Millimeter-wave radar connector is specialized connectors for millimeter wave radar systems that provide low loss and high reliability in high-frequency signal transmission.They are widely used in automotive,driverless,and industrial automation applications to support access to all types of advanced sensors.These connectors are designed to withstand high-frequency signals and ensure the stability and effectiveness of signal transmission,avoiding signal attenuation and distortion.
Millimeter-wave radar connector needs to meet a series of stringent technical parameters to ensure reliability and effectiveness in high-frequency environments.These technical requirements include current rating,voltage rating,contact resistance,and temperature adaptation.For example,many millimeter-wave radar connectors are rated at 100V AC/DC and have a temperature range from -40°C to +125°C.The contact resistance is usually initialized at 100V AC/DC. In addition,the initial value of contact resistance usually needs to be maintained at ≤1mΩ,and after environmental testing shall not exceed 30mΩ, such requirements to ensure the stability of signal transmission.
Factors to consider when selecting a millimeter wave radar connector:
- Frequency Response
Frequency response is the primary consideration in the selection of millimeter wave radar connectors.Millimeter wave radars typically operate in higher frequency bands (e.g., 24 GHz, 77 GHz, and 60 GHz),so the selected connector must have good transmission characteristics at these frequencies to ensure signal integrity and overall system performance.Therefore,the bandwidth of the connector should cover the radar’s operating range to minimize signal loss and distortion. - Plugging and unplugging times
Plugging and unplugging times are important indicators of connector durability.For millimeter wave radar systems that require frequent maintenance or replacement, it is particularly important to select connectors with a high number of plugs and unplugs. This ensures that the connector can still maintain good performance in long-term use, to avoid signal interruption caused by poor contact. - Material selection
Connector material is directly related to its mechanical and electrical properties.Usually,the connector shell material needs to have good electrical conductivity and corrosion resistance, often choose metal materials (such as stainless steel or aluminum alloy) to enhance its durability. In addition,the insulation material should have excellent dielectric properties to reduce signal interference and loss. - Size and spacing
When selecting connectors, you need to consider its size and spacing with other components. Millimeter-wave radar devices usually have high space requirements, and choosing compact and low-profile connectors can effectively save space and simplify the overall design. In addition,a reasonable insertion spacing helps avoid problems such as signal coupling and reflection. - Environmental adaptability
Millimeter wave radar connectors should be able to adapt to the complex and variable operating environment,including high temperature, low temperature, humidity and vibration and other factors.Therefore,selecting connectors that meet the relevant protection level (e.g. IP67) can effectively enhance their reliability in various environments and ensure stable system operation. - Price and supply chain
Finally, price and supply chain availability are also important factors to consider when choosing millimeter wave radar connectors.Connectors should be selected reasonably according to the project budget, and to ensure that they have sufficient supply in the market for maintenance and replacement in the later stage. This helps reduce the overall project cost and risk.
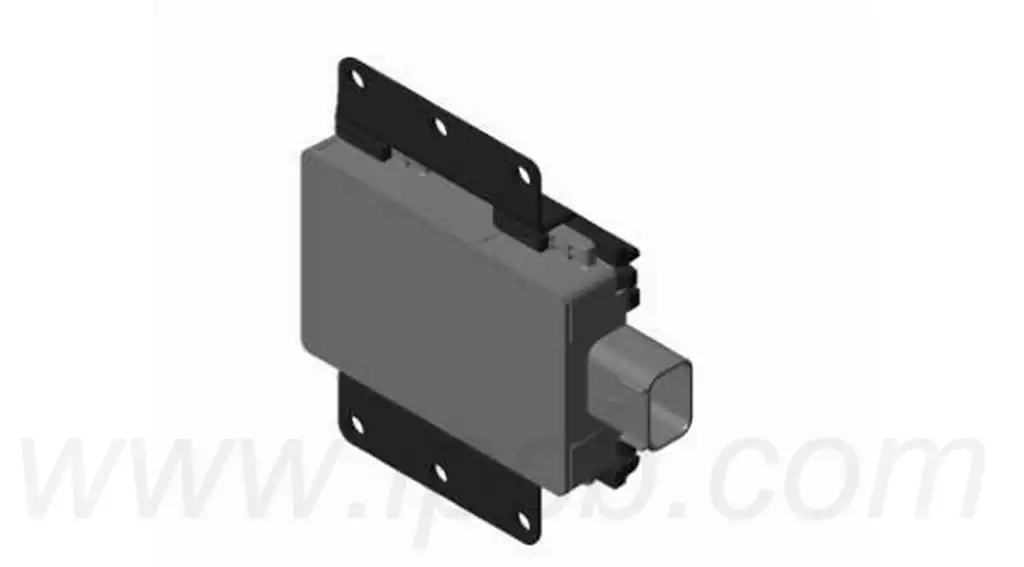
The role of millimeter wave connectors
1.Millimeter wave signal transmission
The basic function of millimeter wave radar connectors is to transmit millimeter wave signals.These connectors are mainly used for applications with frequencies greater than 30GHz,with high frequency and high bandwidth characteristics,to meet the stringent requirements for data transmission rate and signal quality.
- Support high frequency applications
Millimeter wave connectors are widely used in high-frequency devices due to their excellent performance.This includes wireless communications,RFID,radar and satellite communications,ensuring efficient and reliable signal transmission in the millimeter-wave frequency band (30GHz to 300GHz). - Meets the need for miniaturization
Thanks to their miniaturized design,millimeter wave radar connector is ideally suited for space-constrained environments. They not only have advantages in size, but also work stably at multiple orders of magnitude of frequency,adapting to the needs of different devices. - Improved connection accuracy
Millimeter wave connectors have strict requirements for the connector plug and socket interface design.This high-precision design can effectively reduce signal reflection and loss, and improve the quality of signal transmission.
Millimeter wave radar connectors affect the quality of the signal and transmission speed:
- Insertion loss and signal transmission
Insertion loss is the loss of signal strength as it passes through the connector. Millimeter wave connectors need to be designed to minimize insertion loss to ensure that signals can be transmitted efficiently. Ideally, insertion loss should be as low as possible to optimize the quality and speed of signal transmission. High-quality connectors can be guaranteed to transmit efficiently by increasing signal strength. - Impact of reflection loss on signal quality
Reflection loss is caused by poor contact or improper design of connectors, which negatively affects the signal quality. Reflected signals not only lead to reduced signal strength, but also may cause interference and distortion, thus affecting system performance. In millimeter-wave communications, due to the high frequency and short wavelength of the signal, the impact of reflection loss is particularly obvious. - Crosstalk and electrical performance
Crosstalk is the unwanted interference caused by coupling during signal transmission.This is a millimeter wave connector design factors need to be considered, because the increase in crosstalk will lead to a decline in signal quality,thereby affecting the speed and accuracy of data transmission. Good connector design can effectively reduce crosstalk, and ensure that the signal is clear and stable transmission. - Connector materials and structure
Choosing the right material and optimizing the structural design are also important factors affecting signal quality and transmission speed. Millimeter wave connectors usually use metal materials, such as stainless steel or copper alloy,to provide excellent transmission performance and mechanical strength. The use of these materials not only improves the stability and high temperature resistance of the connector, but also maintains good signal transmission quality in a variety of harsh environmental conditions. - Low and high temperature environment performance
The performance of millimeter wave connectors in different temperature environments also has an impact on the quality of signal transmission. In low or high temperature environments, the insulation resistance and contact resistance of the connector may change, thus affecting the stability of the signal. When designing a connector, it is necessary to ensure that it maintains excellent performance over a wide range of temperatures to ensure efficient and reliable signal transmission.
Millimeter wave radar connector plays an indispensable role in modern high-frequency applications. Their design and selection not only involves the low-loss transmission of high-frequency signals, but also covers the multiple requirements of adapting to complex environments, ensuring connection stability and signal quality. By focusing on frequency response, plugging and unplugging times, material selection, size and spacing, environmental adaptability, as well as price and supply chain factors, designers and engineers are able to optimize system performance and improve the overall reliability of radar equipment.