Hot swappable pcb is a technical operation in which circuit boards are inserted or removed from a system that operates under power. This technology allows users to replace or upgrade circuit boards without powering down or disconnecting the system, thereby improving system reliability, quick repairs, redundancy, and timely recovery from disasters.
Hot-plugging is a way of replacing or adding electronic components while the power is on, which can greatly improve the maintainability and expandability of equipment, reduce downtime, and bring convenience to users.
Hot-plugging technology depends on the hardware structure and software system support. At the hardware level, the premise of achieving hot-plugging is that the device itself needs to have the function of compatibility, and assembled with the corresponding slot and interface components. Once a new device is connected to the running equipment system, the hardware system can automatically sense the existence of the new device and quickly complete the circuit connection. At the software level, hot-plugging also needs to be supported by the operating system. After the new device is connected, the operating system needs to have the ability to automatically recognise and install the appropriate drivers to ensure that the new device can be put into operation smoothly.
How Hot swappable pcb work
Detection Mechanism: Hot swappable pcb is usually equipped with sensors to detect insertion and removal actions. The detection mechanism ensures that the system reacts in a timely manner to changes in the connection status of the circuit.
Power Management: Providing safe power switching is key to enabling hot-plugging. Specific power management integrated circuits (PMICs) regulate the current when the board is inserted or removed, ensuring that the system is not subjected to shock.
Data Transfer Protocols: Hot swappable pcb often uses specific data transfer protocols (e.g., USB, SATA, PCIe, etc.) that allow for fast and stable information transfer during board insertion and removal, reducing system instability.
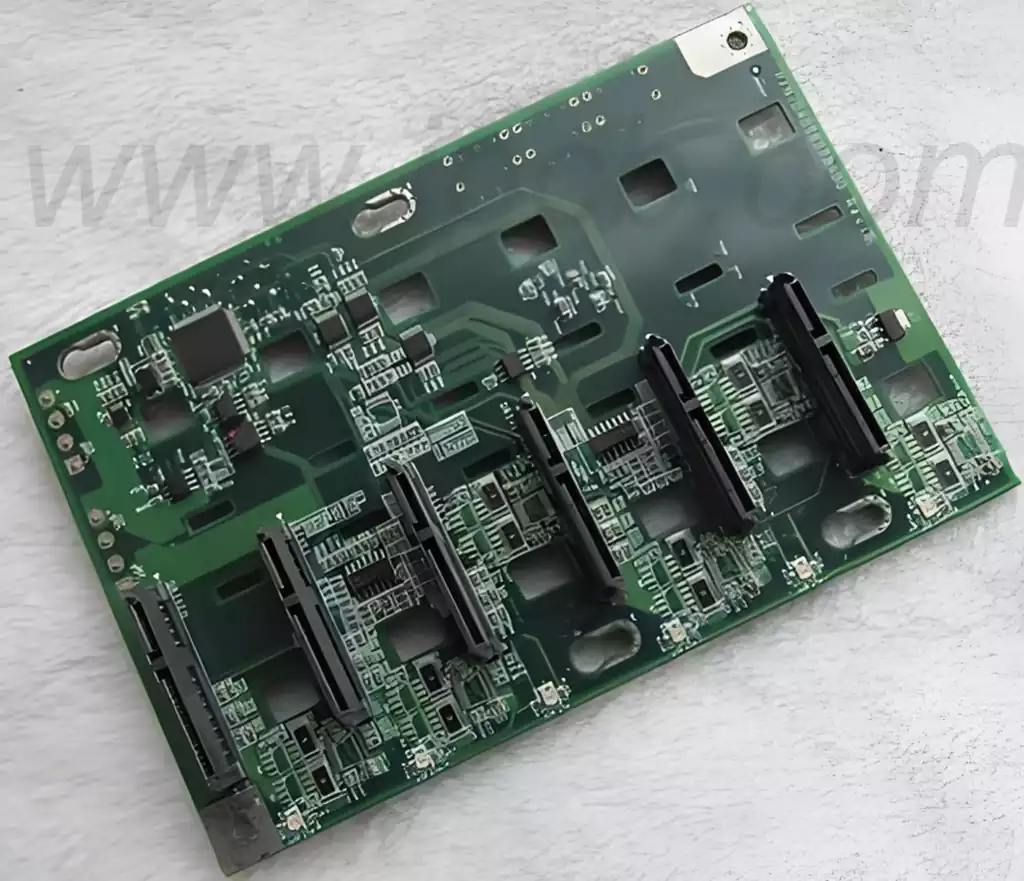
Scenarios for hot swappable pcb
Data Centres and Servers
In data centres and servers, high availability is essential. Hot swappable pcb enables maintenance and upgrades to be performed without interrupting service, ensuring system continuity and reliability. For example, when a network interface card fails, administrators can immediately replace it with hot-swappable functionality without disrupting service, which is critical to providing 24/7 service.
Communications Infrastructure
In a communications infrastructure, hot swappable pcb enables rapid restoration of services, for example, in the event of a failure, the faulty module can be quickly replaced to maintain the stability of the communications link. Using hot-swappable technology, it is possible to easily maintain and update all types of communication equipment, achieving the high performance and reliability required.
Computers and External Devices
Personal computers and a variety of external devices (such as printers, storage devices, etc.) often use hot-plugging technology. Users can add or remove devices at any time as needed without restarting the computer, greatly improving the convenience of use. For example, hot-plugging of USB devices is widely used in mobile storage devices, allowing users to plug and unplug these devices conveniently.
Industrial Automation and Control Systems
In industrial automation and control systems, the use of hot swappable pcb makes it easier to maintain and replace equipment. Any downtime in a factory production environment can lead to significant financial losses, so the use of hot-swap technology allows faulty modules to be replaced without affecting the operation of other equipment, thus improving overall productivity.
Medical Equipment
In the field of medical equipment, the use of hot-swap technology is equally important. For example, in first aid equipment and monitors, replacement and upgrading can be carried out seamlessly to ensure the continuity of medical services and the stability of the equipment, and to avoid safety hazards due to equipment failure during emergency treatment.
High Performance Computing (HPC) Cluster
In HPC clusters, system reliability and scalability are critical. Hot swappable pcb allows users to dynamically increase processing power during operation to meet transient load demands. This is especially important in data processing-intensive applications, allowing the cluster to adapt to changes in various workloads.
Measures to ensure hot swappable pcb safety
Use of appropriate connector design
The choice of connector has a significant impact on the safety of hot-swap operations. The use of staggered pin connectors ensures a safe connection during plugging and unplugging, ensuring that ground and power are connected before other signals are connected. This design reduces the risk of short circuits and electrical shocks.
Implement overcurrent and short-circuit protection
Hot swappable pcb should be equipped with current protection monitoring devices. When boards are plugged in or unplugged, load currents can change dramatically, potentially leading to overcurrents or short circuits. Using a hot-plug controller, such as the ADM1177, you can monitor the current and protect the board and connected loads in the event of a fault. These controllers prevent additional damage by triggering the circuit to disconnect.
Use the right algorithms and control logic
During hot-swapping, an overcurrent prevention algorithm should be implemented that effectively prevents current inrush due to plugging and unplugging by limiting the current and soft-starting. For example, a linear current limiting method can be used to ensure that the device operates safely and stably in high load environments.
Ensuring Thermal Management
Thermal management is another key factor in the safety of hot swappable pcb. It should be ensured that the boards are thermally well designed, including sensible heat dissipation and effective thermal protection measures to prevent overheating and consequent failure. Apply e.g. temperature monitoring and control circuits to the design to ensure that multiple components do not fail due to elevated temperatures.
Regular Maintenance and Testing
Regular maintenance and testing of hot swappable pcb to verify their safety and reliability is a prerequisite to ensure long-term trouble-free operation. The board’s connection points, protection circuits and thermal management system should be evaluated and necessary improvements and remedial measures should be made to ensure safe operation of the circuit.
Hot swappable pcb technology significantly improves system reliability and user experience through its efficient and safe features. To ensure its long-term stability, safety design and regular maintenance are required to take full advantage of the technology.