PCB cutter is a mechanical equipment specialized in cutting circuit boards. It cuts circuit boards accurately and quickly by means of a high-speed rotating cutting tool to meet the needs of different electronic products on the size and shape of circuit boards.
Cutting is the first step in material analysis. The choice of cutter as well as cutting blade must be in accordance with the geometry and material properties of the specimen, and perfect metallographic cutting should avoid thermal damage and deformation of the tissue while maintaining the necessary accuracy and speed.
Good or bad cutting may affect the final results, so how to choose the metallographic cutting machine is particularly important. Due to the different requirements of metallographic sample preparation, there are certain requirements on the direction of feed, clamping direction, feed speed and cooling method when cutting samples, which is why there are various forms of cutting machines designed for this preparation process.
For PCB depaneling or cutting, a CO2 laser system with a wavelength of approximately 10.6μm can be selected. It is relatively inexpensive to process and can deliver up to several kilowatts of laser power. However, it generates a lot of heat during the cutting process, which can cause severe carbonization of the edges.
UV lasers have a wavelength of 355 nm, which makes the laser beam very easy to focus optically. UV lasers with less than 20 watts of laser power have a focused spot diameter of only 20 μm and produce an energy density comparable to that on the surface of the sun.
Analyzing the advantages of UV laser processing
UV lasers are particularly suitable for cutting and marking hard boards, rigid-soft boards, flexible boards and their accessories. UV laser cutting systems offer great technical advantages in areas such as depaneling in the SMT industry and microdrilling in the PCB industry. Depending on the thickness of the circuit board material, the laser cuts along the desired contour once or several times. The thinner the material, the faster the cutting speed. If the accumulated laser pulses are lower than those required to penetrate the material, only scratches will appear on the surface of the material; therefore, the material can be marked with a QR code or barcode for information tracking in subsequent processes.
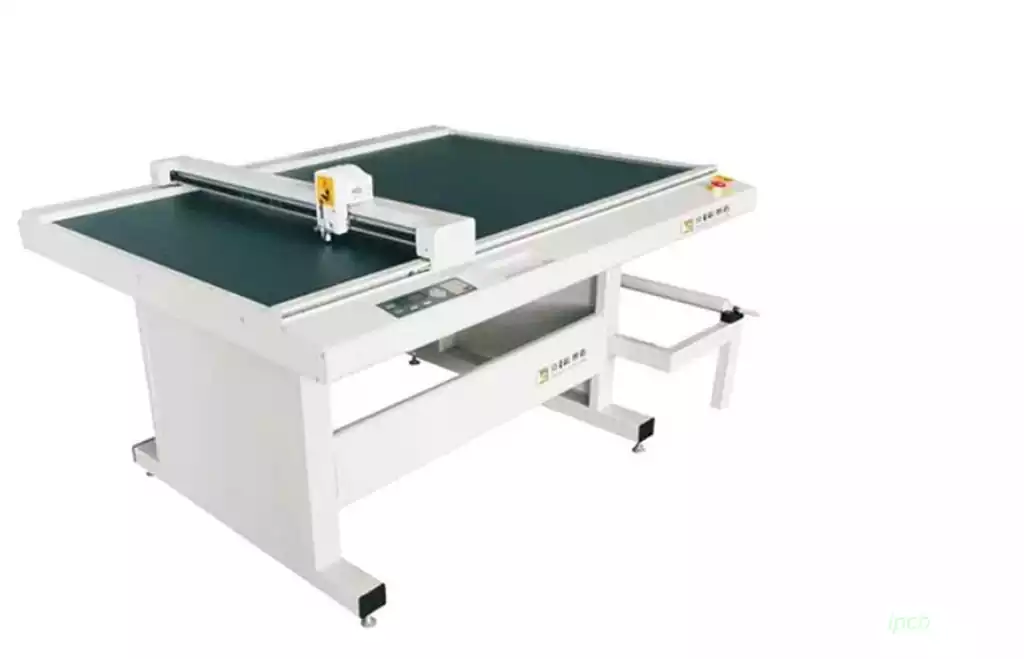
Rigid-Flex Processing
In rigid-flex PCBs, rigid PCBs are pressed together with flexible PCBs to form a multilayer board. During the pressing process, the top of the flexible PCB is not bonded with the rigid PCB, and the rigid cover over the flexible PCB is cut and separated by laser fixed-depth cutting, leaving the flexible part to form the rigid-flexible board.
Such fixed-depth processing is also applicable to the processing of blind slots for surface-embedded integrated components in multilayer boards. the UV laser precisely cuts the blind slots of the target layer separated from the multilayer board. In this area, no connection can be formed between the target layer and the material covering it.
FPC flexible boards are generally molded by either die-punching or cutting. Users choose different molding methods according to the number of flexible circuit boards required, the size of the precision, and the length of the customer’s required delivery time.
Die-punching molding is the use of molds on the flexible board semi-finished products for punching and cutting to create a flexible board shape, different FPC products require different molds.
Cutting molding CNC knife cutting molding and laser molding two kinds, due to the laser molding processing with high precision, speed, burr less, cutting round and square, etc., can effectively save time and cost, therefore, laser cutting gradually become the ideal tool for FPC cutting molding processing. Nowadays, the vast majority of FPC sample production and small batch processing, are using laser cutting molding.
Ceramic laser cutting machine advantages
1.Fine processing
Selection of the international mainstream laser, beam quality, high quality cutting, can complete the minimum line width of 5um fine processing (depending on the material material)
2.Improve production efficiency
Double wire rod, double motor drive system, improve productivity, running speed can be as large as 1000mm/s.
3.Realize high speed cutting
The software has graphic layout and sharp corner smoothing function, which can realize high-speed cutting, punching and marking function.
4.Professional cutting software
Professional cutting software, multi-level authority to operate, easy production management.
5.High stability of equipment
High cutting precision, the whole machine cutting precision ± 25um, high stability of the equipment, CPK>1.33
6.Fiber optic conduction
The whole machine optical path is fiber optic conduction, the external optical path is maintenance-free, and the consumption of perishable quantities is very small.
- High precision and stability
The whole machine is cast, with high precision and stability.
Ceramic laser cutting machine application range
Mainly used in alumina, aluminum nitride, zirconia and other ceramic materials. Realize fast and precise cutting, drilling and scribing.
PCB cutter plays an indispensable role in the field of electronic product manufacturing with its high accuracy, efficiency, adaptability and flexibility.