Among various PCB assembly types, the main PCB assembly is a central component that integrates different electronic components onto a single board. This article explores the intricacies of main PCB assembly, including its process, benefits, challenges, and considerations for effective assembly.
What is Main PCB Assembly?
Main PCB assembly refers to the process of mounting electronic components onto a primary printed circuit board, which acts as the central hub for electrical connections within a device. This assembly process is essential for creating functional electronic products, as it ensures that all necessary components are properly connected and secured on the board.
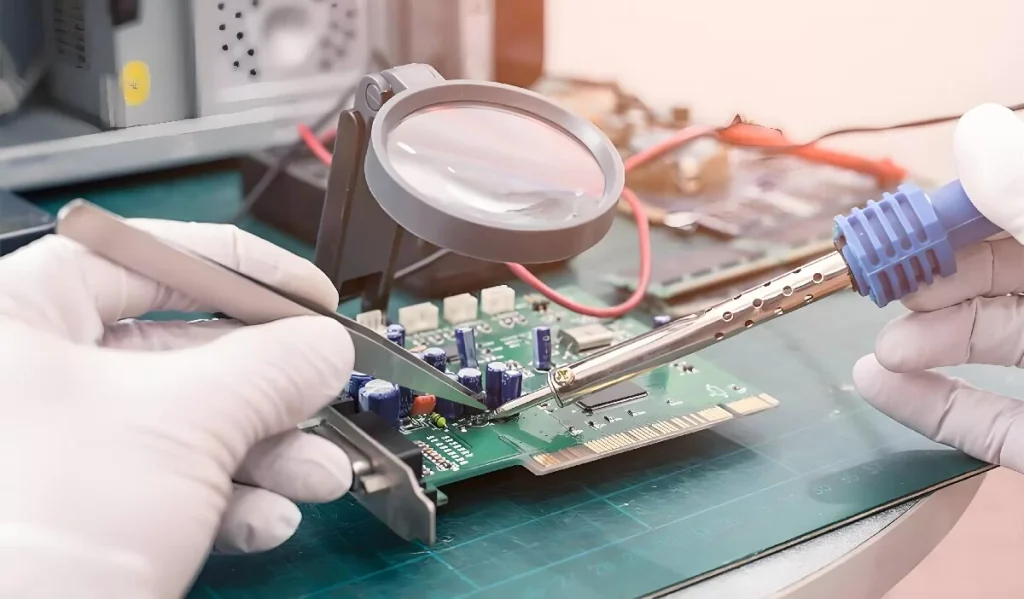
The Process of Main PCB Assembly
The main PCB assembly process involves several stages, each crucial for ensuring the reliability and functionality of the final product. These stages include:
- Design and Preparation: The first step in main PCB assembly is designing the PCB layout. This involves creating a detailed schematic that defines the placement of components and the routing of electrical connections. The design must adhere to specific guidelines to ensure that the assembled PCB meets performance and reliability standards. Once the design is complete, the PCB is fabricated, which involves etching the circuit pattern onto the board and adding necessary layers.The design phase also includes choosing the right materials for the PCB. Different materials have varying electrical and thermal properties, which can affect the performance of the final product. For instance, high-frequency applications may require specialized materials to minimize signal loss and interference. Additionally, the design must consider factors such as thermal management and mechanical stability to ensure that the PCB can withstand operating conditions.
- Component Soldering: After the PCB is fabricated, the next step is component soldering. This involves attaching electronic components to the PCB using solder. There are two primary methods of soldering: surface mount technology (SMT) and through-hole technology (THT). SMT involves placing components directly onto the surface of the PCB and soldering them, while THT involves inserting component leads through holes in the PCB and soldering them on the opposite side. Each method has its advantages and is chosen based on the design requirements and component types.SMT is widely used due to its ability to support high-density component placement and its suitability for automated assembly processes. It allows for smaller and lighter PCBs, making it ideal for compact electronic devices. THT, on the other hand, is often used for components that require strong mechanical connections or for applications where manual assembly is preferred. The choice between SMT and THT can impact the overall design, assembly efficiency, and cost.
- Inspection and Testing: Once the components are soldered onto the PCB, the assembly undergoes rigorous inspection and testing. This step ensures that all components are correctly placed and soldered, and that there are no defects or soldering issues. Various testing methods are used, including visual inspection, automated optical inspection (AOI), and functional testing. These tests help identify any issues that need to be addressed before the PCB is used in a final product.Visual inspection involves examining the PCB for visible defects such as solder bridges, misaligned components, or damaged traces. AOI uses automated systems with cameras to detect defects that may not be visible to the human eye. Functional testing checks the performance of the assembled PCB to ensure that it meets the specified requirements and functions correctly in its intended application. These inspection and testing processes are crucial for ensuring the quality and reliability of the final product.
- Rework and Repair: If defects or issues are identified during the inspection and testing phase, rework and repair are necessary. This involves correcting any errors or defects found in the assembly process. Rework may include resoldering components, replacing damaged parts, or making adjustments to ensure the PCB meets quality standards. Effective rework and repair processes are essential for maintaining the overall quality and reliability of the main PCB assembly.Rework processes should be carefully managed to avoid introducing new defects or causing damage to the PCB. Techniques such as precise soldering and careful component handling are important to ensure that reworked areas meet the same quality standards as the original assembly. In some cases, advanced tools and technologies, such as soldering robots or thermal imaging, may be used to facilitate the rework process and improve accuracy.
- Final Assembly and Integration: The final stage of main PCB assembly involves integrating the assembled PCB into the final product. This may include connecting the PCB to other components or systems, such as enclosures, connectors, and power supplies. The integration process ensures that the PCB functions as intended within the complete electronic device.Integration involves ensuring proper mechanical and electrical connections between the PCB and other components. This may require alignment, securing connectors, and verifying that the PCB fits correctly within the device enclosure. The final assembly phase is critical for ensuring that the PCB performs reliably in its intended application and meets all performance and safety standards.
Benefits of Main PCB Assembly
Main PCB assembly offers several benefits that make it a preferred choice in electronic manufacturing. These benefits include:
- Increased Reliability: A well-executed main PCB assembly process results in a reliable and durable circuit board. Proper soldering, inspection, and testing ensure that the PCB can withstand various operating conditions and perform consistently over time. Reliability is crucial for electronic devices, as it affects their overall performance and longevity.Reliable PCBs reduce the likelihood of failures and maintenance issues, leading to lower warranty costs and higher customer satisfaction. In critical applications such as aerospace, automotive, and medical devices, reliability is especially important, as failures can have serious consequences. The reliability of the PCB is achieved through stringent quality control measures and adherence to industry standards.
- Cost-Effectiveness: Main PCB assembly can be cost-effective, especially when produced in high volumes. The use of automated processes and advanced technologies in soldering and inspection helps reduce labor costs and increase production efficiency. Additionally, the ability to integrate multiple components onto a single PCB reduces the need for additional interconnects and wiring, further lowering costs.Cost savings are achieved through economies of scale, as high-volume production allows manufacturers to spread the cost of setup and tooling across a larger number of units. Automated assembly processes also reduce the need for manual labor and improve production speed. By minimizing the number of separate components and connections, main PCB assembly reduces material costs and simplifies the assembly process.
- Design Flexibility: Main PCB assembly allows for design flexibility, enabling engineers to create complex and compact electronic circuits. By integrating various components onto a single board, designers can optimize the layout and reduce the overall size of the device. This flexibility is beneficial for creating smaller, more efficient electronic products.Design flexibility allows for innovation and customization in electronic products. Engineers can explore new design approaches and incorporate advanced features while maintaining compact and efficient layouts. This is particularly valuable in industries such as consumer electronics, where space constraints and form factors play a significant role in product design.
- Improved Performance: Properly assembled PCBs contribute to improved electrical performance. A well-designed and assembled PCB minimizes signal interference and ensures reliable electrical connections between components. This enhances the overall performance of the electronic device and helps achieve desired functionality.Improved performance is achieved through careful design considerations, such as minimizing signal paths, reducing noise, and optimizing component placement. High-performance PCBs ensure that electronic devices operate efficiently and meet performance specifications, which is critical for applications requiring high-speed or high-frequency operation.
- Simplified Manufacturing: Main PCB assembly simplifies the manufacturing process by consolidating multiple components onto a single board. This reduces the complexity of wiring and assembly, streamlining production and reducing the likelihood of errors. Simplified manufacturing processes lead to faster production times and improved consistency in the final product.Simplified manufacturing processes reduce the risk of assembly errors and streamline production workflows. By integrating multiple components onto a single PCB, manufacturers can achieve greater consistency and efficiency in production. This leads to faster time-to-market and improved product quality.
Challenges in Main PCB Assembly
Despite its advantages, main PCB assembly also presents several challenges that manufacturers must address. These challenges include:
- Complexity of Design: As electronic devices become more advanced, PCB designs become increasingly complex. This complexity can pose challenges in the assembly process, requiring careful planning and execution to ensure that all components are correctly placed and soldered. Complex designs may also necessitate more advanced inspection and testing methods to identify potential issues.Complex designs often involve high-density component placements, fine-pitch components, and intricate routing. These factors can increase the difficulty of assembly and require specialized equipment and techniques. Manufacturers must invest in advanced technologies and skilled personnel to handle complex PCB designs effectively.
- Soldering Issues: Soldering is a critical step in main PCB assembly, and issues such as solder bridges, insufficient solder, and cold solder joints can affect the quality and reliability of the PCB. Ensuring proper soldering techniques and conducting thorough inspections are essential for minimizing soldering issues and ensuring a high-quality assembly.Soldering issues can lead to poor electrical connections, signal interference, and mechanical failures. Addressing these issues requires precise control over soldering processes and adherence to best practices. Manufacturers must also invest in training and quality control measures to prevent and detect soldering defects.
- Component Compatibility: Main PCB assembly involves integrating various electronic components, which must be compatible with each other and with the PCB design. Compatibility issues can arise if components have different sizes, lead configurations, or electrical requirements. Careful selection and placement of components are necessary to avoid compatibility problems and ensure optimal performance.Component compatibility issues can lead to assembly errors, performance problems, and increased production costs. Manufacturers must carefully review component specifications and design requirements to ensure that all components are compatible and function as intended. Proper component selection and placement are critical for achieving successful PCB assembly.
- Quality Control: Maintaining consistent quality throughout the main PCB assembly process is crucial for ensuring the reliability of the final product. Implementing effective quality control measures, including inspection and testing, helps identify and address defects or issues early in the process. Quality control is essential for achieving high standards and meeting customer expectations.Effective quality control involves implementing robust inspection and testing procedures, monitoring production processes, and addressing any deviations from quality standards. Regular audits and reviews help identify areas for improvement and ensure that quality control measures are effective in maintaining product reliability.
- Environmental Considerations: PCB assembly processes must consider environmental regulations and standards. For example, restrictions on the use of lead in solder and other materials require the use of lead-free alternatives. Manufacturers must adhere to these regulations while ensuring that the assembly process remains effective and efficient.Environmental considerations include compliance with regulations such as RoHS (Restriction of Hazardous Substances) and WEEE (Waste Electrical and Electronic Equipment). Manufacturers must ensure that their PCB assembly processes meet these standards while maintaining product performance and quality. The use of lead-free materials and environmentally friendly practices is essential for sustainable manufacturing.
Key Considerations for Effective Main PCB Assembly
To achieve effective main PCB assembly, manufacturers should consider the following key factors:
- Design Optimization: Optimizing PCB design for assembly can improve the efficiency and quality of the process. This includes considering factors such as component placement, soldering techniques, and board layout to ensure that the assembly process is smooth and effective.Design optimization involves evaluating the impact of design choices on the assembly process and making adjustments to improve efficiency and reduce potential issues. Engineers should consider factors such as component accessibility, thermal management, and mechanical constraints when designing PCBs for assembly.
- Automated Processes: Implementing automated processes for soldering, inspection, and testing can enhance efficiency and consistency in main PCB assembly. Automation reduces the risk of human error and increases production speed, leading to higher quality and lower costs.Automated systems can perform repetitive tasks with high precision and speed, improving overall production efficiency. Technologies such as automated soldering machines, AOI systems, and automated test equipment contribute to consistent and reliable PCB assembly. Manufacturers should invest in automation to achieve higher productivity and quality.
- Skilled Workforce: A skilled workforce is essential for successful main PCB assembly. Technicians and engineers must be trained in the latest techniques and technologies to ensure that the assembly process is executed correctly and that quality standards are met.Training programs and ongoing education are important for maintaining a skilled workforce. Technicians should be proficient in soldering techniques, inspection methods, and troubleshooting procedures. Skilled personnel contribute to the overall quality and efficiency of the PCB assembly process.
- Regular Maintenance: Regular maintenance of equipment and machinery used in PCB assembly is important for preventing issues and ensuring consistent performance. Well-maintained equipment contributes to the overall quality and reliability of the assembly process.Maintenance practices include routine inspections, cleaning, and calibration of equipment. Manufacturers should establish maintenance schedules and procedures to ensure that machinery operates effectively and remains in good condition. Regular maintenance helps prevent downtime and production delays.
- Continuous Improvement: Manufacturers should continuously evaluate and improve their main PCB assembly processes. This includes seeking feedback, analyzing performance metrics, and implementing changes to enhance efficiency, quality, and overall effectiveness.Continuous improvement involves monitoring key performance indicators, identifying areas for improvement, and implementing process changes. Manufacturers should encourage a culture of innovation and problem-solving to drive ongoing improvements in PCB assembly. Regular reviews and feedback from customers and stakeholders help guide improvement efforts.
Conclusion
Main PCB assembly is a crucial aspect of electronic manufacturing, involving the integration of various components onto a primary circuit board. The process offers numerous benefits, including increased reliability, cost-effectiveness, design flexibility, improved performance, and simplified manufacturing. However, it also presents challenges such as design complexity, soldering issues, component compatibility, quality control, and environmental considerations.
By addressing these challenges and focusing on key considerations for effective assembly, manufacturers can achieve high-quality main PCB assemblies that meet performance and reliability standards. As technology continues to advance, the main PCB assembly process will evolve, offering new opportunities and innovations in electronic manufacturing. Understanding and optimizing this process is essential for creating successful electronic products and staying competitive in the industry.