Copper oxydation pcb no solder mask is a special type of printed circuit board that protects the copper conductors by forming a stable copper oxide film instead of a solder mask. This oxide layer not only enhances the corrosion resistance of the pads, but also improves solder wetting, ensuring that the solder material adheres better to the pads and effectively reduces the rate of soldering defects.
Characteristics of the copper oxydation pcb no solder mask
One of the most important features of copper oxydation pcb no solder mask is their excellent solderability.Due to the formation of a stable copper oxide film on the surface, the presence of this oxide layer significantly improves solder wettability during soldering. Studies have shown that when soldering with copper oxydation pcb no solder mask, the solder defect rate can be reduced by more than 30 per cent compared to conventional circuit boards. This means that rework and scrap due to poor soldering can be reduced during the production process, thus increasing productivity.
Good corrosion resistance. The copper oxide layer effectively prevents oxidation of copper conductors, especially in humid or corrosive gas-containing environments. This enables copper oxydation no solder mask pcb to maintain good electrical connectivity and stability in harsh environments. In automotive electronics and industrial automation, for example, this property significantly improves the reliability and service life of products.
Thermal stability is another important characteristic of copper oxydation pcb no solder mask.At high temperatures, the copper oxide layer maintains its structural integrity, ensuring that the board’s performance is not compromised. Typically, these boards perform well over a range of service temperatures (e.g., -40°C to +125°C) and are suitable for a wide variety of industrial and consumer electronics. For example, boards used in aerospace and high-end communications equipment often require high-temperature stability, which is met by solderless copper oxide boards.
Electrical performance is excellent, with good conductivity and low resistance. This is particularly important for high frequency applications. Studies have shown that the board reduces signal attenuation by 20-30 per cent when compared to standard boards for high-frequency signal transmission, effectively improving signal integrity and transmission speed. This advantage makes copper oxydation pcb no solder mask the first choice for high-frequency requirements such as communication equipment and data centres.
Copper oxydation pcb no solder mask is compatible with a wide range of electronic component packages and are suitable for a variety of processes such as surface mount technology (SMT) and through-hole insertion. The surface finish allows the boards to perform well with a wide range of soldering methods, and this flexibility makes it easier for manufacturers to select the appropriate soldering technique during production, thereby increasing productivity. For example, in the production of smartphones and tablets, the compatibility of solderless copper oxide circuit boards ensures high-density integration of components within the device.
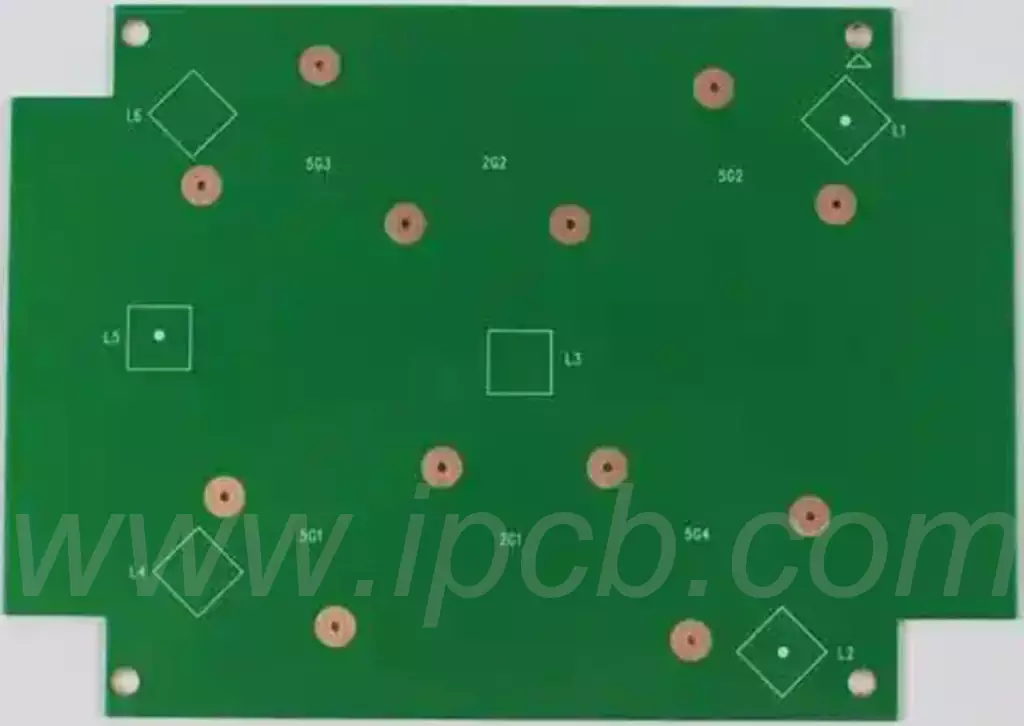
The production process of copper oxydation pcb no solder mask:
1.Material Preparation
The first step in the manufacture of copper oxydation pcb no solder mask is the selection of a suitable base material. Usually, high-performance FR-4 copper clad laminate is used, which is widely used in electronic production for its good electrical insulation and thermal stability. According to statistics, about 70% of consumer electronics products use FR-4 as a substrate. To ensure the long-term stability of the circuit board, manufacturers need to strictly control the thickness of the substrate and the thickness of the copper layer. In general, the thickness of the copper layer is usually 1 ounce (about 35 microns) to ensure the effective transmission of current.
2.Printed Circuit Graphics
Photolithography is used to form circuit patterns on copper-clad laminates, which is a complex and delicate process. First, the photosensitive adhesive needs to be uniformly applied to the surface of the copper-clad laminate to obtain a uniform thickness, usually 0.5-1.0 microns. Then, the area where the circuit pattern needs to be formed is irradiated by a special UV light, which causes the photosensitive adhesive to react chemically to form a laminate with a wire pattern. Not only does this process require a precise pattern design, but the exposure time and intensity of the light source must be right to ensure that the details of the design can be accurately transmitted. Then, moving on to the development step, the unexposed photosensitive adhesive is removed, leaving a circuit pattern that typically achieves a line width of 0.1 mm, which is sufficient to meet the needs of modern electronic devices.
3.Etching
Etching is an important step in removing unwanted copper layers to reveal the circuit pattern. In this process, the etching solution used is usually ferric chloride solution, its concentration and temperature will directly affect the etching efficiency and effectiveness. Manufacturers need to mix etching solutions of the right concentration (usually around 30%) and temperature (around 50°C) to ensure etching speed and quality. Under standard conditions, the etching time is usually between 5-15 minutes, after the completion of the circuit board wires and connections will be clearly visible, showing a bright copper colour, to ensure a good basis for subsequent soldering.
4.Cleaning and drying
After etching, the circuit board needs to be thoroughly cleaned to remove residual photosensitive adhesive and etchant. General use of ultrasonic cleaning machine and deionised water, cleaning time of about 3-5 minutes, to ensure that the surface of the circuit board clean and free of impurities. After cleaning, the circuit board needs to be dried in a special drying equipment, maintaining the temperature at about 70 ℃, to ensure that its surface is completely dry for subsequent processing procedures.
5.Oxidation
Oxidation is a key step in the manufacture of copper oxydation no solder mask pcb,the goal is to form a stable layer of copper oxide film. This process is usually carried out in a temperature-controlled environment of 150-200 ℃, the oxidation environment needs to maintain a certain degree of humidity to ensure the uniformity of the oxide layer and adhesion. Through this process, the thickness of the copper oxide is approximately 0.5-1.0 microns, which can effectively improve the strength of the solder joint and reduce the incidence of soldering defects. In addition, studies have shown that the freshness and durability of solder joints when soldered using copper oxydation pcb no solder mask is improved by approximately 30% compared to conventional circuit boards.
6.Surface Treatment
After the oxidation process is completed,a surface treatment,such as the addition of flux or covering with other soldering pre-treatment substances, is required to further enhance the solderability of the circuit board.This step generally uses chemical spraying or dip-coating techniques to form a uniform layer of flux coating, the thickness of which is controlled within a few microns.This reduces the chance of oxidation entering the joint during soldering and ensures good adhesion of the solder.
7.Final Inspection and Testing
At the final stage of production, the completed board is subjected to a thorough inspection. This includes a visual inspection and electrical performance measurements to ensure that all circuits are connected properly and to avoid the occurrence of short or open circuits. Fabrication companies usually use Automated Optical Inspection (AOI) systems to check whether each circuit board meets the design criteria, while electrical testing includes the requirement for each signal line to have a resistance of less than 1 ohm, which effectively ensures the stable operation of the circuits.
Comparison of the cost of copper oxydation pcb no solder mask and normal circuit boards
Material Costs
Copper oxydation pcb no solder mask is usually made of copper oxide,which is a relatively high cost material. This process adds to the manufacturing cost as it requires an oxidising process compared to conventional copper-clad boards. As a result, the initial material cost of solderless copper oxide circuit boards is typically higher than the material cost of regular conventional circuit boards. This cost increase is mainly due to the manufacturing process of the oxide layer and the special chemical treatment required.
Production Processes
In terms of production processes,copper oxydation pcb no solder mask has a complex manufacturing process that involves multiple steps such as coating and oxidation. These additional process steps increase the productivity requirements and bring additional equipment and maintenance costs to the production line. As a result, from a simple production process perspective, solderless copper oxide circuit boards are more expensive to produce than conventional circuit boards.
Economics of Overall Performance
Although the initial cost of copper oxydation pcb no solder mask is higher than that of conventional circuit boards,their superiority in terms of overall performance shows clear economic benefits.This board improves solder reliability, reduces soldering defects, and lowers rework and maintenance costs due to poor soldering. Additionally, their stability in high temperature and high pressure environments extends product life and further reduces overall costs over the long term.
Copper oxydation pcb no solder mask offers significant advantages in high frequency and demanding applications. Despite their relatively high material and production costs, they offer significant economic benefits in the long term through improved productivity and product reliability. As a result, copper oxydation no solder mask pcb has a promising future in specific areas of application.