PCB potting refers to the filling of potting adhesive into the void of PCB. Potting (potting) is the polyurethane potting adhesive, silicone potting adhesive, epoxy resin potting adhesive with equipment or manual way into the device equipped with electronic components, lines within the device, at room temperature or under heating conditions to become a thermosetting thermosetting polymer insulating material with excellent performance, so as to achieve the PCB sealing and protection, to prevent moisture, dust, etc. to enter the interior of the circuit board, to improve the reliability and stability of the circuit board.
PCB potting and Coating
Coating refers to the coating process, such as the circuit board surface coating of three anti-paint, the thickness is relatively thin, such as 50um ~ 90um, Potting refers to the filling of glue, such as a plastic box equipped with PCBA, in the plastic box filled with resin adhesive, will be the PCB and above the parts of the sealing.Potting to fill the main, Coating to the surface of the main.
Selective coating process is a new protective technology in electronic patch processing, then this new technology is what we often say that the printed circuit board three defense coating process. Printed circuit board design, should be based on the use of electronic products in the environment, can be required to choose to meet the requirements of the use of environmental requirements of electronic components, process materials and assembly process, to be Kaoh Chung anti-heat, anti-salt spray, anti-mold requirements.
Types of Coating
- Anti-moisture and heat: When the relative humidity of the air is greater than 80%, especially in high-temperature environments, a lot of electronic equipment in the organic and inorganic materials due to the influence of moisture and heat to increase the weight of the components, swelling, deformation, will be the components of the corrosion accelerated. If the selection of insulating materials and processes are not properly handled, the insulation resistance decreases, so that insulation breakdown, and performance destruction, fail. To ensure reliability, should be designed to prevent moisture.
- Anti-salt spray: the effect of salt spray refers to the combination of salt spray and humid air, which contains a small radius of chloride ions on the metal protective film and has a penetrating effect. Salt and water combined can make the material conductive, so it can make the insulation resistance decrease, causing metal galvanic corrosion and chemical corrosion to accelerate so that the metal parts and electrical parts the damaged. Sulfur dioxide, chlorine, ammonia, and other harmful gases and humid air will produce acidic, alkaline gas. These gases also have the effect of accelerating the corrosion of metal components, so that the insulation is reduced.
- Anti-mold: Mold, termites, and other organisms will also have an impact on the product under different circumstances. For example, mold in a certain temperature, humidity (generally 25 ~ 35 ℃, relative immersion of 80% 6 or more) of the environmental conditions, reproduction and growth of rapid growth, the secretion of the formation of spots affecting the appearance of the product; these secretions contained in the weak acid will make the electrical instrumentation of the metal wire corrosion broken, damage to the circuit function. Especially in the optical instruments on the long mold, it will make the glass reflection and light transmission decrease significantly, destroying the optical performance. Therefore, the design should also be mold-proof design.
Types of Potting Adhesive
Polyurethane Potting Adhesive
Polyurethane pcb potting adhesive has more excellent low-temperature resistance, the hardness of the gel can be adjusted, and can also provide high elongation,with good tear resistance. For general potting materials have good adhesion, high adhesion, and good abrasion resistance.
Temperature requirements, not more than 100 degrees Celsius, more vapor bubbles after potting, pcb potting conditions in a vacuum,adhesion between epoxy and silicone.
Advantages: excellent low-temperature,with good anti-vibration properties.
Disadvantages: high-temperature resistance is poor, the surface of the cured colloid is not smooth and has poor toughness, aging resistance and UV resistance are weak, and the colloid is easy to discolor.
Scope of application: suitable for potting indoor electrical components with low heat generation.
Epoxy resin potting gel
Epoxy resin potting adhesive is mostly hard, there are very few modified epoxy resin that is slightly soft. The material’s greater advantage lies in the better adhesion to the material and better insulation. Good corrosion resistance and dielectric properties can resist acid, alkali, salt, solvents, and other media corrosion.
Advantages: excellent high-temperature resistance and electrical insulation ability, simple operation, very stable before and after curing, excellent adhesion to a variety of metal substrates and porous substrates.
Disadvantages: weak resistance to hot and cold changes, easy to produce cracks after being subjected to hot and cold shocks, resulting in water vapor infiltration from the cracks into the electronic components, poor moisture resistance. After curing, the hardness of the gel is high and brittle, easy to strain the electronic components.
Scope of application: suitable for potting electronic components at room temperature and no special requirements for the mechanical properties of the environment.
Silicone potting adhesive
Silicone potting compound has stable physical and chemical properties, with good resistance to high and low temperatures, and can be in the range of -40 ~ 200 ℃ long-term work. Excellent weather resistance, in the outdoors up to 20 years or more can still play a good protective role, and is not easy to yellow. Excellent electrical properties and insulation ability, potting effectively improves the insulation between the internal components and lines, improves the stability of electronic components.
Advantages: strong aging resistance, good weather resistance, good impact resistance, excellent resistance to hot and cold changes and electrical properties; good thermal conductivity and flame retardancy, can be returned to repair.
Disadvantages:Compared with polyurethane rubber and epoxy rubber, the bonding performance of general silicone rubber is slightly worse. The mechanical properties of silicone rubber such as tensile strength and shear strength are poor, its physical and mechanical properties at room temperature is not as good as most of the synthetic rubber,and the general silicone rubber oil resistance, solvent resistance performance is poor.
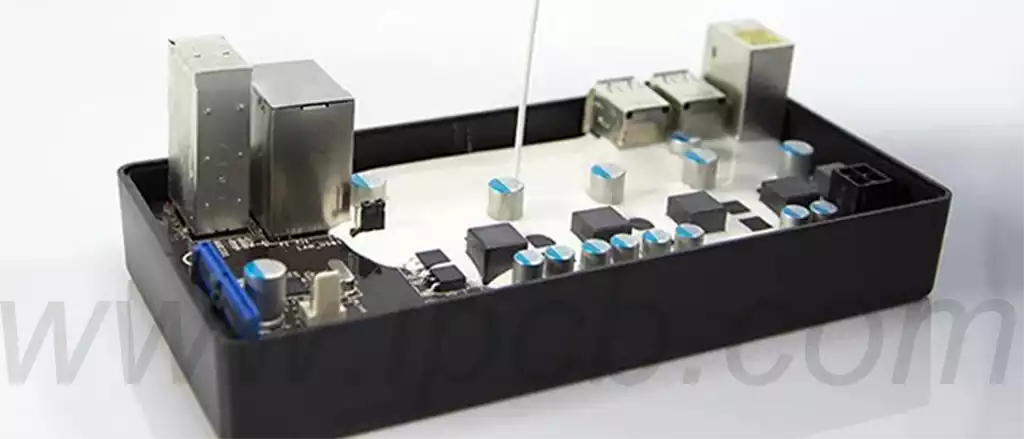
The role of PCB Potting:
Protect the circuit: pcb potting material can cover and protect the components and wiring on the circuit board, to prevent them from physical damage, pollution and humidity and other environmental factors.
Reinforce fixation: Potting materials can fill in the gaps and recesses on the circuit board, making the whole circuit board a solid whole, improving its mechanical strength and shock resistance.
Realize electrical connection: pcb potting material can be used as a conductive medium to realize electrical connection between certain components or wiring on the circuit board, simplifying the wiring design and manufacturing process.
Facilitate maintenance and replacement: The pcb potting process allows components and wiring on the circuit board to be sealed in the potting material, facilitating maintenance and replacement.
Common quality problems and solutions in the pcb potting process
1.Abnormal structure of cured colloid
If the cured potting compound is soft, it may be due to the incorrect ratio of curing agent to colloid. For example, too much or too little hardener may affect the hardness of the gel. In this case, it is recommended that the recommended weight ratio be strictly followed to ensure that the potting compound can fully cure and develop the desired hardness.
2.Surface defects
Frequent touching of the potting compound by hand during the curing process may lead to unsatisfactory film formation and ultimately to an uneven surface. The solution to this problem is to wait until the curing agent is fully cured after potting before handling by hand to avoid interference during the curing process, thus improving the flatness and quality of the final surface.
3.Bubble problem
The problem of air bubbles after potting is usually caused by too fast potting speed or improper operation. In order to solve this problem, it is possible to ensure that air bubbles do not form during the potting process by depressurizing the material or selecting a suitable potting material before potting. At the same time, you can consider using a slower potting speed to minimize the generation of air bubbles.
4.Suitable potting material selection
Selection of suitable potting materials is to ensure the quality of the basis of potting. Before potting, according to the specific needs of the product should be selected according to the appropriate type of potting adhesive, such as epoxy resin or silicone, which not only improves the performance of the product, but also effectively reduces the subsequent quality problems that may arise.
5.Standardized operating procedures
The establishment of standardized operating procedures and training of operators is also an important means to improve the quality of potting products. Through systematic training, so that the operator understands the characteristics of the potting material and its precautions in the use of the process, can minimize the quality problems caused by human error, improve the efficiency and quality of the entire potting process.
PCB potting and coating are two common process technologies for protecting circuit boards, each with its own characteristics and scope of use. In actual application, it is necessary to select and adjust according to the specific needs in order to achieve the best protection effect and production efficiency.