Coplanarity, or the degree of co-planarity of the pins, refers to the deviation of the ends of the pins of an SMT component relative to an ideal plane. Ideally, all pins should be completely coplanar so as to ensure good contact with the PCB pads during the placement process. Insufficient coplanarity may lead to poor soldering, false soldering, cold soldering and other defects, which in turn affects the performance and reliability of electronic products.
Factors affecting coplanarity
Component encapsulation process: the encapsulation process of the component has a direct impact on the co-planarity of its pins. In the encapsulation process, if the pins are fixed improperly or unevenly heated, it may lead to deformation of the pins, which in turn affects the coplanarity.
Material selection: the choice of the pin material will also affect its coplanarity.For example,certain materials are prone to deformation when subjected to heat, thus affecting the coplanarity of the pins.
Transportation and storage: If components are subjected to extrusion, collision and other external forces during transportation and storage, it may also lead to deformation of the pins, destroying their coplanarity.
The coplanarity of electronic components refers to the relative height difference between components on a plane, and this height difference directly affects the performance of the circuit. If the height difference between components is too large, the signal transmission of the circuit will be affected, resulting in unstable circuit operation. Therefore, the coplanarity of components needs to be checked during the circuit design and manufacturing process to ensure that the performance of the circuit meets the requirements.
Which components need to be checked for commonality?
- Higher package components
Some higher packages, such as BGA, QFN, etc., they are more difficult to tightly combined with the PCB substrate, placed unevenly will produce a height difference, so the need for coplanarity check. - Higher hardware components
Higher hardware components, such as connectors, sockets, mounting brackets, etc., in some of the thinner PCB there will be a significant height difference, affecting the components of the coplanarity, so need to check. - Components that require attention during assembly
During assembly, some components may cause bending of the PCB board,such as large electrolytic capacitors, connectors, DDP sockets and electronic transformers, etc. These components require special attention.They should be checked periodically during assembly to see if they affect the coplanarity of the board.
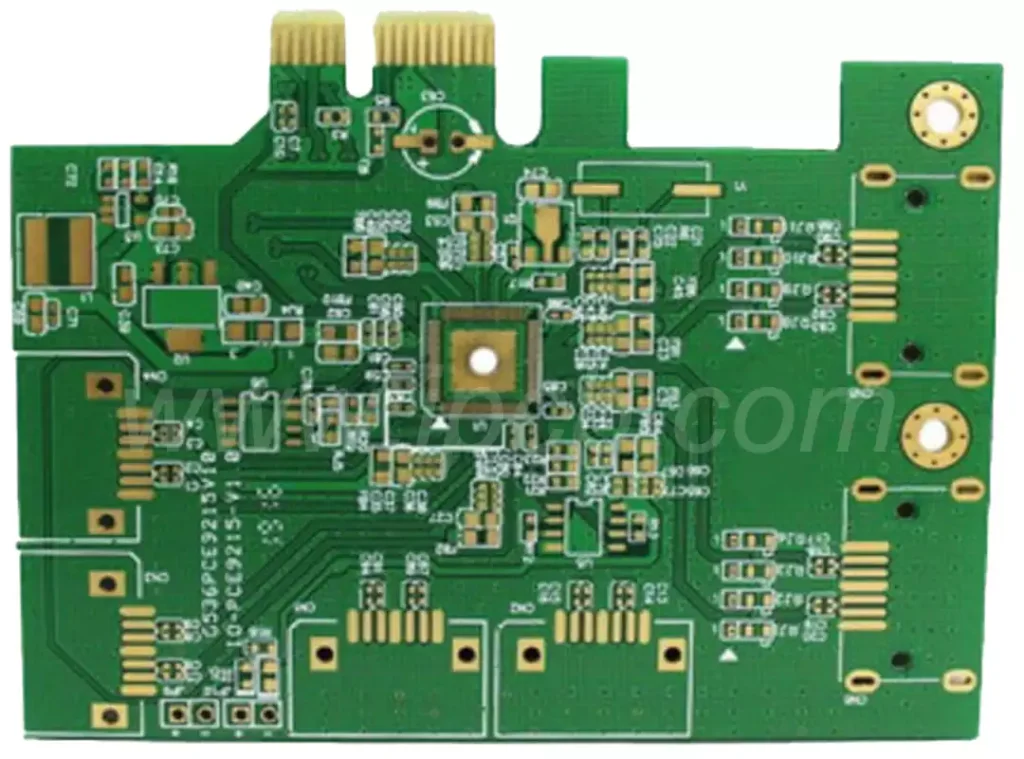
The Role of Component Pin Co-Planarity
Component pin coplanarity is the ability to indicate the parallelism between the device pins mounted to the pcb and the surface of the substrate, which is one of the key indicators affecting the quality of component soldering. When components in the welding process pins and PCB board surface is not parallel, after the completion of welding will lead to poor solder joint quality, which in turn affects the quality and reliability of the entire electronic product. Therefore, to ensure that the component pin coplanarity is essential.
Component pin coplanarity of the standard tolerance value is usually 0.1mm, this tolerance value is issued by the International Institute of Electrical Engineers (IEEE) standard. Of course, different electronic products have different requirements for pin coplanarity, and some high-end, high-demand products may have higher tolerance standards that need to be determined on a case-by-case basis.
In addition, in order to ensure that the components pin coplanarity, but also in the PCB design and component selection and production process for a series of strict control and testing, such as reasonable arrangements for pin layout and welding process parameters and other measures. Through these control and detection means, can effectively ensure that the components pin coplanarity of the standard tolerance value to achieve and maintain.
In surface mount technology (SMT), solder joints are an important medium for connecting electronic components to printed circuit boards (PCBs), and soldering failure is one of the frequently encountered failures of electronic components. Therefore, it is critical to ensure that electronic components are reliably soldered.Among them,the coplanarity of component pins is one of the important factors affecting soldering reliability.
When all the pin endpoints of a device are in the same plane, it is called component pin coplanarity. However, during the component manufacturing process, the effects of factors such as forming stresses on the extension pins and external forces suffered during preservation and transportation usually result in the soldering position of the extension pins not being coplanar. This difference in height needs to be compensated for by solder fill to form a reliable solder joint.
If the soldered parts of the device are not in a plane, soldering faults such as pin deficiencies and missing solder can occur. In order to ensure the reliability of the solder joint, it is necessary to test the planarity of the component pins. Currently there are two main test methods: fixed measurement method and regression surface test method.
Fixed-plane measurement method:
Fixed surface refers to the plane formed by the three solder joints that are the farthest from the bottom of the device package itself in the vertical distance. The projection of the component’s center of gravity in the vertical direction must lie within the triangle formed by these three solder joints. Fixed plane measurements are commonly used to evaluate the coplanarity of component solder terminals. For BGA components, the three highest solder balls hold up the component itself and form a fixed plane (the projection of the center of gravity of the BGA body in the vertical direction lies within the triangle formed by these three solder balls). The distance of the other solder balls from this face is the coplanar deviation value.
Regression plane test method:
The regression plane refers to a plane that is parallel to the optimal plane formed by the solder vertex that is furthest vertically from the bottom of the component body and the vertices of all the solder joints. This optimal plane is determined using the least square method.
How to avoid device pins are not co-planar?
- Avoid squeezing, dropping and impacting during transportation and handling of extended pin devices.
- The reuse of the production line material should be 100% inspected and put into use again after the foot is straightened if necessary.
- BGA device placement, equipment to open the global identification function, the size of the ball, the lack of ball bad automatic interception and detection.
- The use of a smaller pitch of ultra-micro solder paste can be improved to a certain extent, the device pins are not co-planar situation.As the ultra-micro solder paste can improve the welding accuracy and quality of the solder joints, thereby reducing the gap between the device pins and PCB pads,increase its connection strength, so to a certain extent can offset the impact of the device pins are not coplanar, improve the reliability and accuracy of the package.
Ensure that the component pin coplanarity is to enhance the quality of SMT welding and the reliability of electronic products is a key link. Through strict process control and inspection methods, we can effectively reduce the soldering defects caused by pin coplanarity, and escort the high quality production of electronic products.