Wire bonding is a method of connecting metal leads to pads, i.e., it is a technique for connecting internal and external chips. Structurally, the metal leads act as a bridge between the chip’s pads (primary bonding) and the carrier pads (secondary bonding). In the early days, lead frames (lead frame) were used as the carrier substrate, but with the ever-changing technology, PCBs/DBCs are increasingly used as the substrate. Connected to two separate pads of the wire bonding, the lead material, bonding conditions, bonding position (in addition to connecting the chip and the substrate, but also connected to the two chips, or two substrates) and so on are very different.
Material selection for metal wire bonding: The selection of metal materials such as gold (Au), aluminium (Al), copper (Cu), etc. is based on a comprehensive consideration of various soldering parameters with the aim of finding the most suitable combination method. These parameters cover a wide range, including, but not limited to, semiconductor product type, package type, pad size, metal lead diameter, soldering technology, as well as the tensile strength and elongation of the metal lead. Among the many metal lead materials, gold (Au), aluminium (Al) and copper (Cu) are typical.
Gold wires are favoured in semiconductor packaging due to their excellent electrical conductivity, chemical stability and strong corrosion resistance. In contrast, the aluminium wires used in the early days had significant defects that made them susceptible to corrosion. In addition, the high hardness of gold wires enables the smooth formation of spheres in primary bonding and the perfect presentation of semicircular lead loops (Loop, i.e., the shape of gold wires in the primary bonding to secondary bonding process) in secondary bonding.
Aluminium wires have a larger diameter and a wider pitch than gold wires.As a result,even if the use of high-purity gold wire to form a lead loop is not easy to break, but pure aluminium wire is fragile, so often mixed with other elements such as silicon or magnesium to make alloys to enhance its toughness. Aluminium wire is mainly used in high-temperature packaging or can not use gold wire occasions,such as ultrasonic method.
Copper wire, although the price is friendly,but the hardness is too high,it is not easy to form a ball, and in the formation of the lead ring is more restricted. In addition, in the ball bonding process,if the pressure is applied to the chip pad,the high hardness of the copper wire may lead to cracks in the film at the bottom of the pad, or even cause the pad layer to fall off the ‘peeling’ phenomenon.However,the use of copper wire is increasing, as the metal wiring of chips is mainly made of copper. To overcome the shortcomings of copper wire, small amounts of other materials are often added to make alloys.
Core components of wire bonding
Lead material: As the core material for bonding, it is usually made of gold due to its excellent electrical conductivity, corrosion resistance and good adhesion.
Connection area (pad): A special part of the chip or package surface that is dedicated to making a connection with the wires.
Bonding device: A specialised mechanical device that uses ultrasonic energy, heat and pressure to achieve a bonding effect.
Typical steps
Lead wire supply: The wire passes through the capillary tube via the bobbin.
Ball jointing: The wire is cut and shaped into a ball at one end by means of ultrasonic energy and heat.
Wedge crimping: Using a wedge-shaped device, the other end of the wire is flattened and firmly attached to the pads on the package.
Influencing factors
Wire material: The choice of wire material has a direct impact on its electrical conductivity, mechanical strength and bonding characteristics.
Bonding conditions: In the bonding process, ultrasonic energy, temperature, and applied pressure and other parameters will have an important impact on the bonding quality.
Package construction: The overall design of the package, especially the arrangement of the pads and the degree of surface smoothness, will have a certain impact on the bonding process.
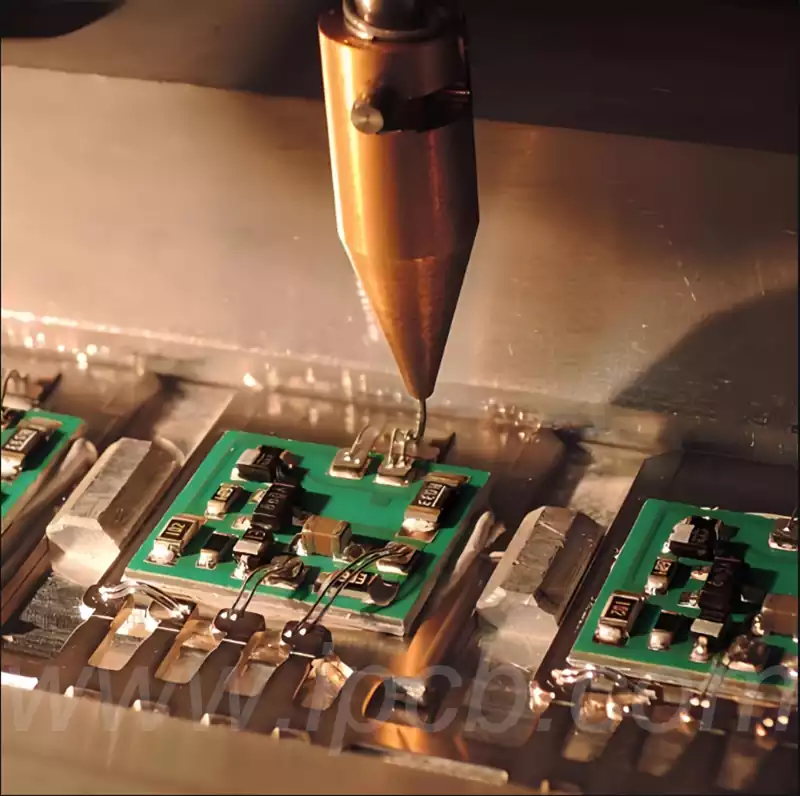
There are three main technical ways to connect metal leads to pads:
(1) Thermo-compression bonding, which uses a capillary cleaver (a tool shaped like a capillary tube used to move metal leads) to connect to the pad through heating and compression. Specifically, the hot compression bonding method will first preheat the chip pad to about 200 ℃, and then raise the temperature of the tip of the capillary cleaver to the formation of a sphere, and then with the help of the cleaver to the pad to apply pressure, so as to complete the connection between the metal lead and the pad.
(2) Ultrasonic bonding technology (Ultrasonic bonding), the technology does not require heating, but rather by applying ultrasonic waves to the capillary cleaver (a tool similar to the capillary cleaver, used to move the metal lead but does not form a ball, called a wedge cleaver) to achieve the connection. This method has the advantage of low process and material costs; however, the bonding tensile strength (i.e., the amount of tensile force that the leads can withstand after joining) is relatively weak due to the replacement of the heating and pressurisation process with easy-to-operate ultrasound.
(3) Thermosonic bonding, which is an integrated method combining heating and ultrasonic waves, is currently the most commonly used bonding technology. The technique is performed by simultaneously applying heat, pressure and ultrasound to the capillary cleaver to complete the connection under optimal conditions. In semiconductor back-end processes, given that bond strength is more important than cost, gold wire thermal ultrasonic bonding is the most commonly used bonding method, despite the higher cost of the thermal ultrasonic bonding technology.
Future trends in wire bonding technology
A notable trend in wire bonding technology is the move towards miniaturisation and high density connections. As electronic devices move towards greater portability and compactness, there is an increasing demand for miniaturisation and high performance. This trend makes the development of fine-pitch wire bonding technology increasingly important, and manufacturers are working to develop even finer leads to meet the demanding size and performance requirements of future semiconductor products.
Another important trend is the change in material selection. The use of copper wire is gradually increasing, as its higher electrical and thermal conductivity makes it an alternative choice for wire bonding, gradually replacing the traditional aluminium and gold wires. This material shift not only reduces costs, but also improves the reliability of the connection, thus driving the popularity of wire bonding technology in high-performance applications.
As a key technology for connecting internal and external chips, wire bonding technology plays a vital role in semiconductor packaging. With the miniaturisation of electronic devices and the increased demand for high-density connections, lead bonding technology is developing in the direction of greater refinement, efficiency and reliability. In the future, with the continuous advancement of technology and further cost reduction, lead bonding technology is expected to be widely used in more fields, injecting new vitality into the development of the semiconductor industry. At the same time, we also look forward to the emergence of more innovative technologies to jointly promote the wire bonding technology to a new level.