Circuit board conformal coatings are specialized polymer film-forming products that protect circuit boards, components and other electronic devices from adverse environmental conditions. These coatings are not limited by the PCB structure or other environmental factors, but provide a higher dielectric resistance to protect the board from corrosive environments, humidity, and contaminants such as dirt and dust.
There are 5 common types of conformal coatings. How to choose the right coating for your application?
Acrylic Adhesives
Acrylic adhesives are readily soluble in many organic solvents, making it easy to complete repairs to circuit boards and often providing only selective chemical resistance. Acrylic adhesives offer the advantages of quick drying, good mold and mildew resistance, no shrinkage during curing and good moisture resistance. However, the disadvantages include low abrasion resistance and susceptibility to scratching, chipping and peeling.
Epoxy resins, two-component
Epoxy resins are usually two-component compounds that begin to cure when mixed. Epoxies have good abrasion and chemical resistance properties, as well as reasonable moisture resistance. However, these coatings are difficult to remove and rework. Because film shrinkage occurs during polymerization, the use of buffers around precision components is recommended. Curing at low temperatures minimizes shrinkage.
Polyurethanes
Polyurethanes offer good moisture resistance and chemical resistance. Because of their good chemical resistance, removal of coatings requires the use of strippers (which may leave ionic residues). These residues may need to be thoroughly cleaned to prevent corrosion of the pcb substrate. Polyurethanes can be reworked by welding, but usually produce a brown residue that affects the appearance of the product.
Silicones
Silicones are usually a single compound that will begin to cure when exposed to moisture in the air and at a certain temperature. Silicones have good wettability and adhesion on all surfaces of electronic materials or modules after curing. It can be widely used in high temperature (>120°C), moisture sensitive, chemical resistant, corrosive and anti-fungal environments.
Ethyl Carbamate
Ethyl Urethane has strong protective properties, hardness and high solvent resistance, providing excellent abrasion resistance and low moisture permeability. It also has good low-temperature adaptability, but does not work well in high-temperature environments and most cannot be repaired or reworked.
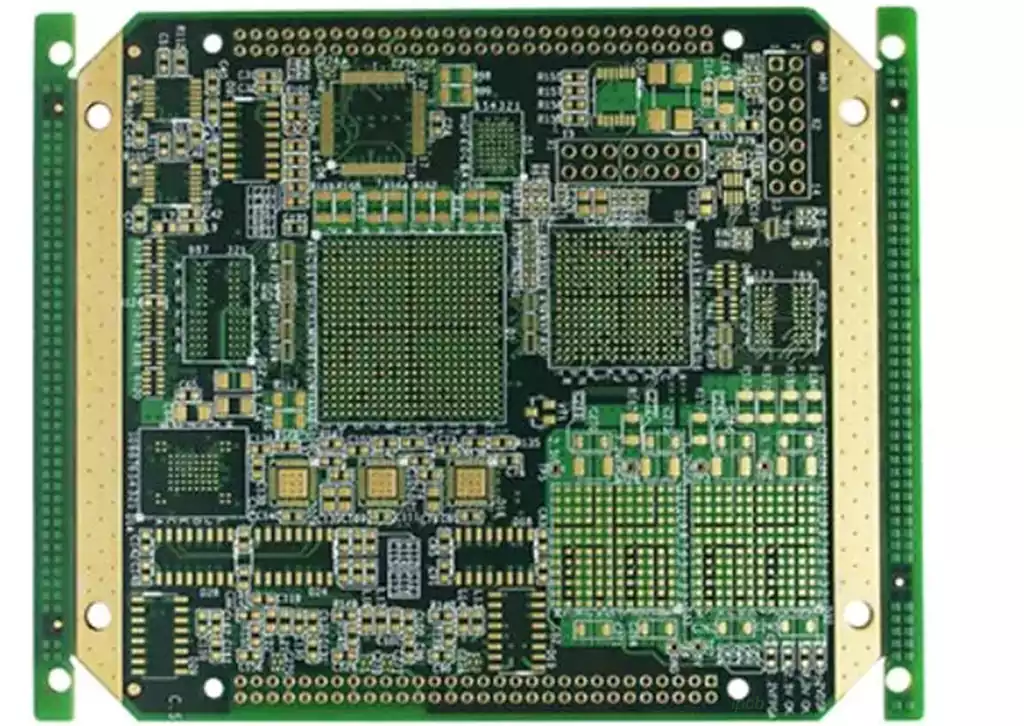
Role of Conformal Coating for Printed Circuit Boards.
Protects electronic circuits from harsh environments that may contain moisture and chemical contaminants such as humidity, fungus, dust, and rust.
Prevents damage to circuit boards during fabrication, assembly and use, reduces mechanical stress on components and protects them from thermal oscillations.
Reduces wear and tear during use and improves the friction and solvent resistance of circuit boards and components.
Reinforces the board’s performance, allowing greater component density due to the increased dielectric strength between conductors from the conformal coating, preventing solder joints and conductors from erosion.
Withstand higher electric fields in high component density designs, allowing for smaller battery pack designs with higher voltages due to the insulating effect of the coating.
Releases stress caused by cyclical temperature changes, improving the stability of electronics and extending service life.
Circuit board conformal coating plays a vital role in electronic products as an important protector of circuit boards. Its appearance not only improves the reliability and stability of circuit boards, but also promotes the development of the entire electronics industry.