PCB gold plating technology plays a vital role in the field of electronic manufacturing, especially in the production of circuit boards. However, in practice, the electroplating process may encounter a series of failures, these failures not only affect the production efficiency, but also may reduce product quality.
Common Failures
Uneven plating: In the plating process, uneven current distribution, insufficient plating solution mixing, or improper pretreatment of the substrate surface may lead to uneven thickness of the plating layer, affecting the conductivity and aesthetics.
Poor plating adhesion: the presence of oil, oxides, or mismatch of plating solution composition on the surface of the substrate will cause insufficient adhesion between the plating layer and the PCB substrate, resulting in easy peeling off of the plating layer.
Plating surface defects: including pinholes, bubbles, skinning, and other phenomena, these defects are usually caused by impurities in the plating solution, gas or tiny particles on the surface of the substrate.
Equipment failure: Failure of plating equipment such as power supply, pumps, temperature control devices, etc. will also directly affect the plating process, resulting in unstable plating quality.
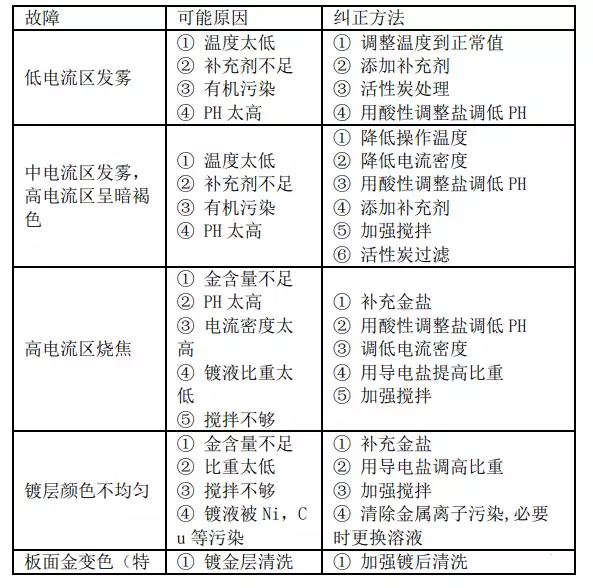
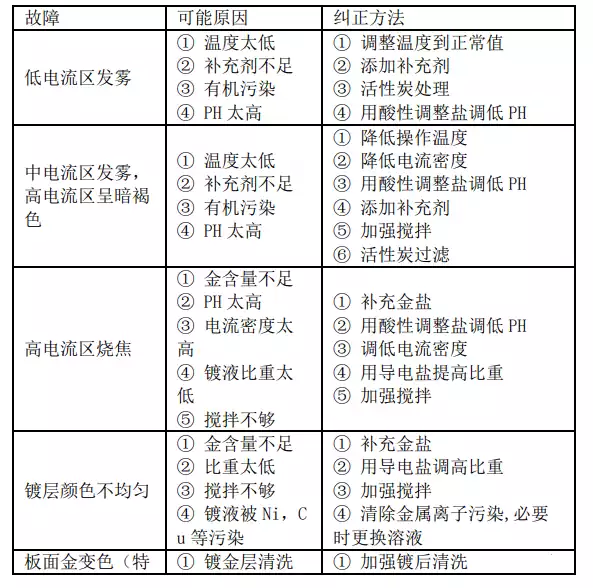
Optimization Solution
Improve plating process parameters: By adjusting parameters such as current density, plating time, plating solution temperature, and pH value, the current distribution can be made more uniform to improve the plating quality and uniformity.
Enhance substrate pretreatment: thoroughly clean and activate the substrate before plating to remove surface oils and oxides and increase the bonding force between the plated layer and the PCB boards.
Optimize plating solution management: Regularly test the plating solution composition and adjust the plating solution formula to maintain the stability and cleanliness of the plating solution and reduce the influence of impurities and gases.
Enhance equipment maintenance: Regularly maintain and service plating equipment to ensure that the equipment is in good condition and reduce the impact of equipment failure on the plating process.
Introducing automation and monitoring technology: adopting automation control system and real-time monitoring technology to accurately control the plating process, discover and deal with abnormal situations in time, and improve production efficiency and product quality.
Through the implementation of the above optimization scheme, the common faults in the process of circuit board electroplating can be effectively solved, thus improving the stability and reliability of the pcb gold plating process and meeting the demand for high-quality circuit boards in the electronic manufacturing industry.