Selecting the right PCBA process is a strategic decision that can have a decisive impact on product quality, productivity and cost-effectiveness. In the face of a wide range of process options, it is important to consider several key factors to ensure that the selected process can fit the product requirements, while adapting to production conditions and market demand.
Product design characteristics
Complexity of the board design: Complex designs with multi-layer structures, high-density wiring, and fine-pitch components may require more elaborate SMT (surface mount technology) processes, especially with high-precision placement machines and advanced reflow soldering equipment to ensure accuracy.
Product Type and Functionality Oriented Process Selection
Consumer Electronics
Characteristics: Consumer electronics products, such as smartphones, tablet PCs and smartwatches, generally pursue miniaturised designs, excellent performance and high reliability. These products place stringent demands on board space while supporting high-speed signal transmission and complex functional integration.
Process preference: For these products, High Density Interconnect (HDI) processes are ideal, as they significantly reduce line widths and spacing, and enable denser hole configurations (e.g., blind vs. buried holes), resulting in significantly higher board densities. In addition, the high-precision placement process of surface mount technology (SMT) is also indispensable to ensure that tiny components, such as 0201 packages and fine-pitch BGA chips, can be mounted accurately. Special signal integrity design processes, such as differential pair wiring and close coupling of signal and ground layers, are also incorporated to meet the demands of high-speed signal transmission.
Industrial Control Products
Features: Industrial control products, including PLCs (Programmable Logic Controllers), industrial computers, and motor drives, etc., are usually required to operate stably in harsh industrial environments, which puts high demands on board stability, anti-interference, and durability. These products have complex functions, which may involve analogue signal processing, digital logic control and high-power drive and other functions.
Process preference: In the PCBA process, should focus on considering the circuit board protection process. For example, the use of high-quality moisture, mould and corrosion-resistant coating process, such as three-proof paint coating, to protect the circuit board from moisture, dust and chemicals in the industrial environment. For high-power components, plug-in processes are preferred to ensure good heat dissipation and electrical connections. At the same time, in order to improve the anti-interference ability, need to pay attention to the electromagnetic compatibility (EMC) design, such as rational planning of grounding layout, the use of shielding and the design of filtering circuits.
Medical equipment products
Characteristics: Medical equipment, such as electrocardiographs, diagnostic ultrasound equipment and medical monitors, etc., have very high requirements for the safety, precision and reliability of circuit boards. Circuit boards for these devices may come into direct contact with the human body or be used in life support systems, so any malfunction can have serious consequences.
Process preference: In PCBA process, high-quality, highly reliable components should be selected and strict quality testing processes should be implemented. For example, 100% aging test and performance screening of critical medical electronic components. The soldering process needs to ensure the high quality and long-term reliability of the solder joints to meet the requirements of the longer service life of medical equipment. At the same time, in order to prevent the potential impact of electromagnetic radiation on medical devices and the human body, excellent EMC processes need to be adopted and compliance with relevant medical device EMC standards, such as the IEC 60601 series standards, needs to be ensured.
Types of components and packages: Different types of components and their package types (e.g. QFP, BGA, 0201, etc.) have specific requirements for placement accuracy and soldering processes. Some large, irregularly shaped or specially packaged components may require a combination of hybrid (i.e. SMT and THT) or hand soldering techniques.
Size and Weight Considerations: For large or heavyweight PCBs, special supports and fixtures may be required to prevent warping or deformation during processing. In addition, these characteristics may affect the choice of production line and its layout design.
Specificity of functional requirements: If the product has specific requirements for EMC (electromagnetic compatibility), heat dissipation performance, RF performance, etc., it may require the use of specific PCBA process processing measures, such as impedance control, shielding layer processing and the use of special soldering materials.
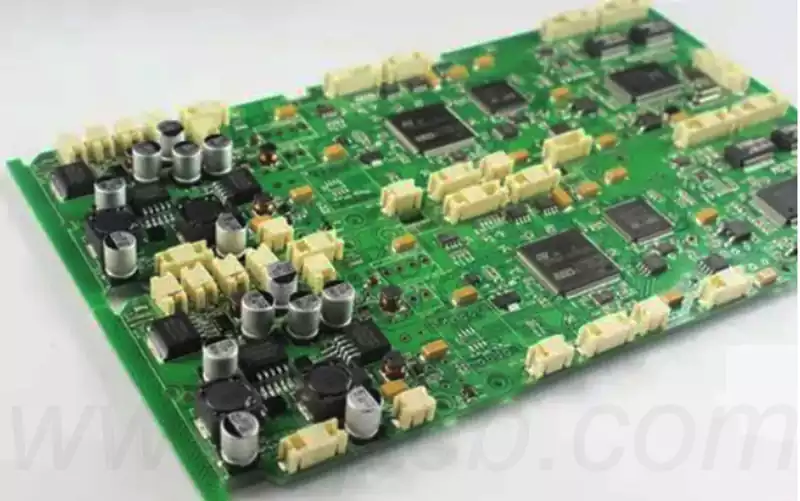
Production scale and efficiency considerations:
Production Lot Size: Large-scale production tends to rely on fully automated SMT lines to achieve efficient and consistent production output. In contrast, small lot sizes or customised production tasks may be better suited to semi-automatic or manual soldering processes, which maintain flexibility and control costs.
Tight lead times: When faced with the need for fast delivery, it is critical to choose processes and equipment that can respond quickly, such as solder paste printers with easy mould changes and mounters with flexible programming capabilities.
The pace of production: In a high-paced production environment, select equipment that supports high-speed placement and continuous reflow, and optimise the line configuration to match this pace.
Quality and reliability assurance:
Process validation process: Based on authoritative standards such as IPC (International Association for Interconnection and Packaging of Electronic Circuits), assess and validate the process capability to ensure that the selected process can meet the reliability requirements of the product.
Quality control measures: Selection of processes equipped with in-line inspection equipment such as SPI (solder paste inspection system), AOI (automatic optical inspection system) and AXI (automatic X-ray inspection system), so that defects can be detected and corrected at an early stage.
Reliability testing programme: Depending on the actual application environment of the product, a series of environmental tests, such as thermal shock test, vibration test and humidity test, may be required to ensure the stability and durability of the PCBA in actual use.
Environmental regulations compliance:
If the products are mainly sold to countries and regions with strict environmental requirements, such as Europe, North America, etc., the choice of lead-free process is more in line with market demand and regulatory requirements.
The choice of PCBA process needs to be fully weighed product design, production scale, quality and reliability and environmental requirements to ensure that the process and product characteristics, market demand and regulatory standards are highly compatible with the