Design for Manufacturing (DFM) technology is one of the important research contents of full life cycle design, and it is also a method of parallel design between product design and subsequent manufacturing. Early consideration of manufacturing related constraints during the design phase, comprehensive evaluation, and timely improvement of product design can result in a design solution with better overall goals, and strive for a successful product design and manufacturing process, in order to reduce costs, improve quality, and shorten the product development cycle.
DFM is the process of identifying the manufacturable and non manufacturable components at the beginning of product design, in order to increase the manufacturability of the product
Today’s DFM is the core technology of concurrent engineering, as design and manufacturing are the two most important stages in the product lifecycle. Concurrent engineering involves considering factors such as product manufacturability and assemblability from the beginning of design. So DFM is also the most important support tool in parallel engineering. Its key is the process analysis of design information, evaluation of manufacturing rationality, and suggestions for improving design.
DFM combines CAX, PDM, DFX, and other technologies to form the Design for Life Cycle (DFLC) technology.
DFX stands for Design for X. Among them, X can represent the product lifecycle or a certain link in it, such as assembly (M-manufacturing, T-testing), processing, use, maintenance, recycling, scrapping, etc. It can also represent product competitiveness or factors that determine product competitiveness, such as quality, cost (C), time, etc.
include:
DFP:Design for Procurement
DFM:Design for Manufacture
DFT:Design for Test
DFD:Design for Diagnosibility
DFS: Design for Assembly
DFE:Design for Environment
DFF:Design for Fabrication of the PCB
DFS:Design for Serviceability
DFR:Design for Reliability
DFC:Design for Cost
DFM process
1. Seeking and establishing DFM series specification documents for iPCB
DFM documents should be reasonably formulated based on the production design characteristics, process level, equipment hardware capabilities, product features, etc. of our company. In this way, when designing, the selection of assembly technology should take into account the current and future production capacity of the factory. Create unique ideas from the perspective of industrial design creativity, and design reasonable and practical products based on ergonomic principles. These documents can be simple clauses or a complex and comprehensive design manual. In addition, the documents must be maintained in a timely manner according to the company’s production development, so that they can more accurately meet current design and production needs.
2. Establish a DFM checklist based on the company’s DFM specification document
While planning product design, establish a DFM checklist based on the company’s DFM specification documents. Checklists are tools that facilitate a systematic and comprehensive analysis of product design, including inspection items, handling of key processes, etc. In terms of content, it mainly includes the following information:
a. Product information and data (such as circuit schematics, PCB diagrams, assembly drawings, CAD structural files, etc.)
b. Select the general processing flow for production and manufacturing: AI, SMT, wave soldering, hand soldering, etc.
c. PCB size and layout.
d. Selection of components and design of solder pads and through holes.
e. Design of applicable process edges, positioning holes, and reference points for production.
f. Implement various requirements for mechanical assembly.
3. Prepare DFM report
The DFM report reflects the issues identified throughout the entire design process. This is similar to the audit report in ISO9001, which mainly issues non conformities in the design based on DFM specification documents and checklists. The content must be intuitive and clear, with reasons for non-compliance listed, and even requests for correction results provided. Its report is real-time and runs through the entire design process.
4. DFM testing
What impact will the results of DFM design have on electronic manufacturing and what role will it play. This needs to be confirmed through DFM testing. DFM testing is conducted by design and testing personnel using a production process similar to the company’s production model to establish design samples, which may sometimes require the assistance of production personnel. Testing must be conducted quickly and accurately, and a test report must be produced to enable designers to immediately correct any issues detected and accelerate the design cycle.
5. DFM analysis and evaluation
This process is equivalent to a summary review. On the one hand, the reliability of DFM in product design can be evaluated, and on the other hand, non DFM designed manufacturing can be compared with DFM designed manufacturing through simulation. From the aspects of production quality, efficiency, cost, etc., the cost savings of DFM can be obtained, which serves as a reference for formulating annual production goals and budget, and can also enhance the determination of leaders to implement DFM.
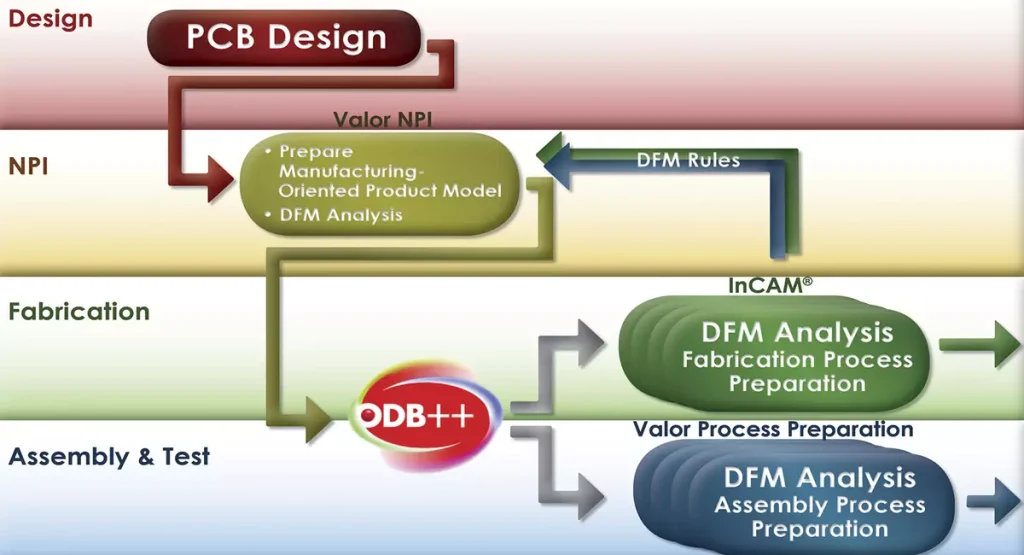
The significance of manufacturability design
1. Reduce costs and enhance product competitiveness.
Low cost and high output are the eternal pursuit goals of all companies. By implementing DFM standards, company resources can be effectively utilized to manufacture products at low cost, high quality, and high efficiency. If the product design does not conform to the company’s production characteristics and has poor manufacturability, it will require more manpower, material resources, and financial resources to achieve the goal. At the same time, they also have to pay a heavy price of delayed delivery or even losing the market.
2. Conducive to the standardization, automation, and improvement of production efficiency in the production process.
DFM organically links the design department and production department to achieve the purpose of information exchange, enabling coordination between design development and production preparation. Unified standards, easy to achieve automation, and improve production efficiency. At the same time, standardization of production testing equipment can also be achieved, reducing the repeated investment in production testing equipment.
3. Beneficial for technology transfer, simplifying product transfer processes, and strengthening collaboration and communication between companies.
Nowadays, many enterprises are limited by production scale, and a large amount of work needs to be outsourced. By implementing DFM, manufacturing technology can be smoothly transferred between processing units and processing units, and production can be quickly organized. The universality of manufacturability design can enable global production of enterprise products.
4. The foundation for new product development and testing.
Without proper DFM specifications to control product design, assembly issues of one kind or another are only discovered in the later stages of product development, or even in the mass production stage. At this point, attempting to correct them through design changes will undoubtedly increase development costs and prolong product production cycles. So in addition to prioritizing functionality in new product development, DFM is also very important.
5. Suitable for the increasingly complex challenges posed by new technologies in electronic assembly processes.
Nowadays, the development of new electronic assembly technology is becoming increasingly complex. In order to seize the market and reduce costs, companies must use the latest and fastest assembly technology and standardize it through DFM in order to keep up with its development pace.
Design for Manufacturing (DFM) mainly studies the physical characteristics of the product itself and the interrelationships between various parts of the manufacturing system, and applies it to product design in order to integrate the entire manufacturing system for overall optimization, make it more standardized, reduce costs, shorten production time, improve product manufacturability and work efficiency. The core of DFM is to participate in the entire design process from the initial planning of the product to its production, without affecting its functionality, to standardize and simplify it, making the design conducive to production and use. Reduce the manufacturing cost of the entire product, especially in terms of components and processing technology. Reduce the process flow, choose high pass rate processes, standard components, and reduce the complexity and cost of molds and tools.