Electroplated nickel gold (Electrolytic Nickel/Gold) is the originator of the PCB surface treatment process and has been around since the advent of PCBs. It is the process of plating a layer of nickel on the PCB surface conductor before plating a layer of gold. Refers to the way through the plating, so that the gold particles attached to the PCB board, because of the strong adhesion, also known as hard gold; the process can greatly increase the hardness and wear resistance of the PCB, can effectively prevent the diffusion of copper and other metals.
The principle is that the nickel liquid configuration, respectively, gold (commonly known as gold salt) dissolved in chemical solution, the pretreatment of the circuit board immersed in electroplating cylinder (nickel-plated cylinder / gold-plated cylinder) and pass the current in the circuit board on the surface of the copper foil to generate nickel / gold plating, electroplating nickel-gold plating because of its high hardness of the plating layer, wear-resistant, not easy to oxidize the characteristics of the electronic products in a wide range of applications.
In fact, electroplated gold itself can be divided into hard gold and soft gold. Because electroplated hard gold is actually alloy, so the hardness will be relatively hard, suitable for use in the need to force friction, in the electronics industry, generally used as a store circuit board board edge contact point (commonly known as “gold finger”); and soft gold is generally used in COB (Chip On Board) above the aluminum line, or cell phone key contact surface, recently has been a large number of applications in the BGA carrier plate on the front and back sides. If you want to understand the origin of hard gold and soft gold, it is better to understand a little bit about the plating process first. Let’s not talk about the front of the acid washing process, the purpose of plating, basically is to be “gold” plated on the circuit board on the copper skin, but “gold” can not directly react with the copper skin, so it must be plated with a layer of “nickel”, and then plated with gold to the nickel on the surface, so we generally called gold plating, the actual name should be called “electroplated nickel-gold”. The difference between hard gold and soft gold is the composition of the final layer of gold plated on, when plating gold, you can choose to plating pure gold or alloy, because the hardness of pure gold is softer, so it is also called “soft gold”, because gold and aluminum can form a good alloy, so the COB in the aluminum wire will be especially required to play the thickness of the layer of gold. In addition, if you choose to plating gold-nickel alloy or gold-cobalt alloy, because the alloy is harder than pure gold, so it is also called “hard gold”.
Soft Gold: Pickling → Nickel Plating → Gold Pre-Plating → Pure Gold Plating
Hard gold: Pickling → Electroless nickel plating → Pre-gold plating → Electroless nickel or gold-cobalt plating
The role of each component of the plating solution:
Main salt – nickel sulfamate and nickel sulfate for the main salt in the nickel solution, nickel salt is mainly to provide nickel plating of nickel metal ions required and also plays the role of conductive salt. The concentration of the nickel plating solution varies slightly with the supplier, and the permissible content of nickel salts varies greatly. A high nickel salt content allows the use of higher cathodic current densities and faster deposition rates, and is often used for high-speed nickel plating of thick nickel. However, too high a concentration will reduce cathodic polarization, poor dispersing ability, and high carry-over loss of the plating solution. Nickel salt content is low deposition speed is low, but the dispersion ability is very good, can obtain the crystallization of fine bright plating layer.
Buffer – boric acid is used as a buffer to maintain the pH value of nickel-plating solution within a certain range. Practice has proved that when the nickel-plating liquid PH value is too low, will make the cathode current efficiency; and PH value is too high, due to the continuous precipitation of H2, so that close to the cathode surface near the liquid layer of the PH value of the rapid increase, resulting in the generation of Ni (OH) 2 colloid, and Ni (OH) 2 in the plating of the inclusions, so that the plating of the brittleness increased, while Ni (OH) 2 colloid adsorption on the electrode surface, but also cause hydrogen bubble retention on the electrode surface, increasing the porosity of the plating layer. Boric acid not only has a PH buffer, and he can improve the cathodic polarization, thereby improving the performance of the plating solution to reduce the “burning” phenomenon at high current densities. The presence of boric acid also helps to improve the mechanical properties of the plated layer.
Anode activator – In addition to sulfate-type nickel plating solution using insoluble anode, other types of nickel plating process are soluble anode. The nickel anode is easy to passivate in the process of electrification, in order to ensure the normal dissolution of the anode, add a certain amount of anode activator in the plating solution. Through the test, it is found that CI-chloride ion is the best nickel anode activator. In nickel plating solution containing nickel chloride, nickel chloride plays the role of anode activator in addition to being the main salt and conductive salt.
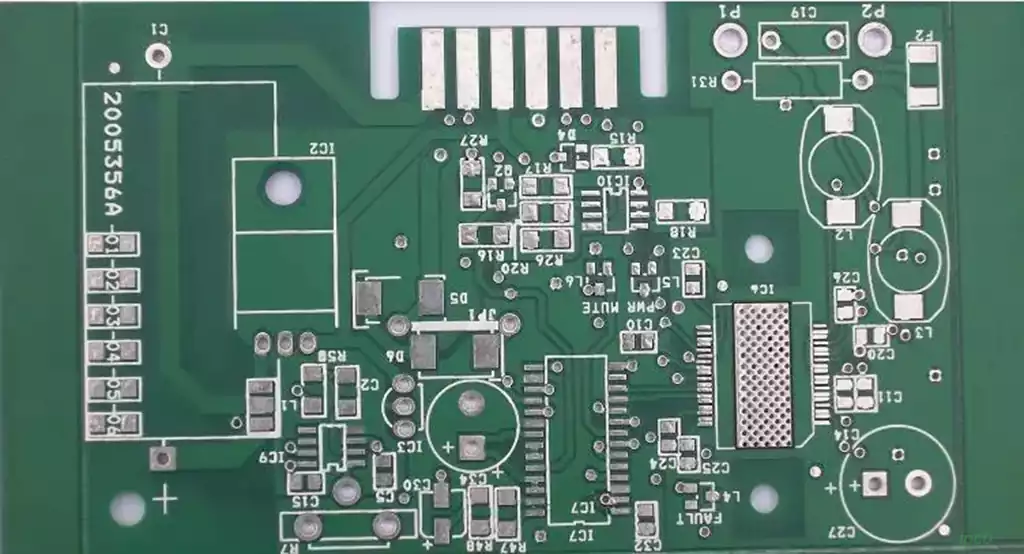
In the nickel plating solution that does not contain nickel chloride or its content is low, a certain amount of sodium chloride needs to be added according to the actual situation. Nickel bromide or nickel chloride is also commonly used as a stress reliever to maintain the internal stress of the plated layer and to give the plated layer a semi-glossy appearance.
Additives – the main pcb component of additives is stress relieving agent, stress relieving agent to join, improve the cathodic polarization of the plating solution, reduce the internal stress of the plating layer, with the change of the concentration of stress relieving agent, the internal stress of the plating layer by tensile stress to change to compressive stress. Commonly used additives are: naphthalene sulfonic acid, p-toluene sulfonamide, saccharin and so on. Compared with nickel plating without a stress relieving agent, the addition of a stress relieving agent to the plating solution will result in a uniformly detailed and semi-glossy plating. Usually stress relievers are added by the ampere hour (now a general combination of specialized additives including anti-pinhole agents, etc.).
Wetting agent – in the plating process, the precipitation of hydrogen on the cathode is unavoidable, the precipitation of hydrogen not only reduces the cathodic current efficiency, but also due to the retention of hydrogen bubbles on the surface of the electrode, but also will make the layer appear pinhole. The porosity of the nickel plating layer is relatively high, in order to reduce or prevent the generation of pinholes, a small amount of wetting agent should be added to the plating solution, such as sodium dodecyl sulfate, sodium diethylhexyl sulfate, sodium n-octyl sulfate, etc., which is a kind of anionic type of surface-active substances, which can be adsorbed on the surface of the cathode, so as to reduce the interfacial tension between the electrode and the solution, and reduce the contact angle of the hydrogen bubbles in the wetting of the electrode, so as to make the gas bubbles can easily leave the surface of the electrode, thus preventing or reducing the generation of pinholes in the plating layer.
Nickel electroplating process
- Pre-treatment: Clean and beat the pcb surface to remove dust and oil.
- Coating primer: apply a layer of primer on the pcb surface to protect the pcb surface in the subsequent nickel electroplating process.
- Copper plating: Immerse the pcb in a copper sulfate solution and deposit copper ions on the surface of the pcb through electric current to form a layer of copper.
- Electroless nickel plating: the pcb after pretreatment is immersed into the electrolyte containing nickel ions, and the nickel ions are deposited on the surface of the pcb through the electric current to form a layer of nickel.
- Electroplating: the pre-treated pcb will be immersed in the electrolyte containing gold ions, through the current so that the gold ions deposited on the surface of the pcb, the formation of a layer of gold.
- Cleaning and inspection: plating good pcb for cleaning and inspection to ensure that its surface is free of pollutants and defects.
Electroplating nickel gold as a PCB surface treatment of the classic process, with its unique advantages in the manufacture of electronic products occupy an indispensable position. From the initial pre-treatment to the final plating completion, each step is carefully planned to ensure that the quality and performance of the PCB board reaches the best state. The hardness and abrasion resistance of the nickel layer, combined with the conductive properties of the gold layer, together provide a solid guarantee for the stable operation of electronic products.