The PCB glass transition temperature (abbreviated Tg) is the temperature at which a material changes from a solid (glassy) state to a soft (rubbery) state. In other words, this temperature is the limit at which a phase change occurs in the substrate, and when the temperature reaches or exceeds this value, the physical properties of the material change significantly. When the temperature is below Tg, the material remains rigid and brittle, while when the temperature is above Tg, the material becomes soft and moldable.
The pcb glass transition temperature plays a crucial role in PCB design and manufacturing. PCB materials with high Tg values typically have higher heat resistance and stability, which is especially important for high-performance electronics. In high-temperature environments, low Tg materials may cause deformation or performance degradation of the board, while high Tg materials are able to maintain structural integrity and stability, accommodating multilayer and high-density design requirements.
Impact of Tg on PCB performance
1.Stability and Reliability
The higher the Tg value, the better the stability and reliability of the finished PCB under high temperature conditions usually is. Higher Tg PCBs are able to maintain their electrical and mechanical properties at higher operating temperatures, reducing the risk of temperature-induced changes in material properties and therefore performing more reliably in the long-term use of electronic products.
2.Heat resistance
Heat resistance is an important indicator of PCB performance. High Tg materials can work at higher ambient temperatures without damage, and can effectively prevent the failure of circuit components due to high temperature. Therefore, in applications that require high temperature operation, the use of high Tg PCBs can improve the heat resistance of the overall system.
3.Chemical Resistance
High Tg PCBs generally maintain their performance better after being immersed in a variety of chemicals.This means that high Tg materials provide better protection when used in environments that require high chemical resistance,such as in automotive electronics and industrial control applications.
4.Thermal Expansion and Thermal Management
The Tg value also affects the coefficient of thermal expansion (CTE) of the PCB.High Tg materials typically have a low coefficient of thermal expansion, which helps to reduce the mechanical stress caused by temperature changes.This characteristic is critical to ensure long-term PCB operation in high-temperature environments and to prevent solder joint failure.
5.Design Freedom
High Tg PCBs are able to withstand more complex designs, especially in multilayer boards and microvia engineering. Due to its excellent thermal performance and reliability, designers can use higher integration and more compact design solutions in PCB layout to meet the demand for thin, light and high performance in modern electronic devices.
Factors to consider when selecting PCB materials to determine the applicability of Tg values.
- Operating temperature requirements
First, determine the operating environment of the PCB and its maximum operating temperature.On this basis, the Tg value should be higher than the expected operating temperature to ensure that the mechanical and electrical properties of the material will not be damaged at that temperature. If the Tg value is lower than the operating temperature, it may lead to material softening, deformation, or even affect the circuit function. - Temperature conditions of the manufacturing process
In the PCB manufacturing process, different soldering processes will involve different temperatures. For example, the traditional leaded soldering process temperature is often between 210 and 245°C, while the lead-free soldering is usually between 220 and 260°C. The temperature of the soldering process can vary depending on the type of material used.Therefore, the Tg value of the selected PCB material needs to take into account these process temperatures to prevent material damage or performance degradation during processing. - Application-specific requirements
The requirements for Tg values vary from application to application. Automotive electronics, aerospace and medical equipment, such as high temperature, high reliability requirements of the application, usually need to use high Tg value of the material to ensure that the equipment can work properly in extreme environments. For consumer electronics, although the Tg requirements may be lower, but still need to ensure basic durability. - Influence of Material Properties
The Tg value is affected by the material matrix.Different resin matrices (e.g. epoxy, polyimide, etc.) have different thermal stability properties. For example, the Tg value of polyimide is usually higher than that of general epoxy resin, which is suitable for more severe working environment.When selecting materials, it is necessary to choose the right matrix based on the needs to optimize the performance. - Balancing cost and performance
High Tg materials are usually more costly, so the balance between cost and performance needs to be considered when selecting.Projects with high requirements for specific properties may require investment in high Tg materials.Whereas for certain applications with low performance requirements, suitable medium or low Tg materials can be selected to reduce costs.
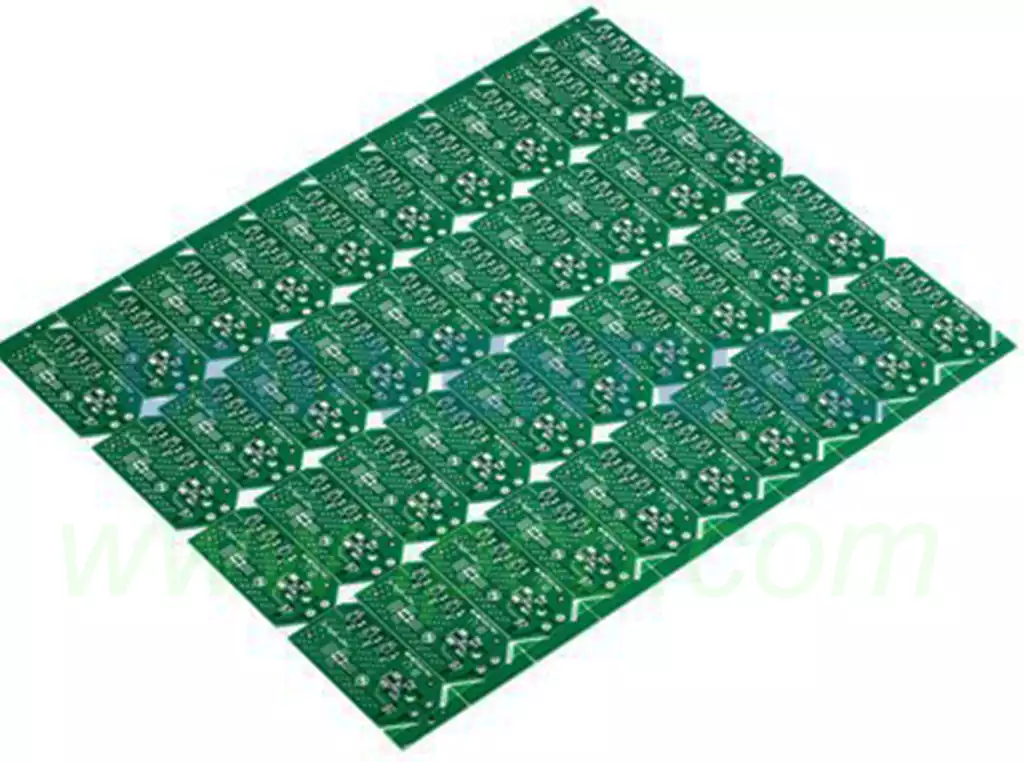
Cost control is an important consideration when selecting high Tg materials. Strategies to effectively avoid high cost:
- Define the needs
Before selecting High Tg materials,you first need to clarify the specific needs of the product, including operating temperature,environmental conditions and performance requirements.Through an in-depth assessment of the actual needs of the project, to avoid the selection of high Tg materials beyond the necessary standards, thereby effectively reducing costs. - Compare different materials
A variety of high Tg materials exist on the market with different properties and prices.For example,polyimide,BT epoxy resin and FR-4 high Tg materials,etc., each with different prices and properties. Manufacturers should carefully compare the performance and cost of different materials and select the one that best meets their needs in order to control costs while satisfying performance. - Adoption of appropriate manufacturing process
The manufacturing process has a direct impact on cost.When selecting materials,the processing technology that matches the specific high Tg material should be considered so as to improve production efficiency and reduce production loss.For example,optimizing the lamination process and drilling techniques can significantly improve yields and reduce failure rates, thereby lowering overall costs. - Bulk Sourcing and Long-Term Cooperation
Material procurement costs can be effectively reduced by purchasing high Tg materials in bulk or establishing long-term partnerships with suppliers. Suppliers often offer discounts based on order quantities,thus reducing overall costs. In addition,long-term cooperation also helps to ensure the consistency of material quality and stability of supply. - Optimized Design
Reasonable board design can reduce the use of high Tg materials and lower costs. For example, the use of simplified design and rational arrangement of components can reduce material requirements and processing complexity. Good design can not only improve product performance, but also effectively control production costs. - Find alternative materials
In some cases, the use of medium Tg materials can be considered instead of high Tg materials, especially when the working conditions of the product do not require excessively high temperatures. By scientifically evaluating the balance between economy and performance, alternative materials may be able to meet the performance while effectively reducing costs.
The pcb glass transition temperature (Tg) plays a pivotal role in the PCB design and manufacturing process.A reasonable choice of Tg value not only directly affects the stability, heat resistance, chemical resistance and thermal management capability of the PCB,but also determines its reliability and performance in specific applications. In the face of increasing market requirements and technical challenges, designers need to take into account the operating temperature, manufacturing process, application areas and material properties when selecting PCB materials to ensure that products can perform well under extreme conditions.