Electrostatic spray coat is the use of high-voltage electrostatic field to make negatively charged paint particles along the electric field in the opposite direction of the directional movement, and will be adsorbed on the surface of the workpiece paint particles of a spraying method.
Electrostatic spray equipment consists of spray gun spray cup and electrostatic spray high voltage power supply. It can not only save paint, reduce the degree of pollution to the environment and can make the spraying process mechanized, continuous, reduce the scrap rate, to obtain excellent film performance, greatly improve labor productivity, improve labor conditions, so as to obtain considerable social and economic benefits.
Generally speaking, the coated material in the coating shall be pre-treatment, so that it is de-oiled, descaled, generated phosphate film, so as to achieve better rust prevention purposes, and spray media better adhesion, electrostatic spray is to be coated as the anode, generally grounded; paint atomization structure for the cathode, connected to the power supply negative high voltage, so that the two poles formed a high-voltage electrostatic field.
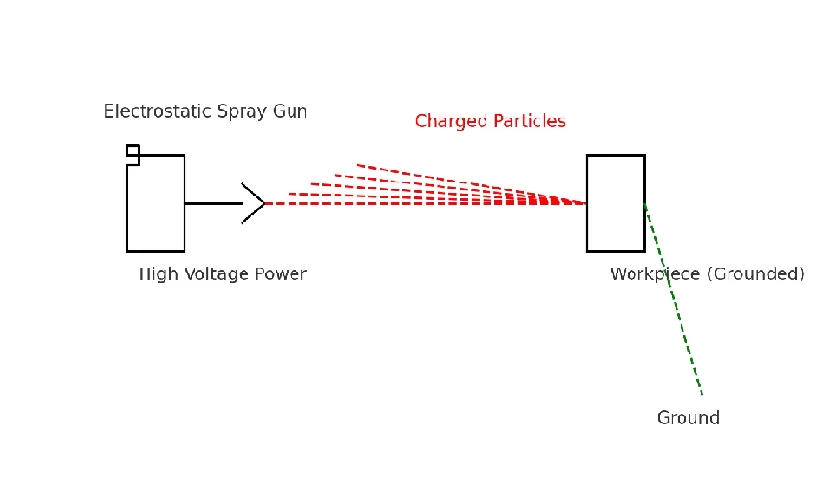
As a result of corona discharge at the cathode, can make the spray paint medium charged, and further atomization. In accordance with the principle of “homogeneous repulsion, heterogeneous attraction”, has been charged by the electric field of the paint medium (F = torsion) along the role of the electric power lines directed to the positively charged surface of the coated material, deposited into a layer of uniform, firmly attached film.
Electrostatic spray coat can also be used positive corona discharge, but the critical voltage of negative corona discharge is lower than the positive corona discharge, and more stable, safe and less likely to produce sparks. Therefore, under normal circumstances will be coated as a positive grounding.
Powder electrostatic spray coat
Powder electrostatic spray is through the spray gun or spray cup electrode needle to the direction of the coated workpiece to release high-voltage static electricity (generally 60 ~ 100 kV), high-voltage static electricity.
So that the spray cup or spray gun sprayed powder and compressed air mixture as well as the surrounding air ionization, due to the high-voltage corona discharge generated by the negative electrode, which produced a dense negative charge, so that the powder is not charged with a negative charge into the electric field strength of a very high static electric field.
Powder in the electric field force and compressed air pressure under the double push to reach the surface of the coated material, the formation of a uniform thickness of the powder layer, and then heated to melt and solidify as a coating film.
(1) Powder coating is a solid coating, no solvent, non-volatile, greatly reducing the pollution caused by solvents, which is conducive to environmental protection and the health of workers.
(2) In the spraying process, the excess spray powder can be collected centrally by using the recycling system to achieve the purpose of recycling and reuse, so the utilization rate of its powder is quite high, which reduces the production cost of the enterprise and obtains better economic benefits.
(3) The whole coating process only needs to go through pre-treatment, spraying, curing and other procedures, simplifying the traditional multi-process spraying means, so that the spraying line is highly efficient, whether it is hand-operated or automatic operation is more convenient.
(4) After powder electrostatic spray, the surface of the coating film with excellent performance can be obtained after baking. The coating film is durable, resistant to acid and alkali, and has the characteristics of abrasion resistance, impact resistance and high mechanical strength. However, due to the powder electrostatic spray is in the development period, so there are inevitably some shortcomings, such as after the spraying of the coating after the existence of impurities, shrinkage, color difference, poor adhesion, etc., these are the future should focus on solving the problem.
Aluminum technology of electrostatic spray process
Electrostatic spray and electrophoretic painting is one of the aluminum profile treatment processes with faster development and more advanced technology in recent years.
Advantages of electrostatic spray coat : energy saving, environmental protection, no pollution, high production efficiency, easy to automate the production of a wide range of product colors to meet the needs of different customers color personality.
Advantages of electrostatic spray paint: high surface finish, color luster crystal, the product surface layer covered with a layer of paint solvent, more corrosion-resistant than the general oxidation of aluminum alloy profiles.
The above are the two ways of electrostatic spray coat I share, thanks!