What is electrostatic coating?It is a coating method that uses a high voltage electrostatic field to cause negatively charged paint particles to move in the opposite direction of the field and adsorb the paint particles on the surface of the workpiece. A thicker coating can be obtained in a single application. Spraying equipment consists of spray guns, spray cups and electrostatic spraying high-voltage power supply.
Electrostatic coating is a technique that utilizes a voltage difference to spray powder. Normally, the coated object is grounded as the anode and the spray gun is connected to a negative high voltage power supply as the cathode. In the front of the gun will produce corona discharge, so that the sprayed paint is negatively charged and atomized. We all know that the role of the electric field to follow the “same sex repulsion, opposites attract” principle, negatively charged paint powder under the action of the electric field, along the power line flow to the positively charged surface of the coated material, and finally to achieve uniformity of the paint, solid adhesion effect. There may be small partners have questions, why is the coated object for the anode, the spray gun for the cathode, can not be switched? In fact, there is no problem from the principle, but the critical voltage of negative corona discharge is lower, and it is not easy to produce sparks, safe and stable, so in general, the coated material is grounded as the positive pole.
Process flow
- Surface pretreatment
Before spraying, in order to ensure that the coating can be uniformly attached to the surface of the workpiece, it is necessary to carry out pretreatment. Pretreatment mainly includes cleaning and descaling. Cleaning is mainly to remove oil, dust and other impurities on the surface of the workpiece; descaling is to deal with the oxidized skin and rust on the surface of the metal workpiece to reveal the original color of the metal. The quality of pretreatment directly affects the combination of coating and substrate, so it is an important part of electrostatic spraying process. - Electrostatic spraying equipment
Electrostatic spraying equipment is the core of electrostatic spraying process, mainly composed of spray gun, powder supply, electrostatic generator, recovery device. The spray gun is responsible for atomizing the paint and spraying it onto the surface of the workpiece, the powder feeder is responsible for providing enough paint, the electrostatic generator produces high-voltage static electricity, which makes the paint particles electrically charged and adsorbed on the surface of the workpiece, and the recycling device is responsible for collecting paint particles that are not adhered to the surface of the workpiece to realize the recycling of the paint. - Paint Selection and Blending
In the electrostatic spraying process, the type and performance of the coating have an important influence on the quality of the final coating. Suitable coatings should be selected according to the material of the workpiece, the use of the environment, coating performance requirements and other factors. At the same time, in order to meet the production requirements, it is also necessary to mix the coating according to the actual situation, so that it meets the process requirements. - Electrostatic spraying operation
Electrostatic spraying operation is the key step in the whole process. The operator needs to adjust the distance between the spray gun and the workpiece, angle, flow rate and other parameters according to the parameters of the equipment and the characteristics of the coating, so that the coating particles can be uniformly attached to the surface of the workpiece under the action of the electric field force. At the same time, in order to get a better coating effect, you also need to control the spraying environment temperature, humidity and other conditions. - Curing and cooling
After the coating is attached to the surface of the workpiece, it needs to be cured and cooled. Curing is mainly to make the coating molecules cross-link each other at a certain temperature and time to form a coating with the desired properties. Cooling allows the coating to cool down gradually for subsequent processing and use. The temperature, time and other parameters of curing and cooling need to be set according to the characteristics of the coating to ensure the quality and performance of the coating. - Quality Inspection
After completing the above steps, the coating needs to be tested for quality. The inspection includes appearance quality, thickness, adhesion and so on. Appearance quality is mainly detected by visual or instrumental testing of the flatness and color of the coating; thickness is determined by measurement; and adhesion is to assess the bonding strength between the coating and the substrate. According to the actual needs and standard requirements, corresponding testing and evaluation are carried out to ensure that the quality of the coating meets the requirements.
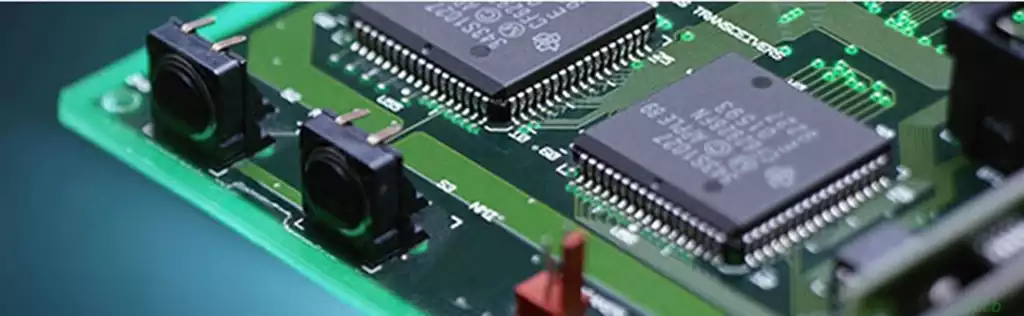
Features
- Suitable for high volume coating production, multiple spray guns spraying at the same time, the efficiency is 1-3 times higher than the traditional spraying.
- Corona discharge atomization is sufficient to make the appearance of the coating film better. By setting the spray gun and adjusting the spraying parameters in advance, a smooth, even, flat and plump coating effect is finally obtained.
- Higher paint utilization rate, under the action of electric field, the paint will reduce the flying and rebound, so the paint utilization rate of electrostatic spraying is as high as 90%, while the paint utilization rate of traditional air spraying is only between 30% and 60%.
- Since in electrostatic spraying, the coated workpiece must be a conductor, it is mainly suitable for spraying metals with good electrical conductivity. If electrostatic spraying is required for objects such as plastic, wood, rubber, glass, etc., surface pretreatment is required in advance.
Advantages
- High spraying efficiency: Electrostatic spraying uses electrostatic action to charge the paint particles, and then spray the charged paint particles onto the surface of the object with the opposite charge, so it can quickly complete the coating task and reduce production costs.
- Save paint: Electrostatic spraying can effectively spray paint on the surface of the workpiece without splashing and wasting like traditional spraying, so it can save the amount of paint used.
- Environmental protection: During the electrostatic spraying process, airless nozzles are used, which reduces the pollution of aerosols to the surrounding environment and helps to protect the ecological environment.
- High spraying quality: electrostatic spraying can complete multiple coats in a shorter period of time, with a more uniform coating quality and a smooth and delicate surface, which improves the quality of the product.
Disadvantages
Harsh construction conditions. Need to be carried out in a dust-free and static-free environment.
Easy to produce sparks. May generate electrostatic sparks due to friction between the coating and air, increasing safety hazards.
High investment cost. The acquisition cost of electrostatic spraying equipment is high.
Limited paint selection. Only specific types of coatings can be used to ensure coating quality.
Difficulty in fine control. Parameters such as spraying pressure, voltage and current need to be precisely regulated.
Limited range of application. It is difficult to obtain a uniform coating for workpieces with complex shapes.
electrostatic coating occupies an important position in the modern spraying process because of its high efficiency, environmental protection and superior quality. Although it has high requirements on construction environment, equipment investment and coating selection, it is undoubtedly an ideal choice for realizing large-scale, high-quality coating production under suitable conditions.