Crazing pcb is the phenomenon of cracks or breaks in a circuit board, which can lead to impaired functionality or even complete failure of the board.
The causes of crazing pcb analysis:
- Material factors
If the PCB circuit board used in the production process of the substrate material quality is poor, or the substrate and welding materials do not match the coefficient of thermal expansion, then in the process of thermal expansion and contraction will produce stress, which in turn triggers the crazing pcb phenomenon. - Improper welding process
In the process of welding PCB board, if the welding temperature is too high or welding time is too long, it will lead to thermal expansion of the substrate material, which may cause crazing pcb. - Mechanical external force
In the manufacturing and use of electronic products, mechanical vibration or the role of external forces may make the PCB line deformation or fracture, resulting in crazing pcb. - Environmental factors interfere
Substantial changes in ambient temperature will make the PCB on the line and material thermal expansion and contraction, resulting in stress and may lead to PCB cracking. In addition, high humidity environment may make the line on the PCB moisture and corrosion, may also trigger the crazing pcb.
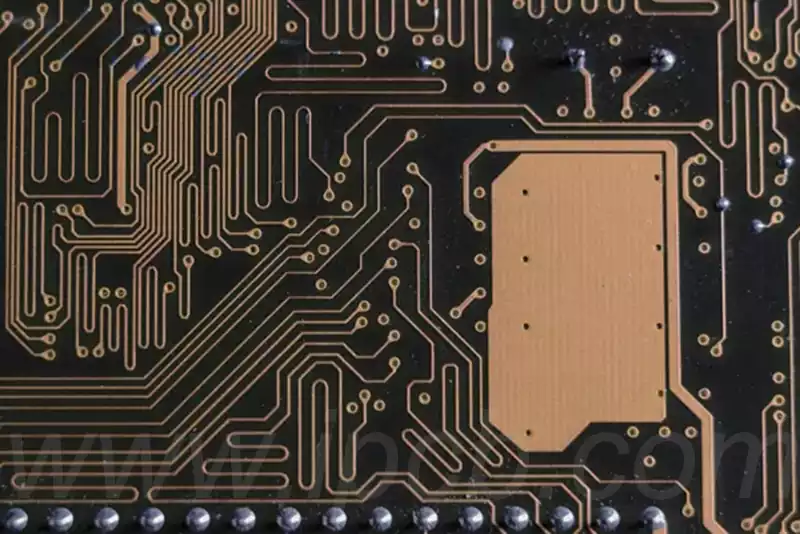
In order to prevent crazing pcb, you can take the following measures:
- Selected boards and appropriate thickness: According to the actual application requirements and mechanical strength standards, carefully select the type of board and ensure that its thickness is moderate. Usually, thicker boards can show better strength and bending resistance.
- Optimise the layout design: In the layout planning of the PCB, it is necessary to carefully avoid excessive concentration of components in a certain area resulting in weight or mechanical stress concentration. Through the reasonable distribution of components, to achieve a balanced layout, and thus weaken the adverse effects of mechanical stress.
- Regulate the thermal expansion of the board: In view of the PCB board in the temperature change will occur thermal expansion, and different materials have different coefficients of thermal expansion, so in the layout design need to take this into account, as far as possible to narrow the gap between the thermal expansion of different materials, in order to reduce the stress borne by the board.
- Reinforcement of the connection: through the use of pins. Socket. Locking screws and other fixed connection methods, strengthen the design of the connection point, so as to enhance the solidity of the connection and tensile performance.
- Strictly control the manufacturing process: In the PCB manufacturing process, be sure to implement strict control of temperature and humidity conditions, to avoid excessive soldering temperature or hot and humid environment. At the same time, should follow the manufacturer’s guidelines and best practices to ensure that the manufacturing process in line with process standards.
- Balanced pressure distribution: In the installation and use of PCB boards, need to pay attention to its pressure distribution, avoid excessive bending. Squeeze or twist to reduce the risk of stress concentration.
- Implementation of testing and quality control: In the PCB manufacturing stage, it is essential to carry out the necessary tests and quality checks to ensure the quality and reliability of the PCB. With the help of X-ray inspection. AOI (Automatic Optical Inspection) and mechanical strength testing and other quality control means, timely detection and resolution of potential cracks.
Preventing crazing pcb requires a multifaceted approach that includes selecting materials, optimising layout, controlling thermal expansion, reinforcing connections, tightening manufacturing processes, balancing pressure distribution, and implementing testing and quality control. Through these measures, we can significantly improve the reliability and stability of PCB boards to ensure the normal operation of electronic products.