What is pcb coating material?
PCB coating is a thin, polymer film (about 12-200 microns) applied to the populated board. It provides electrical insulation and protects the board from external components or the adverse conditions of the environment in which it is used. Harsh factors include (but are not limited to) the following:
- Chemicals
- Abrasives
- Temperature changes
- Moisture or high humidity
- Airborne contaminants such as fungus, dust and dirt
PCB protective film is also called “conformal coating”. This is because it takes on the contours of the circuit board and protects component leads, solder joints and electrical tracks from corrosion and other damage.
You can apply the film using a variety of methods: brushing, spraying, dipping or chemical vapor deposition (CVD). The application process may also involve automated industrial equipment for large batches of boards or manual methods for small coatings.
Benefits of Conformal Coating
Conformal coating ensures that your PCBs meet the needs of their application, making it an important part of circuit board production. It also enables the circuit board to meet specific industry standards. In short, these all provide benefits.
- Sense of responsibility – your board is protected from environmental hazards, improving reliability
- Performance benefits – it allows your pcb to operate at higher voltage gradients and improves its performance
- Space saving – the dielectric properties of pcb conformal films help reduce the space between traces, making smaller designs possible.
- Extended life – the right material prevents corrosion and other forms of damage, thus extending the life of the pcb
- Reduced cost – the protective nature of these films can save you the cost of bulky and expensive enclosures
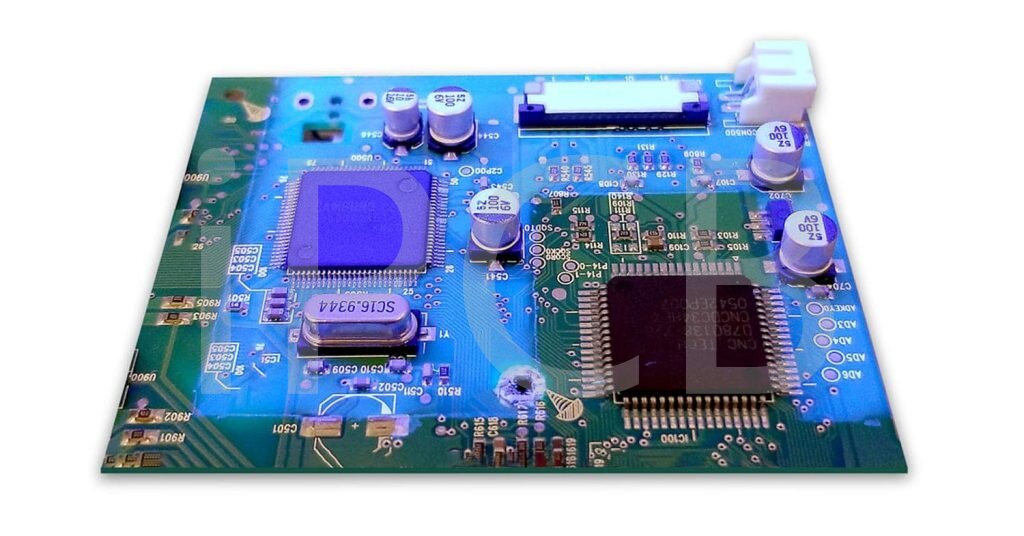
Why use conformal coating?
A conformal coating pcb, it is a protective material that you can apply to the printed circuit board when the assembly process is in the final stages.
- Provides comprehensive protection
Tri-conformal coating protects the circuit board from moisture, dust, fungus, extreme temperatures and other contaminants. In recent years, the demand for pcb that can withstand extreme environmental conditions has been increasing.
The coating resists various chemical attacks, such as corrosion. Without the use of conformal coating, your pcb will be at risk and some fragile components may be easily damaged when exposed to extreme temperatures. - Extend the life of PCB boards
Conformal coating not only protects PCBs to ensure reliability, but its protective layer also extends the life of the board, thus reducing your costs.
By applying conformal coating to the surface of PCBs, the life of PCBs will be extended to five years, and sometimes even to 10 to 15 years. This will save you the cost of purchasing new products every six months or so due to damage to the vulnerable parts of PCBs. The thin layer of PCB coating material will protect your PCBs from harm and give you value for money for years to come. PCB conformal coating provides reliability for long-term use, which makes it an excellent choice in the PCB assembly process. - Improve dielectric properties
Dielectric strength is a measure of the insulating effect of conformal coating. Conformal coatings with high hydrophobicity and lower extractable ionic impurities have a higher possibility of water repellency.
Therefore, they have higher dielectric strength. When you apply conformal coating on PCBs, it provides an extra layer of protection for your product. Protect PCBs from corrosion. - You can apply it easily
There are many ways you can use conformal coating on PCBs. The additional protection of conformal coating makes the circuit board durable and reliable. Some methods of applying the layer include dipping, brushing, and spraying. - Dipping
You can use this technique when producing many pcbs as the coating penetrates every component. This is not the best technique for conformal coating as it can cause leaks. Also, it is not suitable for many circuit boards. - Spraying
You can do this by applying the layer to the surface of the pcb using a spray bottle or spray gun. This is the best method to use if you are producing a small or medium amount of pcbs. It has advantages over brushing and dipping. With the right experience and skill set, spraying is the best choice for coating pcbs. However, spraying does not allow some components to penetrate deeply, which can be a problem if you want the coating to reach certain parts. - Save time and cost
Conformal coating is cost-effective, and the various available methods of using these coatings can save time. The application process is simple and time-saving. Like most manufacturing processes, the application method of three-proof coating has taken a new turn in recent years; hence, the shift from manual application mode to automatic application mode. - Protect sensitive information
By applying the right amount of conformal coating on PCBs, it protects sensitive components from extreme temperatures. When designing PCBs, some components may be susceptible to damage. Harsh conditions such as rain, dust, high temperatures, etc. can shorten the life of PCBs. Using conformal coating on your PCBs can help reduce the need for replacement or repair after a short period of use. It also acts as a protection for fragile components of PCBs.
From dipping and spraying, the application mode has shifted to a selective robotic coating process. Depending on your budget and the number of PCBs you want to produce, conformal coating can be both inexpensive and time-saving.
Another form of spraying is the automated method, which is generally faster than manual spraying, and by conducting an extensive evaluation of your PCB design, you will understand the coating material that is right for you.
Types of PCB Coating Materials
Different PCB coating types offer different levels of protection. In addition to the cost difference, some are easier to apply or remove than others. They include silicones, acrylics, epoxies, polyurethanes, and parylene. Below is a description of their properties.
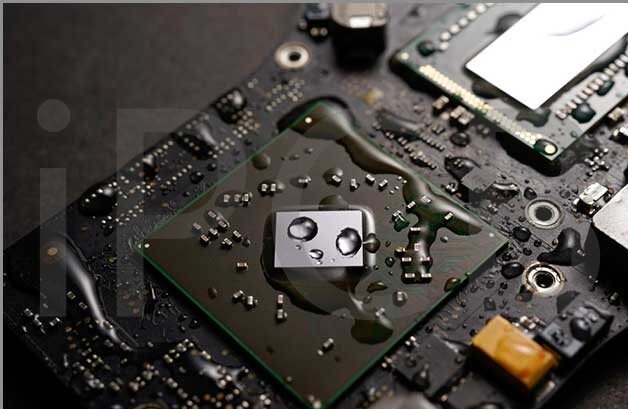
- Silicone Coating
Silicone has several positive properties that make it one of the most favored types of conformal coatings for pcbs. It has high resistance to abrasion and moisture, and it withstands temperature changes excellently.
It is rubbery and highly elastic, resists vibrations, and is well suited for most outdoor applications. Its soft nature also makes it suitable for sensitive circuit board components.
On the downside, the film has a low tolerance to chemicals and oils. Removing it is also challenging, requiring vigorous stirring and the use of specific solvents. It is also relatively expensive. - Acrylic Coating
Acrylic is the simplest of all pcb coating types, being inexpensive and easy to apply. It is equally easy to strip when reworking or repairing the board. You only need a solvent.
But these properties make it less effective as a protective film, with lower resistance to chemicals, salt spray, and other environmental conditions such as moisture and abrasion.
On the other hand, it has good physical qualities and electrical properties and cures instantly. These qualities make it the best choice for low-cost circuit boards used in mild environments or in applications with limited exposure to adverse conditions. - Epoxy Coating
Epoxy hardens into a wear-resistant film, making it one of the most commonly used types of PCB coatings. It also handles well against a variety of hazards, including chemicals, moisture, and other environmental factors.
Due to these properties, it takes effort to remove epoxy when reworking PCBs. It also takes time to cure and is not suitable for high-volume runs.
In addition, PCB epoxy coatings are prone to cracking in extreme vibration environments. Therefore, its use is mainly limited to applications with special requirements. - Polyurethane Resin Coating
Polyurethane has good performance in preventing various forms of damage. Not only is it wear-resistant, it can also withstand moisture and chemicals.
These properties make it the material of choice for most application conditions. The disadvantage is that it takes a long time to harden and may not be suitable for large quantities of circuit boards.
Polyurethane film is also one of the most difficult films to remove, requiring steps such as a combination of long soaking and specific solvents. - Parylene Coating
Parylene is a film applied using a unique technique called chemical vapor deposition. Among all PCB coating types, it has unparalleled tolerance to withstand extreme temperature changes, high humidity levels, corrosive materials, and more.
However, this also makes it difficult to stick or peel the film. It requires specialized vapor deposition process equipment, which increases the ease and cost of application.
Application Fields of pcb coating materials
Initially, conformal coating did find a lot of applicability on printed circuit boards that belonged only to high-tech environments. However, this is not the case today, and the application fields of PCB conformal coating continue to grow by leaps and bounds. At this point, we are going to go. We will focus on the use or application of PCB conformal coating. Typical application fields of PCB conformal coating include:
- Automotive Industry PCB
Looking at the entire automotive industry, you will find something different. Electronic systems have been widely used in this field recently. Therefore, the use of printed circuit board conformal coating plays a big role here. It ensures the protection of key components of the car, especially in the case of salt spray and gasoline evaporation. All of this and more ensure the long-term reliability of the motor. - Consumer Electronics PCB
In addition to the automotive field, printed circuit board conformal coating is also suitable for other fields. For example, it protects the circuits used in home appliances. Applying conformal coating to home appliances solves many problems. Use PCB conformal coating in your home appliances and ensure better functionality. - Navigation Products PCB
Salty seawater and fresh water can have a devastating effect on the circuits in navigation equipment. Here, materials are susceptible to some damage once they come in contact with water. However, all is not lost thanks to PCB conformal coating procedures. Conformal coating prevents the rate of corrosion. It reduces corrosion on the exterior of the device as well as on the underwater components. - Medical Device PCB
The medical field is another area that relies on PCB conformal coating. Across the industry, conformal coatings seem to play a vital role. For example, it protects electronic medical devices from corrosion. Chemical agents are shared across the medical field and are often harmful to the equipment that the industry relies on on a daily basis. However, now with conformal PCB coating, such problems can be avoided. - Military PCB
Electronic equipment used in military applications operates under the most demanding conditions. Military equipment must be able to withstand constant and severe vibrations. In addition, they should be able to function properly under extreme temperature conditions. To protect such devices from damage, PCBs must be conformally coated. Thanks to PCB conformal coating, it is now possible to protect military equipment. It is much easier to protect them from oxidation and corrosion. - High-tech products PCB
High-tech fields such as science, technology, engineering, and mathematics often use high-tech equipment. For example, in a laboratory environment, you will find high-tech equipment. Some of them include vibrators, test chambers, stirrers, and vacuum chambers are common. All of these have basic components that must function properly. With PCB conformal coating, any challenges that may occur can be avoided. This is because PCB conformal coating can be applied here as well.
Protective coatings are an important part of printed circuit boards, and the thickness is usually between 3-8 mils (0.075-0.2 mm). They are widely used in industries such as aerospace, automotive, military, marine, lighting, consumer electronics, and industrial. Based on the chemical composition, protective coatings can be divided into five types, namely acrylic, epoxy, polyurethane, silicone, and paraxylene. The choice of a specific coating is based on the application and electronic requirements of the pcb. Using the wrong surface coating on the pcb can damage the board. It can also lead to wasted time, money, resources, and energy.
As a pcb manufacturer, it is crucial to choose the perfect coating for the pcbs you manufacture. There are many advantages to choosing a pcb coating material. It protects the board from vibration, moisture, dust, rain, heat, and other harsh conditions. Contact us today to set up an appointment and let us add value to your ongoing and future pcb projects.