In the fierce competition in the electronics manufacturing industry, effective control of PCBA (Printed Circuit Board Assembly) processing costs is the key to enhancing the competitiveness of enterprises. From board design to component sourcing, to placement and assembly testing, every step of the process holds the potential for cost optimization.
In order to minimize PCBA processing manufacturing expenses, the following key factors need to be taken into account:
- Board size is undoubtedly a key link, size reduction is directly related to cost reduction. It is worth noting that some of the PCB size has been standardized, the use of standard-sized circuit boards can enjoy the lowest cost.
- Compared to plug-in technology, the use of SMT (surface mount technology) is more economical, because it can accommodate more components on the board.
- In addition, if the layout of the components on the PCB is compact, then the wiring needs to be more delicate and the required equipment needs to be of a higher level. At the same time, the PCB material requirements are also higher, the wire design needs to be more careful to prevent power consumption or affect the performance of the circuit and other issues. These issues bring additional costs, may exceed the cost savings of reducing the size of the PCB.
- The more layers a PCB has, the higher the cost. However, PCBs with fewer layers often result in larger sizes.
- Drilling is time-consuming, so the fewer the number of vias on the PCB, the better.
- Blind vias are more costly than through holes because they need to be pre-drilled before lamination.
- The diameter of the vias is determined by the diameter of the component pins. If there are components with different pin diameters on the board, it will take more time and increase the manufacturing cost because the machine cannot drill all the holes with the same drill.
- Electronic testing using flying probe is usually more expensive than optical testing. Generally speaking, optical testing is sufficient to ensure that the PCB is error-free. Optical testing can more easily detect improper clearance between conductors.
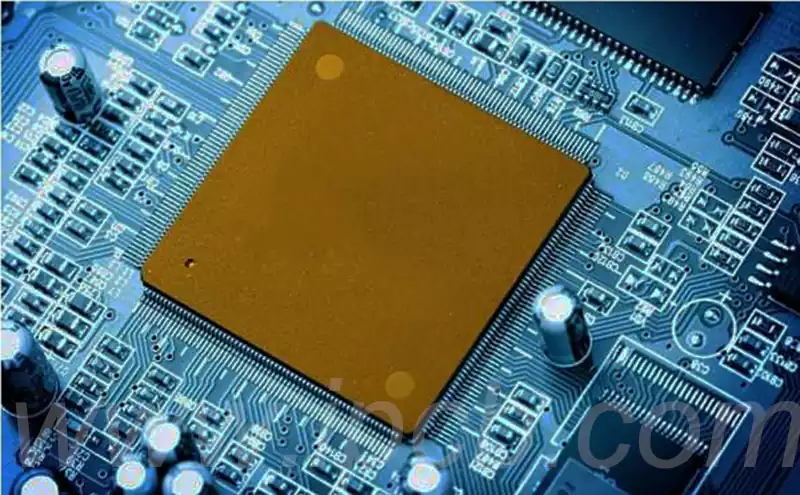
Factors to consider for PCBA costing:
- When customers are faced with the need for small quantities, it is wise to tend to choose a professional manufacturer that focuses on PCBA proofing. As the old saying goes: “Seek knowledge sooner or later, skills have expertise.” Each manufacturer has its own specific market positioning and production processes in which it specializes. For the case of small demand, prefer those specializing in PCBA prototyping factory is more appropriate, because they can usually provide fast, efficient service, and competitive price. Especially those who provide one-stop PCBA chip processing services manufacturers, can bring great convenience to customers, both to save time and reduce costs!
- In the component procurement decisions, need to distinguish between two different situations: one is for the delivery of tight, urgent need to verify the feasibility of the program sampling production, at this time should be the main spot with a single, to ensure that the rapid set of materials needed to promote production. Although the spot can quickly meet the demand, but some of its price may be relatively high. On the other hand, for mature and has entered the mass production stage of the project, if the delivery time is not strict requirements, it is more appropriate to choose futures suppliers, because futures bulk purchases usually enjoy lower prices.
Before formal procurement, in-depth communication with the PCBA manufacturer is crucial, to clarify its procurement channels are focused on spot or futures. In addition, it is also critical to have a wealth of channel resources, which allows us to make multiple comparisons to find the most cost-effective option. But the core is that these channels must be able to ensure that the BOM (bill of materials) is a complete match to meet the production requirements.
- Selecting the manufacturing process for the PCB light board is critical. The current market mainstream FR-4 immersion gold and gold-plated boards in the price difference. If the process is not particularly stringent requirements, it is recommended that the material tends to choose conventional materials, such as aluminum substrates, copper substrates and Rogers high-frequency boards and other special boards need to be carefully considered, because they not only need to be booked in advance, but also accompanied by higher process requirements and costs. In addition, the cost of PCBs is also affected by a number of factors such as board brand, size, quantity, number of layers and thickness.
- In the SMT SMD manufacturing process, the diversity of material types plays a crucial role. The more types of materials, according to the patch soldering point to calculate the charge will naturally increase accordingly. If the number of plug-ins is large, it is necessary to produce wave soldering fixtures to complete the plug-in operation. In addition, some special processes, such as pre-production or post-production program burning, coating three-proof paint (including the production of fixtures), white glue, and labeling, etc., will increase the corresponding additional costs. As for the choice of patch stencils, the cost of stepped stencils is naturally higher compared to ordinary stencils. Therefore, in the absence of special requirements on the thickness of the solder, the choice of ordinary stencil will be more economical.
- Does the assembly and testing process incur additional costs? This step is billed separately by some manufacturers, while others have included it in the processing cost. Therefore, when signing a contract with a manufacturer, customers should make sure to clarify whether the testing costs are calculated separately. In this way, customers will be able to control costs to a certain extent and avoid unnecessary expenses.
Optimization of PCBA processing costs is a systematic project, by accurately grasping the cost drivers of each link, to take targeted optimization measures, enterprises are not only able to achieve effective cost control, but also improve production efficiency and product quality, so as to stand out in the fierce competition in the market!