What is beveler in pcb?The PCB beveling machine is a specialised equipment for chamfering the edges of circuit boards.Beveling of circuit boards refers to a special treatment on the edges or corners of circuit boards, which is usually done by cutting or grinding to make the edges that are originally straight or sharp rounded. This treatment not only changes the appearance of the circuit board, but more importantly, it plays a key role in enhancing the safety and reliability of the circuit board.
PCB beveling machine working principle and operation steps
Wafer loading:The robot removes the wafers to be processed from the storage location or from the previous process and places them accurately on the working table.
Parameter setting:The operator sets the processing parameters, such as chamfering depth, rotational speed, feed speed, etc., through the control cabinet.
Chamfering Processing:After starting the equipment, the chamfering head starts to rotate at high speed and grinds the wafer edge. The carbide tool contacts with the wafer edge and removes the sharp edges of the wafer edge by friction and cutting, making it smooth.
Quality monitoring:During the machining process, the equipment may be equipped with a quality monitoring system to monitor the machining quality in real time, such as surface roughness and chamfer shape.
Wafer unloading:After processing,the robot removes the processed wafers from the table and places them in a collection box or on a conveyor belt for the next process.
Application areas and importance of chamfering machines
Beveling machines play an important role in circuit board design and manufacturing. Their main functions include:
Increased safety:Reduces the risk of scratches or cuts caused by right-angled or sharp edges.
Enhanced durability:Reduces stress concentration at edges and improves the overall durability of the circuit board.
Enhanced aesthetics:rounded edges are not only visually more aesthetically pleasing, but also prevent dust and dirt from accumulating in the corners.
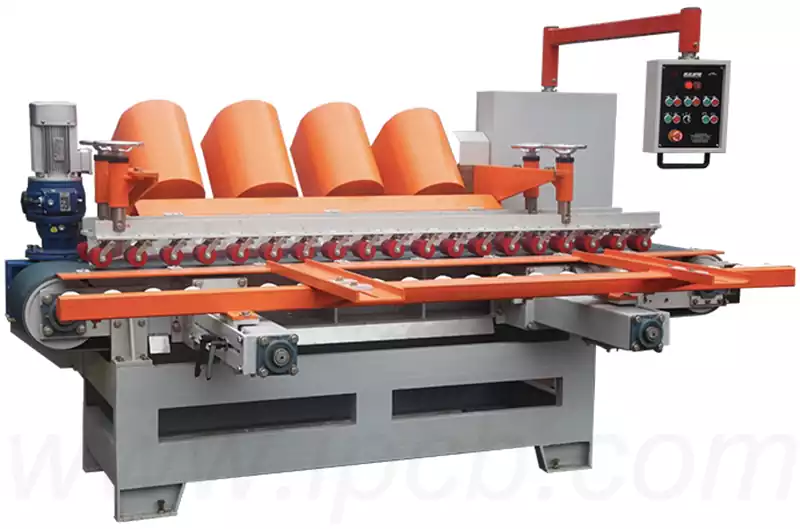
The implementation details of circuit board chamfering need to be based on the actual situation of the PCB board to determine. If the diameter of the through-hole is less than 0.6mm, the usual chamfer width of 0.2mm; when the diameter of the through-hole is more than 0.6mm, the chamfer width should not be less than 1mm as a regular practice. In addition, the thickness of the PCB board is also a factor in determining the through-hole chamfer width. The usual rule is that when the board thickness increases, the width of the chamfer should be increased accordingly.
The role of PCB beveling machine
- Protect the edge of the PCB board
Because the edge of the circuit board is relatively fragile, easy to be damaged by friction, so the chamfering process can play a protective role, so that the edge of the board is not easily damaged. - Improve service life
After chamfering the edge of the circuit board more smooth, if not chamfered, the edge may be sharp, it is easy to scratch your fingers, affecting the use of experience. And if the board edge is damaged during use, it may lead to a shorter life of the board. Chamfering avoids these problems and improves the life of the board.
Despite the advantages of chamfering, over-implementation can have a detrimental effect on the board. Specifically, if the chamfer is designed to be too wide, it will increase the diameter of the through-hole, which may result in an inappropriate amount of solder paste (too much or too little) on the board. In addition, chamfers that are not deep enough or are not uniform enough can reduce the life of the PCB and impair its performance.
PCB beveling technology is not only an indispensable part of the circuit board manufacturing process, but also a key factor in enhancing the safety, durability and aesthetics of circuit boards. With the continuous development of electronic technology, the application of circuit boards is becoming more and more extensive, the quality of circuit boards and performance requirements are also higher and higher. Therefore, the continuous optimisation of circuit board chamfering technology to improve processing accuracy and efficiency will become an important direction for the continuous development of the circuit board manufacturing industry.