Conventional wave soldering is a mature and widely used mass welding technology, by inserting plug-in components into the PCB board, and then the whole through the solder wave to complete the welding, to achieve efficient mass production. This process is particularly suitable for soldering a large number of plug-in components, and the effect is particularly significant in the production of simple structure, the arrangement of regular circuit boards.
Selective soldering is an upgraded process based on wave soldering technology and is mainly used for soldering equipment with through-hole components and surface mount technology (SMT) assemblies. The use of this type of soldering has grown rapidly with the popularity of double-sided PCBs, which facilitate the manufacture of smaller, lighter electronic products.
Conventional wave soldering advantages:
High efficiency: able to one-time soldering of the entire PCB, suitable for large-scale manufacturing.
Cost-effective: less investment in equipment and materials, cost-effective.
Easy to operate: mature and stable process, easy to maintain and operate.
Disadvantages:
Limited soldering selectivity: unable to target only specific areas for soldering, which may affect components that have already been affixed, or require additional protective measures.
Insufficient flexibility: susceptible to soldering defects in complex or high-density circuit boards.
Environmental stress: heavy use of solder and flux volatilisation may have an impact on the environment and operator health.
Scope of application:
Conventional wave soldering is suitable for high-volume manufacturing, single-panel or plug-in component-intensive and simple layout PCBs, such as household appliance control boards and industrial equipment motherboards and other application scenarios.
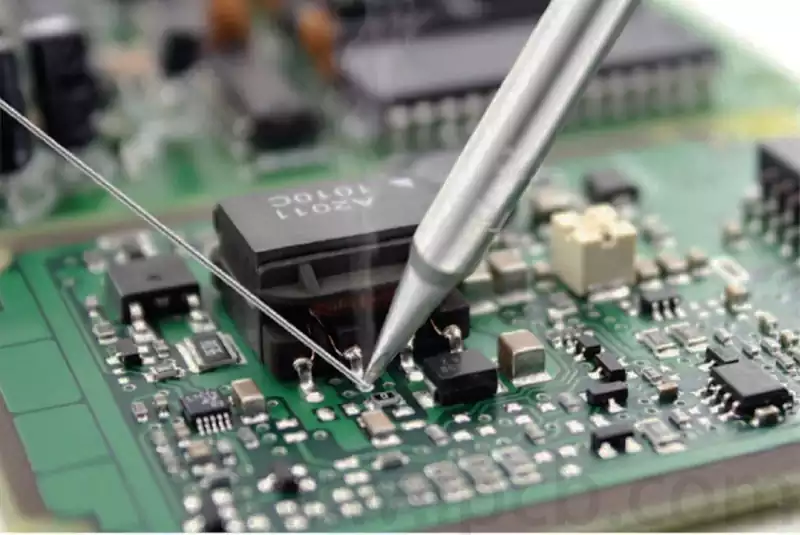
Selective soldering process is usually divided into three steps:
Firstly, flux is locally applied to the component parts to be soldered, then the board is preheated, and finally specific components are soldered using specialised soldering nozzles.
Advantages of selective soldering include:
Process stability and high repeatability;
Easy optimised adjustment of process parameters;
Improved solder joint quality and reliability;
Localised application of flux, eliminating the need for shielding to protect other components;
Reduced flux usage;
Individualised soldering parameters can be set for different components;
Avoiding the cost of expensive aperture wave soldering baffles;
Suitable for complex boards where conventional wave soldering processes cannot be used.
Difference between wave soldering and selective wave soldering:
Wave soldering is a process in which the entire surface of the circuit board is brought into contact with molten solder, and the natural rise of the surface tension of the solder is utilised to complete the soldering. For boards with large heat capacity and multi-layer structures, wave soldering is more difficult to meet the requirements of the tin effect. Selective wave soldering is different, it uses the dynamic tin wave sprayed by the soldering nozzle, the strength of this dynamic tin wave directly affects the through-hole vertical tin permeability. Especially in lead-free soldering, due to poor wettability, more need to have a strong dynamic tin wave. In addition, a strong flow of tin waves is effective in reducing oxide residues, thus improving solder quality.
The soldering efficiency of selective wave soldering is indeed lower than that of conventional wave soldering because it is mainly used for soldering high-precision PCB boards, which is difficult to be performed by ordinary wave soldering. For through-hole group soldering, which is not possible with conventional wave soldering, especially in specialised areas such as automotive electronics and aerospace, selective wave soldering provides precise control of the solder joints. Temperature, process and weld parameters can be finely tuned to individual weld joints through programming, ensuring a controlled and repeatable operation, making it suitable for applications where through-holes are becoming increasingly small and component-intensive. Although selective wave soldering has lower productivity (even with 24-hour continuous operation) and higher maintenance costs, the yield of the joint is largely dependent on the condition of the NOZZLE.
Conventional wave soldering and selective wave soldering each have their own unique advantages and application scenarios. Traditional wave soldering is still an indispensable and mature process in mass production due to its high efficiency, economy and easy operation; while selective wave soldering better meets the needs of modern complex, high-density and high-precision PCB soldering by virtue of its precise soldering control capability and flexible adjustment of process parameters.