High current pcb connector is an electrical connector that can be connected and disconnected under high current and high voltage conditions, and is mainly used for connecting high power supplies and loads that can transmit currents of tens to thousands of amperes. Its features include the ability to withstand high currents, high temperatures and high voltages, as well as being corrosion-proof, explosion-proof, vibration-resistant, water-proof, dust-proof, and heat-resistant.
Features of high current PCB connector
The high current PCB connector is characterised by high carrying capacity, high temperature resistance and corrosion resistance. It is usually made of high-quality conductive materials and can withstand high power current transmission to ensure the normal operation of electrical equipment.
High current PCB connector also has good waterproof and dustproof performance, can work properly in harsh environments. Its structure is reasonably designed to effectively prevent electrical equipment from being affected by the external environment.
High current PCB connector also has good seismic performance and durability, can be in the complex working environment of long-term stable operation.
Common High Current PCB Connector
Solder Pin Blade Connectors
Solder pin tab connector is a common type of PCB high current connector. It is characterised by being connected to the PCB board by welding, with solid connection and excellent conductivity. In high-current application scenarios such as electric vehicle charging piles and inverters, solder pin chip connectors are widely favoured for their reliable connection performance.
This type of connector is known as Faston among foreigners, signifying its fast turn-on feature. Common sizes include 2805, 4808 and 6308, and these numbers actually represent the width and thickness of the tabs. For example, the 6308 specification has an insert with a width of 6.3 mm and a thickness of 0.8 mm.
Spring-loaded connectors
The spring-loaded connector is another commonly used high current pcb connector. It is unique in that it uses spring force to make the connection, eliminating the need for soldering and allowing for a quick and easy connection to the PCB. Additionally, spring-loaded connectors offer excellent conductivity and durability to meet the demanding requirements of high-current applications.
Crimp Connectors
Crimp connectors are connectors that are crimped to the PCB. The advantage is that the connection process is simple and fast, and at the same time has good conductivity and stability. In high current applications such as electric vehicle charging piles and inverters, crimp connectors are highly regarded for their efficient and reliable connection.
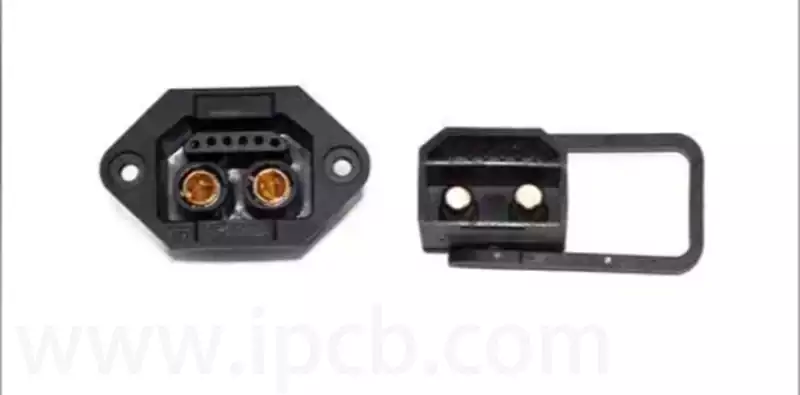
Common materials for high current pcb connector
- Metal materials
Copper alloy: copper alloy is the most important material for high current connector terminals and is widely used due to its excellent electrical conductivity and mechanical properties. Common copper alloys include phosphorus copper, beryllium copper, and Corson copper alloy.
Plating materials: In order to enhance corrosion resistance and stable contact performance, connector pins are usually coated with tin, tin-lead alloy, gold, silver and even brass and other materials. Special coatings such as ENIG/ENEPIG containing nickel or palladium are also widely used.
Spring material: the spring terminal in the connector is usually made of high heat-resistant copper alloy material that is not easy to be annealed, such as beryllium copper, so that the contact pressure and elasticity can be maintained under high temperature environment.
- Plastic materials
Heat-resistant engineering plastics: high-current connector shell and insulation parts are mostly used in heat-resistant materials, such as PBT (polybutylene terephthalate), LCP (liquid crystal polymers), PPS (polyphenylene sulfide), nylon (PA), etc., these materials have good mechanical strength and heat-resistant, suitable for withstanding heat generated by high current.
Flame resistance requirements: the material must meet the UL 94 V-0 level of flame retardant standards to ensure the safety of the connector at high temperatures or under abnormal conditions.
High current pcb connector is widely used mainly include the following points:
- New energy vehicles: for high-voltage high-current connection of battery packs, motors, and charging systems to support fast charging and high energy transfer.
- Industrial equipment: provide stable high current interface for heavy machinery, inverter, power distribution system, adapt to high load operation.
- Renewable energy: connecting photovoltaic inverters, wind turbines and energy storage systems to achieve efficient energy conversion and transmission.
- Railway transport: applied to the traction power supply and auxiliary system of high-speed railway and underground to meet the demand of high reliability.
- Aerospace and military industry: to ensure the stable connection of high-power equipment in extreme environments, such as airborne power supply and radar system.
With the continuous progress of technology and the demand for high-performance electrical connections in various industries, high current PCB connector plays an increasingly important role as key core components. In the future, with the continuous innovation of material science and manufacturing process, high-current PCB connectors will continue to improve the performance and reliability, help high-power electronic equipment to achieve more efficient and safer operation, and promote the industry to the intelligent and green direction.