A drill for pcb board is a device used to perform precise drilling operations on PCBs for the subsequent installation of electronic components such as resistors, capacitors, IC pins, and various other connectors. Drilling is a critical step in the PCB manufacturing process as it ensures electrical interconnections between internal layers of the board as well as between external components and the board.
It mainly consists of a drill, spindle, table, control system and positioning system. The drill head is rotated by the spindle drive, the table is used to fix the PCB and the positioning system ensures the positional accuracy of the drilled holes.
Product working principle: Firstly, the drilling position is determined by the positioning system, and then the PCB is fixed on the working table. Then, the drilling head starts to rotate under the drive of the spindle, and through the precise control of the control system, the drilling head drills the holes according to the set path. Finally, the drilled PCBs are transported to the next production stage through the conveyor belt.
PCB drilling machine has the advantages of high precision, high efficiency and low error. It adopts advanced positional positioning system to realize high-precision drilling. At the same time, its drill speed is adjustable, which can adapt to different drilling needs. In addition, the PCB drilling machine also has the advantage of high automation, which can **improve the production efficiency. It is widely used in the electronic manufacturing industry, such as PCB, membrane switch, FPC and so on. It plays an important role in circuit board processing, SMT assembly, electronic equipment manufacturing and so on.
PCB CNC Drilling Machine is a specialized equipment for processing PCB (Printed Circuit Board), mainly used for drilling holes in circuit boards. It adopts CNC technology for precise control and is characterized by high precision, high efficiency and high reliability.
PCB CNC drilling machine usually consists of drilling machine, CNC system, servo system, air pressure system, cooling system and other parts. Among them, the drilling machine is the core part to realize the drilling function, and the CNC system is the key to realize the precise control.
Compared with the traditional mechanical drilling machine, PCB CNC drilling machine has higher processing accuracy and shorter processing time, which can greatly improve the production efficiency and reduce production costs. In addition, it can process various circuit boards with different specifications and materials, which are widely used in communication, electronics, automotive, medical and other fields.
Laser drilling machine is a specialized equipment used in the electronics manufacturing industry for precision laser drilling in printed circuit boards (PCBs). Utilizing laser technology, these machines are capable of creating tiny and precise holes in PCBs for the manufacturing of high-density circuit boards and microelectronic devices.These machines play a key role in PCB manufacturing in the electronics industry, supporting a variety of applications, including pass-through hole creation, microvia fabrication, and the realization of precision circuit designs.
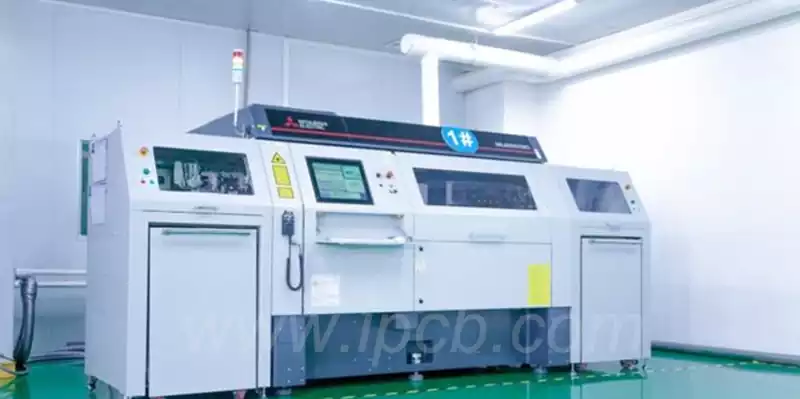
PCB drilling technology is mainly divided into two kinds, mechanical drilling and laser drilling.
(1) Mechanical drilling:
Mechanical drilling is less accurate but easy to perform. This drilling technique relies on drill bits that can drill a minimum hole diameter of about 6 mils (mil) equivalent to: ( 0.1524 mm).
Limitations of Mechanical Drilling.
When used for softer materials such as FR4, mechanical drills can be used for up to 800 impacts. For denser materials, the life is reduced to 200 counts. If this is ignored, it can result in the wrong holes being made, which can lead to board scrap.
(2) Laser drilling:
Laser drilling allows for smaller holes to be drilled. Laser drilling is a non-contact process in which the workpiece and tool do not come into contact with each other. A laser beam is used to remove board material and create precise holes that can be drilled with effortless depth control. Laser technology is used to easily drill over-holes to controlled depths and can accurately drill holes as small as 2 mil (0.05mm) in diameter.
Laser Drilling Limitations.
Circuit boards are made of copper, fiberglass, and resin. These PCB materials have different optical properties that make it difficult for the laser beam to effectively burn through the board. In this case of laser drilling, the cost of the process is also relatively high.
PCB drilling process:
After the lamination process, the laminate is loaded onto a panel of exit material on the drilling machine. The exit material reduces burr formation. Burrs are protrusions of copper formed when the drill spindle penetrates the panel.At the top of this panel,more stacks were loaded and carefully aligned. Finally, a sheet of aluminum foil was placed over the entire stack. The aluminum foil avoids entrance burrs and dissipates the heat generated by the rapidly rotating drill. Once the required number of holes have been drilled, the board is sent for deburring and decontamination.
Since the quality of the drilled holes is a critical aspect, the geometry of the tool must be considered.High-speed steel (HSS) and tungsten carbide WC) are commonly used drill materials for drilling composite materials. Carbide tools provide longer tool life during the processing of glass fiber reinforced polymers (GFRP). Carbide drills are commonly used for PCB drilling.
(1) Tip and helix angles:
PCB drills have a top angle of 130° and a helix angle of 30° to 35. The tip angle is located at the top of the drill. It is measured between the most prominent cutting edges.
(2) CNC Machines:
A drilling machine is a preprogrammed computer numerical control (CNC) machine. Drilling is performed according to the X Y coordinates entered into the CNC system. The spindle rotates at a high RPM to ensure accurate drilling on the board.
Unlike etching and plating processes, the drilling process does not have a fixed duration.The drilling time in the workshop varies depending on the number of holes to be drilled.
Drill for pcb board technology, whether it is the mature application of mechanical drilling or the cutting-edge exploration of laser drilling, demonstrates the relentless pursuit of precision and efficiency in electronics manufacturing.