How to choose between ceramic pcb vs fr4? This article will show you how to choose.
Ceramic pcb: a circuit board made of ceramic material, also known as ceramic PCB (Printed Circuit Board). Unlike the common glass fiber reinforced plastic (FR-4) substrate, ceramic circuit board uses ceramic substrate, which can provide higher temperature stability, better mechanical strength, better dielectric properties and longer life. Ceramic circuit boards are mainly used in high temperature, high frequency and high power circuits, such as LED lights, power amplifiers, semiconductor lasers, RF transceivers, sensors and microwave devices.
Circuit board: a basic material for electronic components, also known as circuit board, PCB board (Printed Circuit Board) or printed circuit board. It is a carrier that prints metal circuit patterns on non-conductive substrates and then makes conductive paths and assembles electronic components through chemical corrosion, electrolytic copper, drilling and other processes.
Application fields are divided by materials:
Alumina ceramics (Al2O3): It has excellent insulation, high temperature stability, hardness and mechanical strength, and is suitable for high-power electronic devices.
Aluminum nitride ceramics (AlN): have high thermal conductivity and good thermal stability, suitable for high-power electronic equipment and LED lighting and other fields.
Zirconia ceramics (ZrO2): have high strength, high hardness and wear resistance, suitable for high-voltage electrical equipment.
From the process division:
HTCC (high temperature co-fired ceramics): suitable for high temperature and high power applications, such as power electronics, aerospace, satellite communications, optical communications, medical equipment, automotive electronics, petrochemical and other industries. Product examples include high-power LEDs, power amplifiers, inductors, sensors, energy storage capacitors, etc.
LTCC (low temperature co-fired ceramics): suitable for the manufacture of microwave devices such as RF, microwave, antennas, sensors, filters, power dividers, etc. In addition, it can also be used in medical, automotive, aerospace, communications, electronics and other fields. Product examples include microwave modules, antenna modules, pressure sensors, gas sensors, acceleration sensors, microwave filters, power dividers, etc.
DBC (direct copper ceramics): suitable for heat dissipation of high-power power semiconductor devices (such as IGBT, MOSFET, GaN, SiC, etc.), with excellent thermal conductivity and mechanical strength. Product examples include power modules, power electronics, electric vehicle controllers, etc.
DPC (Direct Copper Multilayer Printed Circuit Board): Mainly used for heat dissipation of high-power LED lamps, with the characteristics of high strength, high thermal conductivity and high electrical performance. Product examples include LED lamps, UV LEDs, COB LEDs, etc.
LAM (Hybrid Ceramic Metal Laminate): Can be used for heat dissipation and electrical performance optimization in high-power LED lamps, power modules, electric vehicles and other fields. Product examples include LED lamps, power modules, electric vehicle motor drivers, etc.
Fr4
IC substrates, rigid-flex boards and HDI blind buried via boards are all commonly used PCB types, which are used in different industries and products, as follows:
IC substrate: IC substrate is a commonly used printed circuit board, mainly used for chip testing and production in electronic devices. Common application industries include semiconductor production, electronic manufacturing, aerospace, military and other fields.
Rigid-flex board: Rigid-flex board is a composite material board that combines a flexible circuit board with a rigid circuit board, and has the advantages of both flexible and rigid circuit boards. Common application industries include consumer electronics, medical equipment, automotive electronics, aerospace and other fields.
HDI blind buried via board: HDI blind buried via board is a high-density interconnect printed circuit board with higher line density and smaller aperture to achieve smaller packaging and higher performance. Common application industries include mobile communications, computers, consumer electronics and other fields.
Ceramic pcb vs fr4 material: Which one should we choose?
How to choose between traditional FR4 material and Rogers PCB material, mainly consider the following five points:
- Impedance control
Supplier customers may be confused when choosing FR4 Rogers PCB material for special projects. Here I would like to take radar PCB as an example to talk about the manufacturing issues of FR4 Rogers PCB material. For example, radar PCB will have stricter control over impedance, which is a very important factor for radar equipment. Matched impedance can produce cleaner signal transmission. Previously, the tolerance of signal-carrying wiring standards was ±8-10%. This indicator is no longer good enough for today’s high-frequency and high-speed circuits. Today, the required tolerance is ±6-8%. In some cases, the tolerance even reaches ±5% or less.
This parameter change will help to manufacture radar PCBs with particularly tight impedance control, but it will also limit the number of manufacturers who can manufacture these PCBs, because tolerances less than 5% are difficult to produce. But at Viasion, we can provide high-frequency PCBs with impedance tolerances less than 5%.
Using Rogers’ UHF PCB materials for lamination, the tolerance of the dielectric constant is maintained at ±2%, and some products can even reach ±1%. In contrast, the dielectric constant of FR4 laminates is as high as 10%. Therefore, regarding the comparison of Rogers and FR4 PCB materials, you can also find that the insertion loss of Rogers materials is very low, which may be less than 0.001. And the transmission loss and insertion loss of Rogers laminates are almost 50-80% lower than traditional FR4 materials. Therefore, Rogers PCB products are often used in microwave and RF applications.
- Cost-effectiveness
Many times, cost is what customers value most, and Rogers materials are much more expensive than FR4 materials, but Rogers’ prices are not inflated, and they can provide relatively low loss and high-frequency lamination performance at an acceptable price.
For commercial applications, Rogers materials can also be used with FR4 materials to reduce the overall cost, but both meet high-frequency PCB requirements. We can use all FR4 Rogers hybrid PCBs.
Usually the dielectric between the top/bottom layer and the next inner layer uses Rogers materials, while other layers use FR4 materials for lamination. But when you choose Rogers materials for stacking, frequency is the primary factor that should be considered.
- Electromagnetic frequency
Electromagnetic frequency is also a factor in Rogers vs. FR4 printed circuit board materials. When the frequency exceeds 500MHz, PCB designers tend to choose Roger materials, especially for RF circuit boards or microwave circuit boards, because Rogers materials can provide higher performance when the upper layer wiring requires strict impedance control. In addition, Rogers materials can also provide lower dielectric loss. Their dielectric constant is stable even over a wide frequency range.
In addition, Rogers can also provide ideal low insertion loss performance for our radar, radio, antenna and other electronic products that require high-frequency operation.
- Coefficient of Thermal Expansion (CTE)
Rogers 4000 series materials have excellent coefficient of thermal expansion (CTE) dimensional stability compared to ordinary FR4 materials. Compared with ordinary FR4 materials, when the PCB experiences cold environment, hot environment and multiple reflow cycles, the thermal expansion and size of the circuit board can still remain at a stable limit at higher frequency and higher temperature cycles, so when you need the product to have high dimensional stability, you can consider using Rogers materials. The above is a CTE comparison between Rogers and FR4 PCB materials.
- Electrical performance
The TG of general FR4 materials is around 135~150, which cannot meet very reliable electrical performance, while high-performance FR4 materials have good reliability, such as high TG materials above TG170, such as our commonly used Shengyi S1170, S1000-2, and even S1190 TG has reached 200.
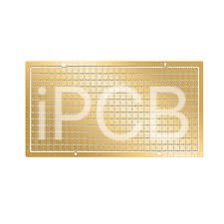
1) High temperature resistance: Ceramic circuit boards can withstand temperatures up to 1000°C, while traditional circuit boards can usually only withstand temperatures of 100-200°C.
2) Thermal conductivity: The thermal conductivity of ceramic circuit boards is usually 3-5 times that of traditional circuit boards. For example, the thermal conductivity of alumina ceramics (Al2O3) is 30 W/mK, while the thermal conductivity of fiberglass boards (FR-4) is only 0.2 W/mK.
3) Dielectric constant: The dielectric constant of ceramic circuit boards is usually between 5-10, while the dielectric constant of traditional PCBs is usually between 4-6. This means that ceramic circuit boards can provide better signal transmission quality.
4) Strength and hardness: Ceramic circuit boards are usually harder and more durable than traditional circuit boards because they are made of ceramic materials. For example, the strength of alumina ceramics is more than 10 times that of ordinary glass and the hardness is twice that of ordinary glass.
5) Corrosion resistance: Ceramic circuit boards have excellent corrosion resistance and can be used in strong acid and strong alkali environments. For example, alumina ceramics can operate stably for a long time in strong alkaline acid solutions such as HF, NaOH and KOH, while traditional PCBs are easily corroded.
6) Size and weight: Ceramic printed circuit boards can be made very thin and very small, thereby achieving higher integration and smaller size. At the same time, ceramic printed circuit boards are also light in weight.
Application of Ceramic pcbs
Ceramic circuit boards have the advantages of high temperature resistance, high frequency, high strength, high reliability and low dielectric constant, so they are widely used in the following fields and industries:
- Aerospace: Ceramic pcbs can withstand extreme temperatures and high radiation environments, so they are widely used in aerospace fields such as satellites, missiles and aircraft.
- Military: Ceramic pcbs are also widely used in military radars, missiles, fighters and other applications that require high temperature, high pressure and high radiation.
- Medical devices: Ceramic pcbs are antibacterial, high temperature resistant and corrosion resistant, which can meet the requirements of medical devices for high quality and reliability, such as widely used in cardiac pacemakers, prostheses and high-pressure syringes.
- Electronic products: Ceramic pcbs are suitable for high-speed, high-frequency and high-power electronic products such as mobile phones, tablets, LED lights, etc.
- New energy: Ceramic pcbs can also be used in new energy fields such as solar energy and wind energy, such as solar panels, wind turbines, etc.
- Other fields: Ceramic pcbs are also suitable for industrial control, automotive electronics, high-speed trains, communications and other fields.
FR4 Rogers hybrid PCBs can also be selected. In the case of mixed stacking in PCB manufacturing, Rogers PCB materials can be easily mixed with high-performance FR4 for production using general manufacturing technology. Therefore, it is not difficult to achieve high manufacturing quality.
Overall, by reading the above information, I believe you already have the answer about ceramic pcb vs fr4 material. The choice of FR4 Rogers PCB material is different in different situations, and ultimately it is for cost-effectiveness.