In the construction of electronic devices, circuit boards are indispensable basic components, which are responsible for connecting electronic components and realising signal transmission and processing. Among the many types of circuit boards, radio frequency circuit board (RF PCBs) and general PCBs display their own characteristics due to their different design purposes and application scenarios. RF PCB focuses on the transmission and processing of high-frequency signals, and has more stringent requirements for materials, design and manufacturing process; while ordinary PCB focuses more on meeting the connection needs of daily electronic equipment, its design is relatively simple, and the cost is more economical. Next, we will explore the specific differences between the two.
Radio frequency circuit board, or RF PCB, is circuit board designed for high frequency and radio frequency signal transmission. Compared to ordinary PCBs, RF PCBs exhibit unique design requirements in a high-frequency environment to ensure effective signal transmission. Impedance matching and signal integrity play a significant role in the design of RF PCBs, which requires the use of special materials such as PTFE (also known as polytetrafluoroethylene) and Rogers, which meet the special needs of RF PCBs by virtue of their extremely low dielectric loss and excellent thermal stability.
The design and manufacturing standards for radio frequency circuit board is even more stringent:
In terms of impedance matching, radio frequency circuit board must achieve accurate impedance matching to ensure that signals are transmitted with minimal reflection and loss.
In terms of signal integrity, RF PCB uses fine wiring and layout strategies to maintain signal stability and accuracy.
As for material selection, RF PCB often uses PTFE, polyimide (PI) and other low dielectric constant materials, which exhibit excellent performance under high frequency conditions.
In addition, the special characteristics of RF signals require higher precision in the manufacturing process of RF PCBs, such as the use of finer drill bits and more accurate line width control.
Difference between ordinary PCB and RF PCB
Material selection is different:
Most ordinary PCBs are made of FR-4, a material favoured for its cost-effectiveness and high mechanical strength for a wide range of electronic applications. In the low to medium frequency range, FR-4 exhibits good performance. However, when applied in high frequency scenarios, its high dielectric constant and losses can lead to increased signal attenuation, making it unsuitable for RF applications.
In contrast, radio frequency circuit board has more stringent material requirements, requiring the use of low-loss, low dielectric constant materials such as PTFE (polytetrafluoroethylene) or ceramic-based materials. These materials demonstrate excellent electrical performance in high frequency environments, effectively reducing losses during signal transmission to maintain signal integrity. Among these materials, PTFE is the preferred material for RF PCBs due to its extremely low dielectric loss and high frequency stability. In addition, materials such as low dielectric constant polyimide (LCP) are also widely chosen to achieve higher signal transmission speeds and better signal quality.
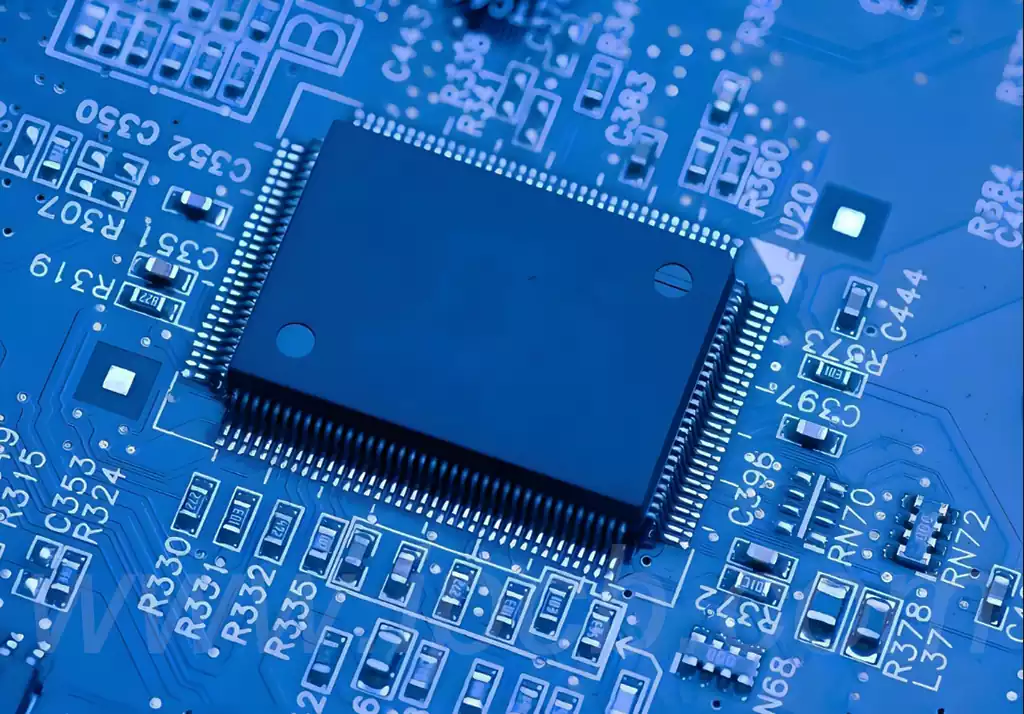
Differences in Signal Transmission and Layout Planning
At the signal transmission level, the design of an ordinary PCB is relatively intuitive, with the core focus on ensuring solid circuit connections and reliable mechanical support. Given that ordinary PCBs usually deal with low-frequency signals, their wiring and layout requirements are relatively loose, and the design process focuses more on the realisation of circuit functions and effective cost control.
Radio frequency circuit board, on the other hand, require extreme precision in the design of signal transmission paths, with the aim of avoiding signal reflection, crosstalk and attenuation to the maximum extent possible. RF signal transmission on the signal integrity has very high requirements, designers must fully consider the signal propagation delay, electromagnetic interference (EMI) and power loss and other factors. Therefore, RF PCBs commonly use differential signal transmission techniques, coplanar waveguide or microstrip line structure, and with the help of multilayer board design to further reduce the interference between the signal. These well-designed layouts and transmission methods work together to ensure the clarity and stability of signals in RF circuits.
Impedance Control
Common PCB in the impedance control is relatively loose, usually do not put forward strict standards for impedance matching. However, in RF PCBs, the accuracy of impedance control is crucial because it is directly related to the quality of signal transmission. The design of RF circuits requires strict matching of the impedance between the signal source, transmission line and load to reduce signal reflection and loss. In order to achieve this, radio frequency circuit board is often designed with precise wire width control and specific stacking arrangements to ensure consistent impedance values.
Manufacturing process differences
General PCB manufacturing process has been relatively mature and cost-effective, mainly including substrate preparation, drilling, plating and soldering assembly and other key aspects. In this process, the accuracy requirements are relatively relaxed, the traditional photolithography and etching technology that can meet its electrical performance standards.
In contrast, the radio frequency circuit board manufacturing process is more complex, the precision and process control requirements significantly increased. Given the high-frequency characteristics of RF signals, RF PCB in lamination, drilling and plating and other links need to maintain a very high degree of precision to ensure the accuracy and consistency of the signal path. In addition, the impedance control of RF PCBs also requires a high degree of material uniformity, and put forward strict standards for the laminated structure, which undoubtedly increases the complexity and cost of its manufacturing process.
Difference in application areas
Ordinary PCB because of its simple design, cost-effective features, in consumer electronics, industrial control and computer hardware and many other fields have been widely used. It is mainly responsible for low-frequency and medium-frequency signal circuit processing work, is an indispensable cornerstone of various types of electronic equipment.
Radio frequency circuit board focuses on high-frequency signal processing, and is mainly used in wireless communication equipment, radar systems, satellite communication platforms and RF spectrum analysers and other high-end fields. These application scenarios put forward strict requirements for the stability of PCBs in high-frequency environments, while emphasising the low-loss and high-fidelity characteristics of signal transmission.
General PCB and radio frequency circuit board each plays an irreplaceable role in its field of application. Although there are significant differences between the two, but they can show their strengths, and jointly promote the continuous progress and development of electronic technology. In the future, with the continuous innovation of electronic technology, ordinary PCB and radio frequency circuit board will continue to shine in their respective fields, to build more intelligent and efficient electronic equipment to contribute.