What is fr4 material? FR4 material is a widely used composite material, mainly composed of glass fiber and epoxy resin. The name “FR4” indicates that the material meets the requirements of the flame retardant class, meaning that it is self-extinguishing in a burning state, which has led to the widespread use of FR4 materials in the manufacture of circuit boards.
The main components of FR4 material is woven glass fiber cloth and fire-resistant epoxy resin. This combination gives FR4 materials good mechanical strength, electrical insulation and thermal stability, making them adaptable to a wide range of electronic applications.
The “FR” in FR4 stands for “flame retardant,”which means that FR4 material is able to prevent the spread of flame under certain conditions and meet UL94V-0 flame retardant standards.This property is one of the key reasons why FR4 materials are preferred for circuit boards and other electronic products.
FR4 materials have good heat resistance and typically operate in temperatures ranging from 105°C to 200°C. Within this range, FR4 materials maintain good mechanical strength and insulation properties. For example, at temperatures up to 150°C, FR4 still maintains its structural integrity and electrical properties. However, at higher temperatures, such as when subjected to lead-free soldering, the decomposition temperature of FR4 may reach 288°C. Under such conditions, it is important to ensure that the Tg value meets the high temperature requirements to avoid degradation of the material’s performance. Performance is also relatively stable at low temperatures, with a range of use temperatures generally down to -45°C. At this temperature, FR4 materials exhibit good mechanical and electrical properties and are not prone to embrittlement and fracture. However, very low temperatures may affect the flexibility of the material, leading to possible poor performance in some applications.
As temperatures increase, FR4 materials undergo thermal expansion, which can lead to dimensional changes that can affect the interface and connection reliability of the PCB. In practice, designers need to consider the coefficient of thermal expansion at different temperatures to ensure a good fit between components.The glass transition temperature of FR4 is typically between 130°C and 170°C, which determines the critical point at which the material changes from a rigid to a soft state. When the temperature exceeds Tg, the mechanical properties of FR4 are significantly reduced, which is a critical factor in high temperature applications . The application of high Tg FR4 improves the stability of the material at high temperatures, which is particularly important for circuit boards that operate in high temperature environments for long periods of time.
FR4 has a very low moisture absorption rate, preventing moisture from damaging its structure and properties. The use of FR4 materials in humid environments avoids performance degradation, which allows it to maintain good working performance in a variety of climatic conditions.
FR4 materials are widely used in several fields, especially in the electronics industry, because of their unique properties.
It is the preferred substrate for manufacturing printed circuit boards (PCBs). Its excellent electrical insulation properties and high temperature resistance ensure that it can maintain stable electrical performance in high frequency and high temperature environments. In practical applications, FR4 materials can effectively support circuit connections and reduce signal interference in a variety of electronic devices, including cell phones, routers and fiber optic communication equipment.
It also excel in scaffolding and insulating support materials for electronic components. Its high mechanical strength and good stability enable FR4 to play an important role in complex applications.These components need to operate at high temperatures and under high loads,so the heat and moisture resistance of it is particularly important.
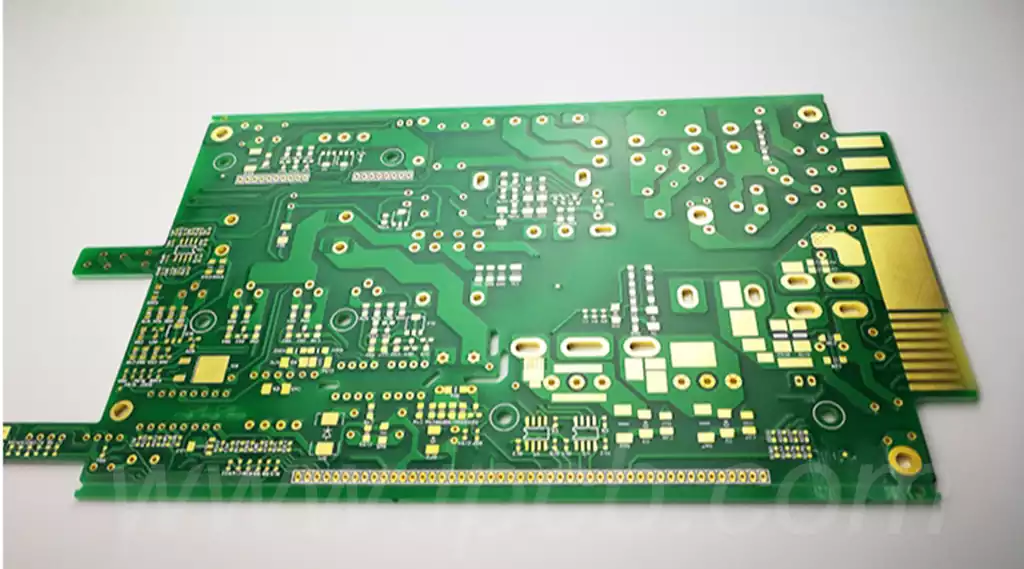
While FR4 performs well in most applications,in high-frequency applications,its high dissipation factor (Df) results in more signal loss compared to materials designed for high-frequency applications.This means that FR4 may not be as desirable as other specialized materials in extreme high frequency situations, but is still an acceptable choice for general high frequency applications.
FR4 also has a wide range of applications in industrial and mechanical manufacturing, being used for many lightweight mechanical components and mold linings. These applications require materials with good heat resistance and processability, and FR4 has the physical properties to meet these requirements.
In medical devices, the electrical insulation properties of FR4 and its stability at elevated temperatures make it a popular choice, especially in applications requiring high precision and reliability. Medical devices often need to function properly under changing environmental conditions, and the excellent properties of FR4 can effectively safeguard the safety and performance of the devices.
The manufacturing of FR4 epoxy glass fiber board usually includes the following steps:
- Glass fiber pretreatment: the glass fiber cloth will be pre-treated to remove impurities and improve the bonding between the fibers. The pretreatment process usually includes washing, drying and coating.
- Resin impregnation: The pre-treated glass fiber cloth is placed in the impregnation tank and impregnated with epoxy resin. The impregnated fiberglass cloth is flattened by squeezing or roller pressing so that the resin fully penetrates the fibers.
- Lamination and sheet metal: Multiple layers of impregnated fiberglass cloth are laminated together according to design requirements and compacted to form a substrate of uniform thickness. The laminated material is further cured by heat and pressure to cure the resin.
- Rough machining and leveling: The cured substrate undergoes rough machining, such as cutting, polishing punching, etc., to achieve the required size and precision requirements, and the surface of the substrate is made flat and smooth through leveling.
FR4 material is ideal for modern electronics and a wide range of applications due to their excellent electrical insulation properties, mechanical strength and heat resistance. From the manufacture of printed circuit boards to supports for electronic components to industrial and medical device applications, FR4 materials demonstrate their unique performance advantages.