In modern electronic products, DCC adapter PCB plays a vital role. Whether in consumer electronics, industrial equipment or electric vehicles, it undertakes the tasks of power conversion, signal conditioning and circuit protection. This article will explore in depth the design points, manufacturing process and role of DCC adapter PCB board in different application scenarios, and analyze its future development trend.
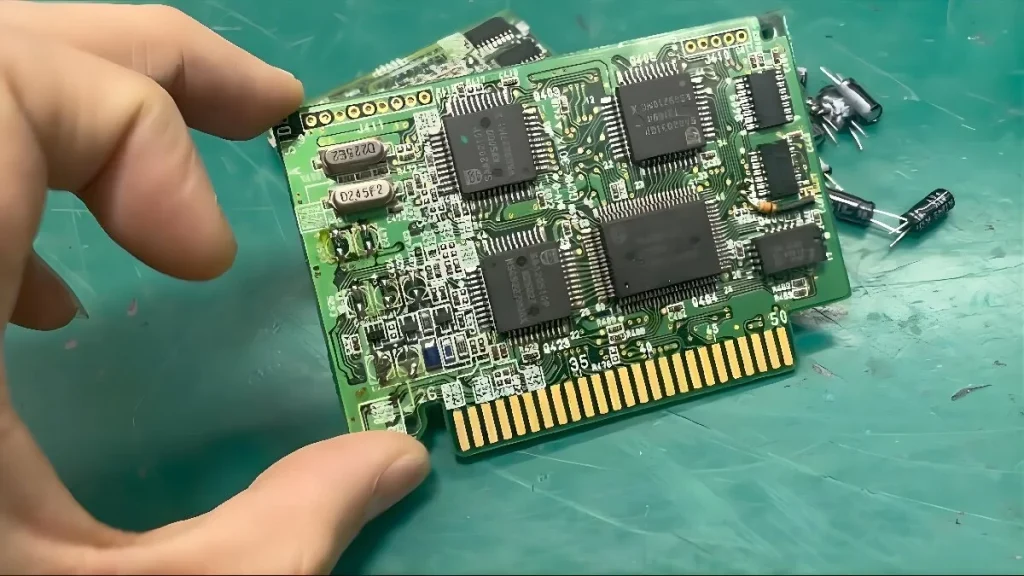
Basic concept of DCC adapter PCB
DCC adapter PCB is a circuit board used for power adaptation. Its core function is to convert input power into a stable output voltage required by the device. This PCB is usually used in power management systems to ensure that electronic devices can operate safely and stably. It is mainly composed of multiple electronic components, including rectifier circuits, filter circuits, voltage regulator modules and protection circuits.
In the design process of DCC adapter PCB, engineers need to consider factors such as voltage range, power requirements, heat dissipation management and electromagnetic compatibility. These factors determine the reliability and performance of the circuit board and ensure that it can operate stably in different environments.
Design points of DCC adapter PCB
- Power management and voltage regulation design
In the design of DCC adapter PCB, the voltage regulator module is the most critical part. The function of the voltage regulator circuit is to adjust the input voltage to a stable output voltage to meet the needs of the target device. Generally speaking, the voltage regulator circuit can adopt two methods: linear voltage regulation or switching voltage regulation. Among them, the linear voltage regulation method has the characteristics of low noise and easy design, but the efficiency is low and it is easy to generate heat; while the switching voltage regulation method is more efficient, but requires additional filtering circuits to reduce high-frequency interference.
In addition, in some special applications, such as industrial equipment or medical equipment, the requirements for power supply stability are higher. Therefore, the power management system of the DCC adapter PCB board may include a multi-stage voltage regulator circuit to further reduce voltage fluctuations and improve the reliability of power supply.
- Heat dissipation management
DCC adapter PCB board will generate a certain amount of heat during operation, especially in high power conversion applications, heat dissipation design is particularly important. Common heat dissipation methods include:
Increase heat dissipation holes to enhance air convection
Use large area copper foil to improve thermal conductivity
Use heat sink or fan to assist heat dissipation
Select PCB substrate with high thermal conductivity, such as metal substrate
Reasonable heat dissipation design can effectively reduce the operating temperature of the circuit board and improve its service life and stability. Especially in high-power electronic devices or outdoor equipment, good heat dissipation management can effectively reduce system failures caused by overheating.
- Electromagnetic compatibility (EMC)
When the DCC adapter PCB board works at high frequency, it may generate electromagnetic interference and affect the normal operation of surrounding equipment. Therefore, certain electromagnetic compatibility measures need to be taken during design, such as:
Use shielding design to reduce electromagnetic radiation
Perform reasonable routing layout to avoid cross interference of signal lines
Use filtering circuit to reduce high-frequency noise
Good EMC design can not only ensure the normal operation of the DCC adapter PCB board, but also improve the reliability of the entire system and reduce the interference of the external environment on the circuit.
Manufacturing process of DCC adapter PCB board
The manufacturing process of DCC adapter PCB board includes multiple key steps, from design, material selection to final assembly test, each link affects the quality of the product.
- Material selection
The material of the PCB board usually selects FR-4 glass fiber board, metal substrate or high-frequency material. For high-power DCC adapter PCB board, thick copper plate or metal substrate is usually selected to improve thermal conductivity. - Circuit board production
The production of circuit boards mainly includes processes such as exposure, etching, and electroplating. This stage requires precise control to ensure the integrity and reliability of the circuit. - Electronic component welding
The components on the DCC adapter PCB board can be soldered by wave soldering, reflow soldering, or manual soldering. In order to ensure the quality of soldering, the soldering temperature and time need to be strictly controlled to avoid component damage or cold soldering problems. - Testing and quality control
After manufacturing, the DCC adapter PCB board needs to undergo rigorous functional testing, reliability testing, and environmental testing to ensure that it can operate stably in actual applications.
Application fields of DCC adapter PCB boards
DCC adapter PCB boards are widely used in many fields, each of which has different requirements for its performance and reliability.
- Consumer electronics field
In consumer electronic products such as smartphones, laptops, and tablet devices, DCC adapter PCB boards are used for power management to ensure that the device can operate stably under different charging environments. This type of PCB board usually requires miniaturization, high efficiency, and low cost. - Industrial automation
Industrial equipment usually requires a stable power supply to ensure the normal operation of the production line or control system. DCC adapter PCB boards are widely used in industrial automation equipment, such as robot control systems, motor drive modules, etc. Such applications usually require PCB boards to have high durability and good electromagnetic compatibility. - Electric vehicles
With the development of new energy vehicles, DCC adapter PCB boards have been widely used in electric vehicles, electric bicycles and other vehicles. Such PCB boards need to have the characteristics of high voltage resistance and high reliability, and be able to work for a long time in harsh environments. - Medical equipment
In medical equipment, DCC adapter PCB boards are used to provide stable power supply to ensure the accuracy and safety of the equipment. For example, ECG monitors, ultrasonic equipment, etc. require a high-stability power management system.
Reliability test of DCC adapter PCB boards
The stability of DCC adapter PCB boards directly affects the service life and safety of electronic equipment. Therefore, after manufacturing, they must undergo a series of rigorous reliability tests to ensure that they meet industry standards and customer needs.
- High and low temperature cycle test
DCC adapter PCB boards may work under extreme temperature conditions, such as outdoor equipment or industrial automation systems. Therefore, before leaving the factory, it is usually necessary to perform high and low temperature cycle tests, that is, repeatedly cycle between high temperature (such as 85°C) and low temperature (such as -40°C) to verify whether the circuit board can maintain stable operation under temperature changes. - Vibration and shock test
Especially in the automotive, aerospace and industrial fields, DCC adapter PCB boards need to withstand long-term vibration and unexpected shocks. For example, the adapter circuit board in the car needs to undergo a bump test that simulates the driving of the vehicle to ensure that the solder joints will not loosen due to vibration. - Insulation withstand voltage test
In order to avoid electric shock or short circuit accidents, the insulation layer of the DCC adapter PCB board needs to be subjected to withstand voltage test. The test method is to apply high voltage (such as more than 1000V) between the input and output ends of the PCB board to check whether there is leakage to ensure that it can still work normally under high voltage environment. - Humidity and moisture test
PCB boards may be used in humid environments, such as medical equipment or outdoor monitoring systems. Therefore, manufacturers usually conduct humidity tests and place the DCC adapter PCB board in a high humidity environment (such as 95%RH) to test its moisture resistance. In order to improve the moisture resistance, the conformal coating technology can be used to enhance the durability of the PCB board. - Aging test
Aging test mainly simulates the performance changes of the DCC adapter PCB board after long-term use. Usually, manufacturers will let the PCB board run continuously for hundreds of hours under rated load conditions in a laboratory environment to observe whether it will experience performance degradation or abnormality.
Manufacturing optimization of DCC adapter PCB board
To manufacture a high-performance DCC adapter PCB board, it is necessary to comprehensively consider multiple aspects such as material selection, processing accuracy, and assembly process. In order to improve product quality, many manufacturers continue to optimize the process during the production process, mainly starting from the following aspects:
- Improve the durability of PCB materials
High-quality DCC adapter PCB boards usually use FR-4 fiberglass or metal substrates. Compared with traditional materials, FR-4 boards have better high temperature resistance, while metal substrates (such as aluminum or copper) can effectively improve thermal conductivity and are suitable for high-power adapters. - Use more advanced soldering technology
Traditional wave soldering and reflow soldering technologies have been widely used in the production of DCC adapter PCB boards, but in order to improve the quality of soldering, some manufacturers have begun to use selective soldering technology. This technology can more accurately control the temperature of solder joints and reduce the risk of cold solder joints and short circuits. - Enhance automated detection capabilities
During the PCB production process, any tiny defects may affect the stability of the final product. Therefore, manufacturers usually use Automatic Optical Inspection (AOI) systems to scan the PCB surface with a high-definition camera to identify possible soldering defects, short circuits or open circuits. In addition, X-ray inspection is also commonly used to detect whether there are hidden defects in the internal solder joints. - Use environmentally friendly manufacturing processes
With the tightening of global environmental regulations, the PCB industry is gradually transitioning to lead-free production. Many DCC adapter PCB board manufacturers have adopted lead-free soldering and environmentally friendly solvent cleaning processes to reduce the impact on the environment while complying with RoHS (Restriction of Hazardous Substances Directive) standards.
Common problems and solutions for DCC adapter PCB boards
Even in a strict manufacturing process, DCC adapter PCB boards may still have some common problems. Here are some common faults and their corresponding solutions:
- Overheating
Problem causes: PCB board design is unreasonable, heat dissipation system is insufficient or power conversion efficiency is low.
Solution:
Use large area copper foil to improve thermal conductivity.
Design reasonable heat dissipation channels, such as adding heat dissipation holes or using heat sinks.
Select high-efficiency switching power supply solutions to improve energy conversion efficiency.
- Excessive electromagnetic interference (EMI)
Problem causes: unreasonable circuit design, irregular signal routing or insufficient filtering system.
Solution:
When laying out the PCB, minimize cross-interference of high-speed signal lines.
Use appropriate filter capacitors and magnetic beads to reduce high-frequency noise.
Use shielding covers to isolate key circuit areas and reduce electromagnetic radiation.
- Unstable output voltage of the adapter
Problem causes: improper voltage stabilization circuit design, component aging or PCB moisture.
Solution:
Use high-precision voltage stabilization chips, such as LM series or TPS series.
Check capacitors for aging regularly and replace damaged components.
Coat the PCB surface with conformal coating to enhance moisture resistance.
Future development trend of DCC adapter PCB board
With the continuous progress of the electronics industry, the technology of DCC adapter PCB board is also evolving. The future development trends mainly include the following points:
- Higher energy efficiency standards
As the world pays more attention to energy conservation and environmental protection, future DCC adapter PCB boards will adopt more efficient power management chips to reduce energy consumption and improve conversion efficiency to meet more stringent international energy efficiency standards (such as Energy Star). - More compact design
The trend of thinner and lighter consumer electronics products has prompted DCC adapter PCB boards to continue to develop in the direction of miniaturization and high-density integration. For example, by using embedded component technology, the PCB size can be further reduced and the space utilization can be improved. - More intelligent control function
Future DCC adapter PCB boards may integrate intelligent monitoring systems that can automatically detect parameters such as current, voltage, temperature, etc., and connect to the cloud through the Internet of Things (IoT) to achieve remote monitoring and control. - More environmentally friendly manufacturing technology
As environmental regulations tighten, future PCB manufacturing will develop in the direction of environmental protection such as degradable materials and water-based cleaning processes to reduce environmental pollution during the production process.
Conclusion
As the core component of modern electronic devices, DCC adapter PCB boards involve complex design, manufacturing and testing processes. With the advancement of technology, its application scope will be further expanded, and in the future it will develop in the direction of high efficiency, miniaturization, intelligence and environmental protection. By continuously optimizing the design and manufacturing process, DCC adapter PCB boards will play an increasingly important role in the electronics industry.