Circuit board assembly machine is a very important equipment in the semiconductor industry, which is mainly used to automate the assembly of electronic components and circuit boards. According to its different assembly methods, circuit board assembly machine can be divided into two types: surface mount assembly machine and through-hole assembly machine.
Surface mount assembly machine is an important equipment in modern electronic assembly line, mainly used for electronic components accurately and quickly mounted to the printed circuit board (PCB) on the designated position. The working principle of surface mounting machine mainly relies on high-precision visual recognition system and precise mechanical motion control system. In the working process, the surface mounting machine firstly identifies the marking points on the PCB and the position of the components through the vision system, and then calculates the mounting coordinates of the components. Then, the mechanical arm accurately removes the components from the feeder according to the calculated coordinates and mounts them on the corresponding position of the PCB board. The whole process is fast and accurate, greatly improving the assembly efficiency and quality of electronic products.
Surface mount machines are widely used in various fields such as consumer electronics, communications, automotive electronics, aerospace and so on. In the field of consumer electronics, with the popularity of smart phones, tablet PCs and other products, surface mounting machines play an important role in assembling high-density, high-precision circuit boards for these products. In the field of communications, the rapid development of 5G, the Internet of Things and other technologies has put forward higher requirements for the performance and reliability of electronic equipment, and the application of surface mounting machines has further enhanced the manufacturing level of communications equipment.
A through-hole assembly machine is a device used to mount through-hole components onto a printed circuit board (PCB). The leads of the through-hole components are passed through drilled holes in the PCB and then fixed to the board by wave soldering or hand soldering. This type of assembly is suitable for application scenarios that require high reliability and mechanical strength.
A through-hole assembly machine usually consists of the following parts:
Feeding system: responsible for delivering the through-hole components to the assembly position.
Positioning system: ensures that the components are accurately aligned with the drilled holes on the PCB.
Soldering System: Secures the component to the PCB using wave soldering or hand soldering.
Inspection System: Ensures the quality of the soldering and the accuracy of the component position.
The principle of operation is that the components are sent to the positioning system through the feeding system, the positioning system ensures that the components are aligned with the drilled holes on the PCB, then the soldering system completes the soldering process, and finally, the inspection system checks the quality of the soldering and the accuracy of the position.
Advantages and Disadvantages of Through-Hole Assembly Machines
Pros:
Strong mechanical bond: through-hole assembly creates a stronger connection by flowing solder through the board, increasing durability and reliability
Suitable for high-stress environments: for applications that are subject to high mechanical or environmental stresses
Easy to manually adjust and replace: suitable for testing and prototyping
Disadvantages.
Higher cost: leads through holes in the board are very time consuming, resulting in higher costs
Wiring space constraints: drilled holes must cover all layers of the board, limiting the wiring space for multilayer PCBs
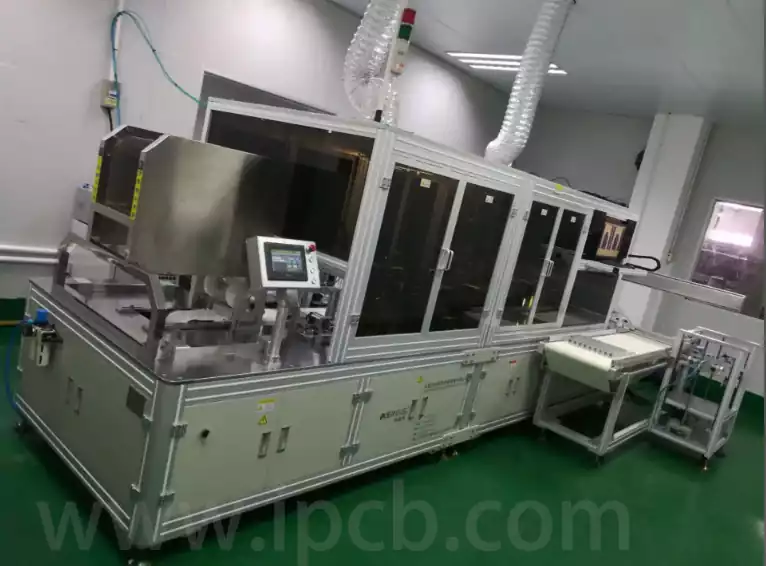
Circuit board assembly machine works mainly through the following principles:
Component placement principle
Visual recognition and positioning
High-precision cameras are used to take pictures and image the designated placement locations on the circuit board. These cameras capture characteristic information such as marking points, line patterns, etc. on the circuit board. For example, in a double-sided circuit board, the camera can accurately identify the placement coordinates of different components on the front and back sides.
An image recognition algorithm then compares the captured image with a circuit board design template pre-stored in the system. The algorithm calculates the deviation of the actual placement position from the design position with an accuracy of ±0.01 mm or even higher.
Component pick and place
For small components, such as resistors and capacitors, assembly machines usually use the vacuum adsorption principle. A precision pneumatic device generates negative pressure so that the suction nozzle can firmly absorb the components. The size of the suction nozzle is customised according to the size of the different components. For example, for resistors of size 0402 (length 0.4 mm, width 0.2 mm), a very small diameter suction nozzle is used.
After sucking up the component, it is accurately placed on the circuit board by means of a high-precision motion control system according to the coordinate position determined by the vision recognition system. The motion control system consists of motors, guide rails and transmission components that enable precise movement in the X, Y and Z directions, with the X and Y directions responsible for in-plane positioning and the Z direction responsible for component lifting and lowering operations.
Welding Principle
Wave soldering (for double-sided circuit boards)
When one side of a double-sided circuit board has been attached to a component, the other side needs to be attached and soldered as well. Wave soldering is used for the manual soldering part of a double-sided board or for large components that need to be inserted manually on both sides of a double-sided board.
The component-placed boards are first fixed on a conveyor belt and slowly passed through a wave of molten solder. The melted solder evenly covers the pins of the hand-inserted components and the solder joints of the circuit board to achieve a soldered connection. Parameters such as temperature, speed and amount of solder need to be precisely adjusted to the different board materials and component requirements.
Reflow Soldering (for surface mount components)
After the surface mounted components are placed on the board, they need to be soldered in a reflow oven. Inside the reflow oven there are several heating zones, usually including a preheating zone, a holding zone, a reflow zone and a cooling zone.
In the preheating zone, the flux on the circuit board begins to evaporate, removing oxides from the component pins and the solder paste surface; the holding zone maintains a certain temperature to further activate the flux in the solder paste; the reflow zone has the highest temperature, melting the solder paste and soldering the component pins to fix them on the circuit board; and the cooling zone allows the soldered components and circuit board to cool and solidify quickly, forming a stable soldered connection.
Benefits of upgrading the circuit board assembly machine
- Improve production efficiency
Circuit board assembly machine can automatically complete the precise assembly of electronic components, significantly improve production efficiency, and reduce the time and cost of manual operation.
2.Reduce Costs
Through the automatic assembly of circuit board assembly machine, it can reduce the labour cost, reduce the scrap rate and maintenance cost, thus reducing the overall cost.
- Enhance product quality
The automated assembly of circuit board assembly machine can ensure the precision and consistency of assembly, thus improving the quality and stability of products.
In the wave of the semiconductor industry moving towards intelligence and high precision, circuit board assembly machine, as the core hub connecting design and manufacturing, are reshaping the underlying logic of electronics manufacturing with continuously evolving technological capabilities. In the future, with the 5G communications, automotive electronics, industrial Internet of Things and other emerging areas of circuit board complexity and yield requirements, circuit board assembly machine will further integrate digital twin, machine learning and other cutting-edge technologies.