PCB prepreg refers to the resin matrix in a certain way impregnated with reinforcing fibers, the formation of a uniform thickness of the strip or sheet-like semi-finished products, is a composite material from the raw material to the products of the transition of the intermediate products. It contains matrix resin and reinforcing fiber.
Prepreg can be divided into unidirectional prepreg, unidirectional textile prepreg,textile prepreg according to the physical state; according to the width can be divided into wide and narrow tape (a few millimeters to dozens of millimeters) prepreg,and according to the resin matrix can be divided into thermosetting resin prepreg and thermoplastic resin prepreg; according to the reinforcing material can be divided into different prepreg,glass fiber prepreg,aramid prepreg; according to the different lengths of the fibers can be divided into short fiber prepreg,long fiber prepreg,long fiber prepreg and long fiber prepreg.According to the different fiber length can be divided into short fiber prepreg, long fiber prepreg and continuous fiber prepreg.
Prepreg step by step
- Pre-treatment
Pretreatment is the first step in prepreg production,mainly including substrate cutting,surface pretreatment and filling treatment.Substrate cutting needs to be cut in size and shape according to the product requirements,and cleaned and dusted to ensure that the surface of the substrate is clean and can be better integrated with the resin. Surface pre-treatment mainly involves cleaning and activating the surface of the substrate with solvents or physical methods to improve the surface energy and fusion of the substrate.Filling treatment is to add fillers to the surface of the pcb substrate,both to increase its strength and to improve the performance of flame retardant and so on.
2.Mixing
Mixing is one of the key steps in the production of prepregs and involves processes such as material proportioning and stirring.The proportion of resin and hardener needs to be measured accurately according to the requirements of the product,and there should be no error. Homogeneity and sufficiency need to be ensured during the mixing process, which can improve the resin permeability and the performance of the substrate. Some special requirements of the prepreg also need to add fillers, catalysts and other auxiliary materials.
- Dip coating
Dip coating is the process of coating the mixed resin on the surface of the substrate,and it is necessary to ensure that the whole surface is evenly covered. In the coating process need to pay attention to control the depth of resin penetration and avoid bubbles,voids and other defects. Some high-grade prepregs also need to be vacuum dipped to improve performance. - Baking
Baking is the last process of prepreg production,mainly in the constant temperature oven will be cured prepreg heating,so that the resin is fully hardened to form a hard profile. In the baking process,it is necessary to ensure that the temperature,time and other parameters are strictly controlled to avoid excessive temperature or time leading to pyrolysis and other undesirable phenomena. - Quality control
Quality inspection is the last step in the production of prepreg,which is mainly to test the appearance,size,performance and other aspects of the finished product to ensure that the product meets the requirements.If any quality problems are found,they need to be dealt with in a timely manner so as not to affect the quality of the finished product and the use of the effect.
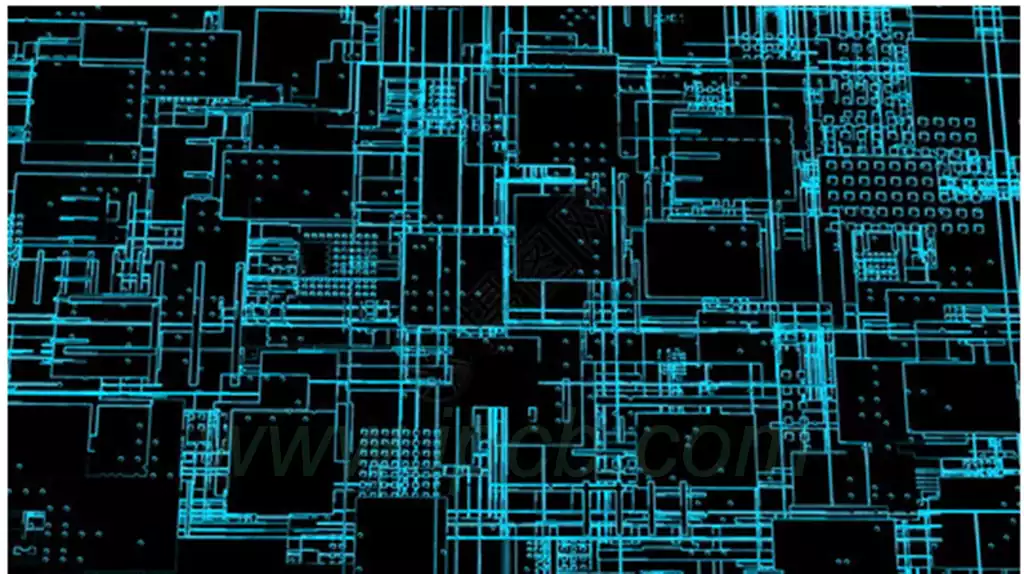
Features of prepreg:
- High adaptability: prepregs can be used to manufacture composite materials of various shapes, including flat sheets, plates,profiles, complex curved surfaces and special shapes.This adaptability can greatly reduce production costs and improve production efficiency.
- High production efficiency:Since prepregs do not require on-site resin impregnation,they can save a lot of time and labor.This contributes to higher productivity and reduces labor and material waste through automated processes.
- Consistent performance:Since the resin is pre-impregnated in the pcb prepreg,problems such as operator error and leakage that may occur during the impregnation process can be avoided.This ensures consistent performance of the composite and avoids unnecessary quality problems.
- Environmentally friendly: Prepreg manufacturing processes do not produce harmful substances and are therefore more environmentally friendly than traditional composite manufacturing processes.
Prepregs are widely used in the manufacture of composite materials in aerospace, energy, automotive, electronics and other fields.In the field of aviation, prepregs are used to manufacture aircraft compartments,wings,rudder surfaces and other components, whose strength and stiffness are much higher than those of traditional materials.In the automotive field,prepregs are used to manufacture body shells, interior parts, etc.,which can improve the degree of lightweight and energy-saving performance of the car body.In the electronics field,prepregs are used to manufacture components such as pcb substrates and screens in cell phones, computers and other devices.
PCB Prepreg, as the core of composite material manufacturing, is leading the development trend of modern industry with its unique process and wide range of applications. Its high efficiency, stability and environmental protection have brought innovation and change to several industries, and the future is promising.