FPC flexible circuit board is widely used in modern electronic products due to their thin, lightweight and bendable characteristics. However, its unique physical properties also bring many challenges to the welding process, requiring fine process control and specialised coping strategies.
Flexible circuit boards in the welding process should pay attention to:
- Temperature control:flexible circuit board welding temperature is generally low, usually below 200 ℃. Too high temperature may damage the circuit board, so please make sure to control the welding temperature.
- Welding time: When welding flexible circuit boards, the welding time should be shortened as much as possible to reduce the thermal impact on the circuit board. At the same time, pay attention to avoid welding time is too short, resulting in weak solder joints.
- Welding position: When welding flex board, you should choose a suitable welding position to avoid welding to the circuit board important components or signal lines.
- Pre-welding processing
Before welding, the circuit board needs to be fully cleaned and processed to keep the surface dry and clean and avoid the interference of impurities such as oil and moisture. At the same time, before welding needs to be based on the materials used and the process of selecting the appropriate acid and alkali cleaning agents, solvents, etc., in order to ensure that the surface of the circuit board after welding without residual substances and oxidation layer.
Quality inspection is a key part of the soldering work. After the soldering is completed, you should carefully check the quality of the soldered joints and perform the necessary tests. If you find problems with the soldering points, you should repair or re-solder them in time to ensure the normal operation of the circuit board.
In terms of layout, when the size of the circuit board is too large, although the welding is easier to control, but the printed lines are long, the impedance increases, the anti-noise ability decreases, and the cost increases; when it is too small, the heat dissipation decreases, the welding is not easy to control, and it is easy for neighbouring lines to interfere with each other, such as the electromagnetic interference of the circuit board. Therefore, the PCB board design must be optimised:
(1) shorten the connection between high-frequency components, reduce EMI interference.
(2) Large weight (such as more than 20g) components, should be fixed with brackets, and then welded.
(3) Heat-generating components should be considered to dissipate heat, to prevent the component surface has a large ΔT defects and rework, heat-sensitive components should be far from the heat source.
(4) The arrangement of components as parallel as possible, so that not only beautiful and easy to solder, suitable for mass production. Circuit board design for the 4:3 rectangular (good). Do not change the width of the wire to avoid discontinuity in the wiring. When the board is subjected to heat for a long time, the copper foil is susceptible to expansion and peeling off, therefore, the use of large areas of copper foil should be avoided.
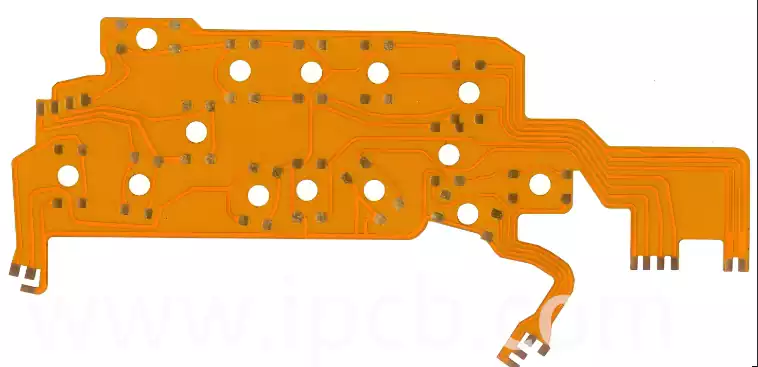
Countermeasures of soldering machine in flexible circuit board (FPC) soldering
Countermeasures for FPC material characteristics
Adopt special fixtures: Design and use special fixtures for flex board, fix FPC on the fixtures to reduce its deformation in the soldering process. The fixture can adopt vacuum adsorption, mechanical clamping and other methods to ensure that the FPC remains flat and stable during the welding process. For example, for some shaped FPC, the fixture can be customised to improve the stability of welding.
Optimise the heating method: adopt local heating or low temperature welding technology to reduce the thermal impact on the whole FPC. For example, the use of laser welding or infrared welding and other local heating methods, only on the welding point part of the heating, to reduce the heat conduction to other parts of the FPC. At the same time, choose better heat-resistant FPC materials or surface treatment of flexible circuit board to improve its heat resistance.
Countermeasures for high fineness of pads and lines
High-precision positioning system: Equipped with a high-precision vision positioning system, the camera accurately identifies and positions the pads on the flexible circuit board to ensure that the solder head can be accurately aligned with the pads. The precision of the vision positioning system should reach the micron level to meet the demand for high-precision soldering of FPCs. For example, high resolution industrial cameras and advanced image processing algorithms are used to improve positioning accuracy and stability.
Optimise welding parameters: Optimise welding pressure, welding speed and other parameters according to the size and material of the pads and lines. Through experimentation and debugging, we find the best combination of welding parameters to avoid damage to the lines. For example, for fine lines, the welding pressure and welding speed can be appropriately reduced to reduce the impact on the line.
Countermeasures to solve the complexity of welding process control
Intelligent temperature control system: adopt intelligent temperature control system to monitor and adjust the welding temperature in real time. The system can automatically adjust the heating power according to different flexible circuit board materials, solder paste types and soldering stages to ensure that the soldering temperature is always kept within the appropriate range. For example, some advanced soldering machines are equipped with temperature sensors and feedback control systems that can accurately control the soldering temperature, and the fluctuation range can be controlled within ±2.
Flexible circuit board soldering is a complex and sophisticated process. In the future, with the continuous development of FPC materials and welding technology, the welding of flex board will be more efficient and precise, providing strong support for the innovation of various electronic products.