FPCA is the abbreviation of Flexible Printed Circuit Assembly, which refers to the hardware substrate formed by soldering electronic components to a flexible circuit board (FPC, Flexible Printed Circuit).
It is widely used in communication, consumer electronics, automotive field. Automotive electrification, intelligence has opened up a broader market space for it, power batteries, sensors, cameras need to use it. Take the car battery as an example, before the new energy vehicle power battery collection line using traditional copper wire harness program, compared with the traditional wire harness, it has a high degree of integration, automated assembly, assembly accuracy, ultra-thin thickness, ultra-softness, lightweight, and many other advantages, especially in the automation and lightweight outstanding performance. New energy vehicles as the main line of the future development of the automotive industry, automotive FPCA to replace the traditional copper wire harness has become mainstream. With the increase in the application of sensor technology and the gradual penetration of the Internet to the car, the trend of automotive electronics is becoming more and more obvious, FPCA in the car’s dosage ratio will also get a significant increase.
The importance of new energy vehicle FPCA cleaning
The safe, reliable and stable operation of new energy vehicle power devices is the core requirement of energy storage batteries and a prerequisite, and the FPCA collection line is an important part of the battery management system of new energy vehicles, and it is very important for the monitoring of the operational status of energy storage batteries and the transmission of information.
FPCA production process, in order to ensure the electrical stability of it and long-term service life, improve the appearance of the quality of the fpc assembly residue cleaning after welding is particularly important, usually need to flexible circuit board assembly welding flux, solder paste residue and assembly process of oil, dust, handprints and so on.
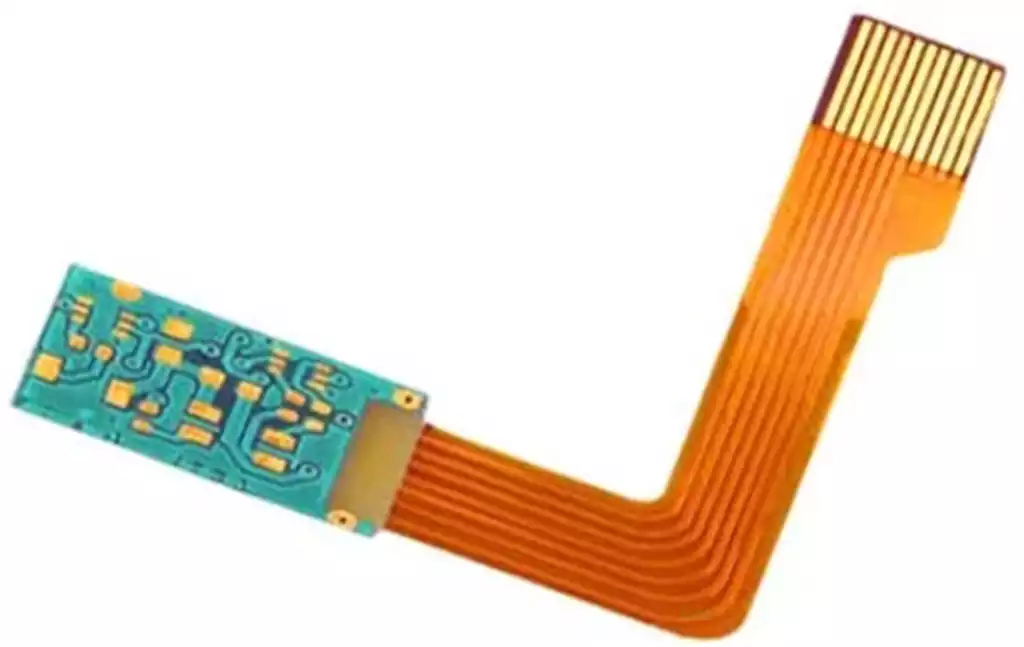
Production process:
Substrate preparation: select the appropriate flexible insulating substrate, which is the basis of the FPC board, determines the flexibility and reliability of the circuit board. The choice of substrate needs to take into account factors such as the end use of the circuit board, the working environment and the required electrical properties.
Graphic Design: According to the circuit design requirements, CAD (Computer Aided Design) software is utilized to draw the circuit graphics. This includes determining the size of the board, wiring paths, component locations, etc.
Production of Masking Plates: Based on the designed circuit graphics, masking plates are produced. The mask plays a key role in the subsequent printing and etching process to ensure accurate reproduction of the circuit pattern.
Printing the circuit: Using screen printing or gravure printing technology, conductive ink or copper foil is uniformly printed on the substrate. The printing process requires strict control of the thickness and uniformity of the printing to ensure stable performance of the circuit.
Etching and molding: After printing, the substrate needs to be etched to remove the unwanted conductive parts and form the circuit pattern. Then, molding is performed according to the design requirements to give the circuit board the desired shape and size.
Soldering and Assembly: Electronic components are soldered on the circuit board to form a complete FPCA. this step requires precise control of soldering temperature and time to ensure the quality of soldering. At the same time, the necessary assembly work is performed according to the product requirements.
Inspection and Testing: Electrical performance test, appearance inspection and reliability test are performed on the completed board to ensure that the product meets the design requirements and quality standards.
Packaging and shipping: The tested and qualified it is packaged and then shipped according to customer requirements.
The entire FPCA production process requires strict quality control at all stages to ensure that the final product has stable performance and high reliability. With the continuous progress of science and technology, FPCA production technology is also constantly updated and optimized to meet the development needs of the electronics industry.