A cold solder joint is a soldering phenomenon that occurs when the required minimum wetting temperature between the brazing material and the base metal is not reached, or when the metallurgical reaction fails to proceed adequately despite the fact that wetting occurs in some localised areas. When this phenomenon occurs, it means that there is no problem with the solderability of the PCB (Printed Circuit Board) and the components on it per se, but that the root of the problem lies in the fact that the temperature conditions during the soldering process are not ideal.
The main reason for cold solder joint is that insufficient heat is supplied during soldering, resulting in a soldering temperature that does not reach the required wetting temperature of the brazing material, which prevents the formation of a sufficiently thick IMC (Intermetallic Compound) at the bonding interface, or an IMC layer that is too thin. In some cases, cracks may even appear at the bonding interface.
Analysis of the extent of cold solder joint defects
Minor cold soldering phenomena constitute a potential defect that is unlikely to significantly affect the normal functioning of a product under conventional environmental conditions of use,even over a considerable period of time.The growth of IMC (intermetallic compounds) is not only affected by temperature, but also has a close relationship with time.While IMC formation may not be complete at the time of reflow soldering,it has the ability to continue to grow and develop during subsequent use of the product,albeit relatively slowly. In order to accurately judge the degree of cold welding,we refer to actual ERSACOPE observations and tentatively classify them into three classes based on their appearance: Class A (slight cold welding), Class B (moderate cold welding),and Class C (severe cold welding).
Reasons for inducing cold solder joints and their countermeasures
- μBGAs and CSPs face high cold solder joint rates in hot air reflow soldering.
Hot air convection soldering technology relies on air as the heat transfer medium, and is particularly suitable for heating components that ‘protrude’ from the PCB surface, such as high-pin components and small components. However,a key issue in this process is the ‘surface layer’ formed between the convection air and the PCB surface. When the gap between components such as μBGAs and CSPs and the PCB surface narrows to a thickness close to that of the attached layer, it is difficult for the hot air to effectively penetrate to the bottom gap of these components, resulting in a significant reduction in the efficiency of heat transfer to the bottom pad area of the μBGAs and CSPs.
At the same peak temperature and reflow time, the solder ball joints of μBGAs and CSPs receive significantly less heat compared to components with cold solder joints that are well exposed to hot air. This results in some of the μBGA and CSP bottom ball joints not reaching the required wetting temperature, leading to cold soldering problems. In this soldering process,heat is first transferred to the μBGA, CSP package body and PCB board,and then gradually heats up the pads and the braze balls of the μBGAs and CSPs by thermal conduction of these materials, ultimately forming a cold solder joint.For example,when the 240 ℃ hot air on the surface of the package body,pads and μBGA,CSP brazing ball will gradually warm up,but their temperature rise rate compared to other components will have a lag. If the required wetting temperature cannot be reached within the specified reflow time, cold soldering will occur.
- Possible solutions for the high incidence of cold soldering in μBGAs and CSPs
1) Implement a trapezoidal temperature profile strategy (i.e., extend the peak temperature maintenance period) and moderately reduce the peak temperature of reflow soldering.This practice helps to reduce the temperature difference between high and low heat capacity components and prevents small components from being damaged by excessive temperature.Modern advanced composite reflow soldering systems are able to significantly reduce the temperature difference between 45mm BGAs and small pin packages (such as SOPs) to within 8°C.
2) Optimising heat transfer in reflow soldering
The reflow soldering process involves firmly soldering thousands of components to a PCB substrate. When a PCB carries components of varying quality, heat capacity and area, uneven temperature distribution becomes a significant problem. Currently, within the industry, the two most common re-flow heat transfer methods and their characteristics are outlined below.
① Forced convection heating technology: This is a reflow soldering method that uses convection jet nozzles to force the airflow to circulate, thus heating the soldered component.Under this heating method,the temperature of the PCB substrate and components tends to be close to the set temperature of the gas in the heating zone,effectively solving the infrared heating due to differences in component surface colour, reflectivity and other factors triggered by a large temperature difference between the components. However,in terms of heat exchange efficiency,the heat transfer performance of forced convection heating is not as good as that of infrared heating,so its productivity is relatively low and energy consumption is high.In addition, due to the lower heat transfer efficiency, the size difference of the components can lead to a large difference in their warming rate.In forced hot air convection reflow soldering equipment,the convection speed of the circulating gas is critical.In order to ensure that the circulating gas can be fully applied to each area of the PCB,the airflow must have sufficient velocity or pressure.However,this may also lead to a certain degree of vibration of the thin PCB substrate,and even cause the displacement of components.
② Infrared heating technology: Infrared (IR) refers to electromagnetic waves with wavelengths between 3 and 10 microns. Typically, PCB boards, fluxes, and component encapsulation materials are composed of molecular layers formed by atoms bonded chemically.The molecules within these polymers vibrate continuously,including stretching and angular shifts.When the vibration frequency of these molecules matches a similar infrared electromagnetic wave,the molecules resonate and the vibration becomes more intense.This intense vibration is converted into thermal energy,allowing heat to be transferred quickly and evenly throughout the object in a short period of time.As a result,the object is fully heated without having to rely on an external high-temperature heating source.
The significant advantages of reflow soldering with infrared heating are the uniform heating of the same surface,which reduces the thermal stress on the part to be soldered,and the high thermal efficiency,which contributes to energy savings.However,the disadvantage is equally obvious: when infrared rays irradiate several objects at the same time,the heat absorbed by each object varies due to differences in surface colour, reflectivity and material,resulting in temperature differences between the objects. Some objects may overheat due to excessive heat absorption.
③ ‘IR + forced convection’ combination is a response to the μBGA and CSP cold soldering of the core technology means.Overseas industry for the QFP140P and PCB and 45mm BGA and PCB cold solder joint between the research found that only convection heating and the use of ‘IR + forced convection’ combination of heating system under two different conditions,the temperature uniformity of heating there are significant differences:
(a) The temperature difference between the QFP140P and the PCB reached 22°C under convection heating only;
(b) The use of ‘IR + forced convection’ composite heating system, QFP140P and PCB temperature difference between the PCB is reduced to only 7 ℃, for 45mm BGA, the temperature difference is further reduced to 3 ℃.
The basic principle of ‘IR + forced convection’ heating is: the use of infrared light as the main heat source to achieve efficient heat transfer, combined with the balanced heating characteristics of convection, in order to effectively reduce the temperature difference between the components and PCB. Convection heating has the advantage of heating large-capacity components, and can also play a cooling role in the overheating of smaller thermal capacity components.
3) The impact of the difference in the installation position on the incidence of cold soldering μBGA, CSP cold soldering phenomenon occurs, and its installation position on the PCB also has a great relationship.
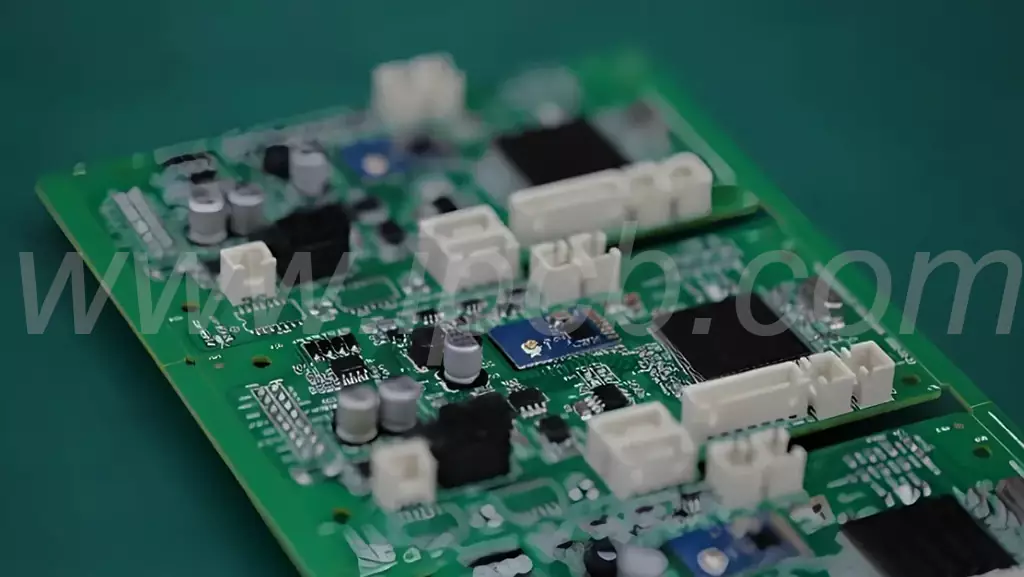
Similarities and Differences Between False and Cold Solder Joint
Similarities
Dummy soldering and cold solder joints have many commonalities in their phenomena, which often leads to difficulties in accurately distinguishing them in practice,resulting in misjudgments. Therefore, accurately identifying the similarities and differences between false soldering and cold soldering is crucial for quality control in the manufacturing process of electronic products.The similarity between false soldering and cold soldering is mainly reflected in the following aspects:
(1) The failure of solder joints caused by cold solder joint and false soldering both show the characteristics of interface failure, i.e., poor electrical contact or microcracks in solder joints all occur at the contact interface between the pad and the brazing material;
(2) Cold soldering and false soldering have similar definitions, both indicating the failure to form the desired intermetallic compound layer (referred to as IMC) at the solder interface;
(3) In engineering applications, cold solder joint and false soldering produce similar effects and hazards, and both suffer from poor electrical contact, unstable electrical performance, and insufficient connection strength. Especially for components such as BGAs and CSPs, such solder joint defects are insidious and may be exposed only after days, months or even longer.
Differences and Physical Characteristics Positioning
- Difference in Causal Mechanisms
False soldering originates from oxidation, sulphation or contamination of the surface of the metal to be soldered, which leads to degradation of soldering performance,while cold soldering is caused by insufficient supply of heat during the soldering process. - Difference in solution
Soldering problems are usually solved by improving the cleanliness and weldability of the welded metal surface and adjusting the chemical activity of the flux, which is relatively easy to implement.While the cold welding problem needs to solve the welding process in the heat to fully supply the problem, especially for BGA, CSP and other high-density components,which often involves the heating mode of the re-flow furnace,heat conversion and transfer efficiency and other complex factors, so the solution is much more difficult,the scope of the wider. - Difference in connection strength
In false soldering, due to the presence of oxide film between the brazing material and the surface of the base metal, the adhesion of the brazing material is significantly reduced after solidification, and the connection strength is weaker. In cold soldering, the IMC layer formed at the interface of the solder joint is thin and incomplete in minor cases, and penetrating cracks may appear in serious cases, resulting in almost no strength of the solder joint. - Differences in metallographic structure
The metallographic structure of virtual soldering is relatively fine; while the metallographic structure of cold soldering appears to be uneven. - Comparison of micro-optical visual images
(1) Appearance characteristics of good solder joints
CBGA solder joints in the reflow soldering, the solder ball does not melt,the solder paste after reflow fully fill and wet the pad and the solder ball between the formation of a good wetting angle, the surface is smooth and flat,the height of the non-collapse. pBGA ball solder joints surface bright and smooth, good wetting angle, the height of the collapse of the ball pin height of about 1 / 3 to 1 / 2.
(2) Appearance characteristics of the cold solder joints of false solder
The micro-optical visual image of a defective solder joint is characterised by the absence of a wetted fillet.
(3) Appearance characteristics of cold solder joints
The micro-optical visual image characteristics of a cold solder joint include an orange peel on the surface of the joint, insufficient reflow of solder paste, and insufficient collapse height (only the first stage of collapse occurs, and the second stage of collapse does not proceed due to insufficient heat).
Although the cold solder joint is a difficult pass in the manufacturing process of electronic products, on the basis of an in-depth understanding of the mechanism and influencing factors of cold welding, we continuously optimise the welding process and enhance the heat transfer efficiency to ensure that each welding point can achieve the ideal welding effect.