A complex circuit board, as the name suggests, is a circuit board that is made from a combination of materials. It usually consists of several components such as insulating substrates, conductive layers, and insulating layers, each of which plays an integral role. The insulating substrate provides a stable support for the circuit, the conductive layer is responsible for transmitting current and signals, and the insulating layer ensures isolation between circuits and prevents short circuits from occurring.
The complex circuit board is brittle and hard, the fiber is strong and tough, the interlayer shear strength is low and anisotropic, the thermal conductivity is poor and the coefficients of thermal expansion of the fiber and the resin are very different, when the cutting temperature is high, it is easy to generate thermal stresses at the interface of the fiber and the substrate around the cutting zone; when the temperature is too high, the resin melts and sticks to the cutting edge, resulting in difficulties in machining and chip removal. Drilling composite material cutting force is very uneven, easy to produce delamination, burr and splitting and other defects, processing quality is difficult to ensure. This material is extremely abrasive to the processing tools, tool wear is quite serious, tool wear in turn will lead to greater cutting force and generate heat, if the heat can not be dissipated in time, it will lead to the melting of the low melting point component of the PCB material and composite materials between the layers and layers of the peeling. Therefore, PCB composite materials are difficult to process non-metallic composite materials, and its processing mechanism is completely different from that of metal materials.
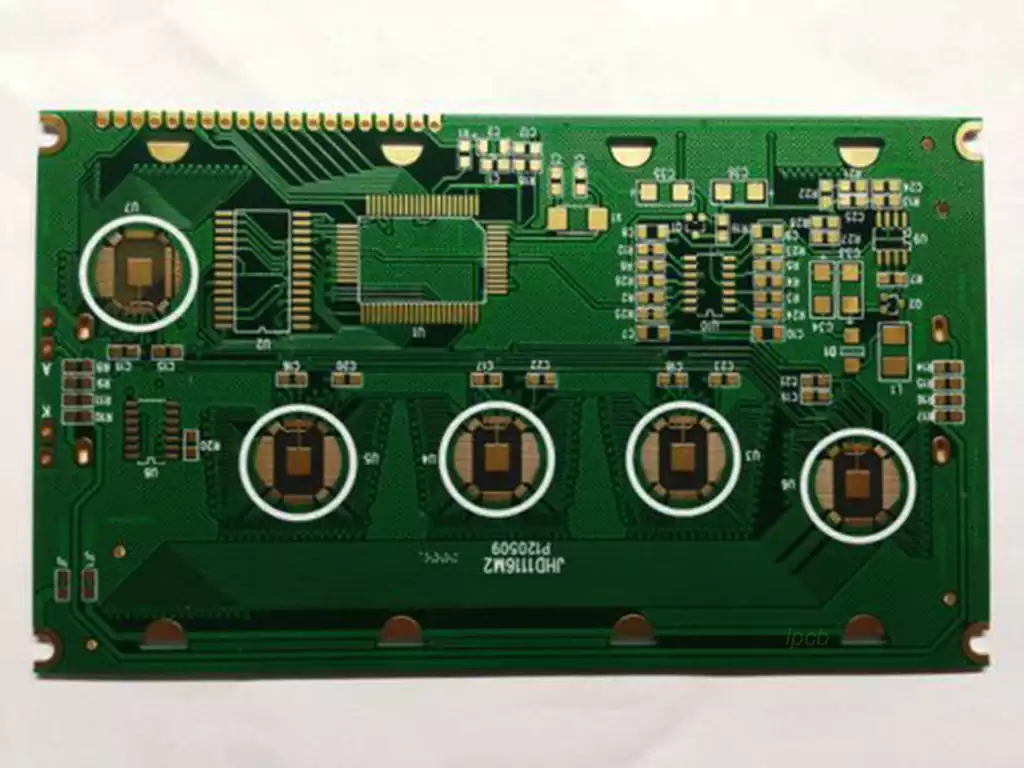
When mechanically drilling PCB materials, the processing efficiency is high, the hole positioning is accurate, and the quality of the hole is high. However, when drilling micro-small holes, due to the drill diameter is too small, it is very easy to break, and the drilling process may also appear material delamination, hole wall damage, burrs and stains and other defects.
Various problems in the mechanical drilling process are directly or indirectly related to the axial force and cutting torque, the main factors affecting the axial force and torque are the feed, cutting speed, the shape of the fiber bundle and the presence or absence of prefabricated holes also have an impact on the axial force and torque. The axial force and torque increase with the increase of feed and cutting speed. As the feed increases, the thickness of the cutting layer increases, while the cutting speed increases, the number of fibers cut per unit time increases, and the tool wear increases rapidly, so the axial force and torque increase.
Due to the different processing properties of composite matrix and reinforcing fibers, the effects of matrix resin and fibers on the axial force during mechanical drilling are different.Khashaba investigated the effects of the type of matrix and fibers on the axial force and torque, and found that the shape of the fiber bundles had a more pronounced effect on the axial force, while the type of matrix resin had a lesser effect on the axial force.
The importance of complex circuit board as the cornerstone of modern electronics cannot be overstated.