Flex cut technology usually refers to the use of lasers or high-precision mechanical tools to cut circuit boards made of flexible materials (e.g. polyimide, etc.). This technology is known for its high precision, efficiency and flexibility to meet the needs of cutting complex shapes and small sizes. This technology typically uses a laser or mechanical tool as the cutting tool, combined with an advanced control system to enable precise cutting of complex shapes and small dimensions.
In contrast, non-flex cut technology is mainly used to cut circuit boards made of rigid materials. These materials are often hard and stable and therefore require more powerful cutting tools such as diamond saw blades or high-speed rotating milling cutters. Non-flexible cutting technology is characterized by its high efficiency, stability and suitability for mass production, and occupies an important position in automotive electronics, industrial control and other fields.
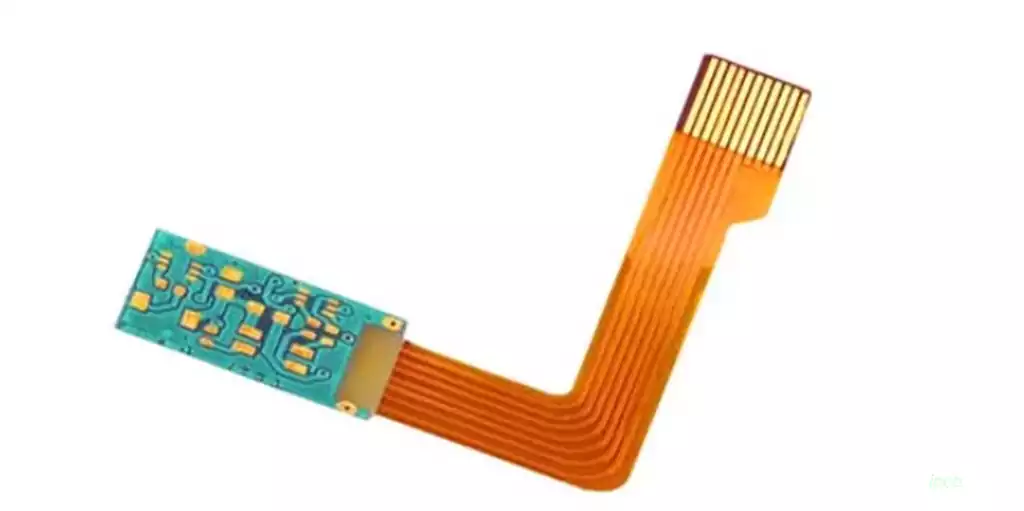
Features of PCB flexible cutting technology
High accuracy: Flexible cutting technology can achieve micron-level cutting accuracy, ensuring the precise position of each component on the PCB.
High flexibility: the technology is applicable to PCB of various materials and shapes, including flexible PCBs and rigid-flexible composite PCBs.
High production efficiency: Flexible cutting technology can quickly complete the cutting of a large number of PCBs and improve production efficiency.
High safety: The use of laser or mechanical tools for cutting reduces the danger of traditional methods such as chemical corrosion.
Application Scenarios and Advantages
Flexible cutting technology excels in electronic devices that require frequent bending, folding or twisting due to its high flexibility and precision. For example, in wearable devices, flexible circuit boards can closely fit human body curves and provide a more comfortable user experience. In addition, flexible cutting technology is also suitable for the manufacture of circuit boards with complex shapes, such as curved shapes and spirals, providing designers with more room for creativity.
Non-flexible cutting technology, on the other hand, with its high efficiency and stability, in the need for mass production, the stability of the circuit board requires a higher field has obvious advantages. In automotive electronics, rigid circuit boards can provide more stable and reliable electrical connections to ensure the normal operation of the vehicle in a variety of complex environments. In addition, non-flexible cutting technology is also suitable for the manufacture of larger size, simple structure of the circuit board, such as computer motherboards, server boards and so on.
Flex cut vs non flex cut pcb technology are two indispensable processing technologies in the electronics manufacturing industry. They each have unique advantages and application scenarios, and play an important role in the electronic manufacturing industry. With the continuous updating of electronic products and changes in market demand, these two technologies will also continue to develop and innovate, injecting new momentum into the future development of the electronics manufacturing industry.