the rapid rise in temperature appears too much solvent, causing collapse or splash, resulting in the solder paste rushed out of the pad, the formation of tin beads or tin balls. The solution to this problem is to control the temperature of reflow soldering, in the preheating stage, the temperature rise can not be too fast, the rate of temperature rise is generally controlled in the 2 ° C / S below the moderate position, so that the temperature of the solder paste and components and pads rose to 120 ° C ~ 150 ° C between, reducing the components in the reflow of the thermal shock. Holding time is controlled within 60-120S, so that the solvent can be in a good platform to most of the volatile away. At this stage, the flux in the solder paste begins to vaporise and evaporate, which may cause small particles of metal to separate and run underneath the component, and then run around the component to form tin beads during reflow. If the temperature rises too quickly it is easy to cause the solder to splash and form tin beads. Therefore, take a more moderate preheating temperature and preheating speed can control the generation of solder beads.
6.Reduce the influence of external factors
General solder paste printing the best temperature of 18 ~ 28 ℃, relative humidity of 40 ~ 70% (with the characteristics of the paste). Temperature is too high, so that the viscosity of the solder paste is reduced, easy to produce slump; humidity is too high, the paste is easy to absorb moisture, easy to splash, which is the cause of solder beads. Therefore, it is necessary to control the temperature and humidity of the workshop.
Solder beads problem is a big challenge in SMT board assembly, but by optimising key aspects such as solder paste selection, stencil design, placement process, oven temperature profile and production environment, we can effectively control and reduce the generation of tin beads. Continuous efforts and fine process control are the key to ensure the quality and reliability of SMT boards.