Traditionally, Through Hole Technology (THT) has been used to build most printed circuit boards (PCBs).However,in recent years,the use of surface mount technology (SMT) has become increasingly popular and is gradually replacing through-hole mount technology.
What is through-hole insertion technology?
Through-hole insertion technology inserts components with tails or leads into pre-drilled holes in the PCB. These components are through-hole components. The leads can then be soldered to pads or to pads on the bottom of the board, usually using a wave soldering process (or can be hand soldered).
A new advancement in the process is the change from normal drilled holes to plated through holes.The holes are coated with solder paste and the wires are passed through this paste.The entire PCB is then heated to reflow the solder paste,which is called through-hole reflow soldering.This advancement has allowed through hole and surface mount to work together to build circuit boards,as both types of components can be soldered in one process.
Through-hole insertion technology creates a strong mechanical bonding action and is therefore very reliable and a proven process. The number of variables that can cause soldering problems on through-hole insertion technology is less than on surface mount technology and is usually well researched and understood. However, the process can make bare boards more expensive due to the additional drilling and possible requirements of printing PCBs on both sides. Automatically laying out the components on the PCB board can also be more difficult because many through-board assemblies are loosely packaged or otherwise bulk packaged.
Advantages of through-hole assembly:
- Easier to prototype, through-hole components are easy to replace; therefore they are well suited for PCB prototyping and testing.
- High heat resistance, THT bonds are highly heat resistant; thus making them the first choice for aerospace and military products
- Better power handling, soldering through-hole assemblies creates a strong bond between the board and the assembly. As such, it is well suited for larger assemblies that are bound to be affected by
- Stronger Physical Connection, the leads of THT assemblies have a stronger physical endurance. They can withstand environmental stresses because they are soldered on the opposite side of the board (they pass through the board). Stronger Physical Connections Stronger physical connections, which is why THT is the preferred choice for stadium and billboard LED lights. It is also used in industrial equipment and machinery due to exposure to very harsh conditions.
Disadvantages.
Like any other manufacturing or assembly technique, through-hole PCB assembly has its drawbacks. These include: Longer production times – it takes a lot of time to drill the multiple holes that the leads are expected to pass through. Expensive – Increased production costs due to the difficult and time-consuming process of drilling holes Minimizing space on the board – Drilling holes on the surface of the board restricts the area in which signals can be routed for tracing. Additionally, by routing the leads through the board, only one side of it is available, making the THT PCB run slightly slower.
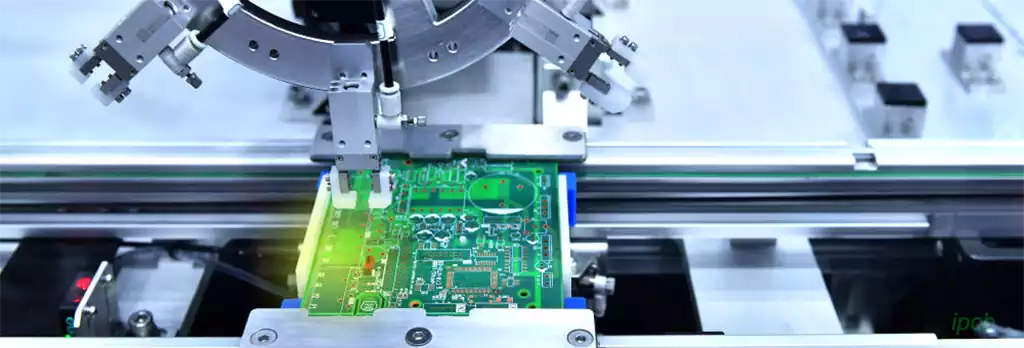
Surface mount technology is a method used to assemble electronic circuits by mounting or placing components directly on the top surface of a printed circuit board.
High assembly density, small size and light weight. smt uses chip components that are only a few tenths or even a few hundredths of the size of traditional cartridges, so higher assembly density can be realized, making electronic products lighter in size and weight.
High reliability and shock resistance. smt chip components used due to the small size and light weight, so can be more closely together, thus improving the reliability of the entire circuit board. In addition, the soldering material used in smt is tin-lead alloy, which has better shock resistance.
Low manufacturing cost and high production efficiency. smt uses automated production equipment that can realize high-speed, high-efficiency production, thus reducing manufacturing costs. At the same time, smt used components of small size, can save a lot of raw materials and energy, thus reducing the production cost.
Poor maintainability. smt used chip components once the failure, maintenance is more difficult, because these components are fixed in the circuit board by welding, maintenance requires the use of specialized equipment and tools to be replaced. smt has a wide range of applications, including communications, computers, consumer electronics, automotive electronics, industrial control and other fields. In these fields, smt plays an important role. For example, in the field of communications, smt can achieve smaller size and higher reliability; in the field of computers, smt can improve the performance and reliability of computers; in the field of consumer electronics, smt can improve the appearance and reliability of the product; in the field of automotive electronics, smt can improve the safety and reliability of the car; in the field of industrial control, smt can improve the reliability and stability of the device. In the field of industrial control, smt can improve the reliability and stability of equipment. smt’s future development trend mainly has the following aspects:
Toward smaller and finer direction. With the continuous development of electronic technology, the requirements of smt are getting higher and higher. The future smt will be smaller, more detailed direction, so as to achieve a smaller volume and higher assembly density.
Toward a more efficient, more intelligent direction. The future smt will be more efficient, more intelligent direction, through automation equipment and the application of artificial intelligence technology, to achieve higher speed, more efficient production.
Toward a more environmentally friendly, more sustainable direction. Future smt will develop in the direction of more environmentally friendly and sustainable development, through the use of environmentally friendly materials and the application of energy-saving technologies to achieve more environmentally friendly and sustainable production.
Through-hole and surface mount PCB assembly
Surface mount devices do not require holes to be drilled in the PCB because their leads do not pass through the board to the other end. Instead, these assemblies have surface mount packages. The leads are usually located around or under these packages. These leads are usually in direct contact with pads located on the surface of the board.
The main differences between through-hole and surface mount assemblies are:
- Drilling holes and soldering leads on the other side of the board means that only one side of the board can be used for THM.
- Components used in SMT are usually much smaller, allowing multiple components to be mounted on a relatively small board.
- In SMT, the board is able to accommodate a higher number of pins than THM; therefore, the board has a higher number of component leads than THM.
- The throughput of SMT can be very high.
- SMT requires higher capital investment in setting up machines and production processes than THM.
- The use of SMT requires a higher level of skills and technology than THMA. The need for more advanced technology also comes at a higher cost.
- Although SMT seems to have overwhelming advantages over it, the through-hole method is still mainly used for testing and prototyping applications.
As electronics technology continues to evolve, the future of SMT will be toward smaller, finer, more efficient, smarter, as well as more environmentally friendly and sustainable. Overall,through hole vs surface mount each have their own characteristics and applicable scenarios, and in practical applications, the appropriate PCB assembly technology should be selected according to specific needs and conditions.