A pewter bead is a small, round ball-like substance that forms when tin is extruded between the pad and the component foot during the soldering process. The generation of solder beads is mainly related to the soldering temperature, flux and the surface condition of the printed wiring board.
Reflow soldering in the tin bead generation causes are analyzed as follows:
Reflow soldering curve can be divided into 4 zones, respectively, preheating, holding, reflow and cooling preheating, holding purpose.
- Incorrect temperature profile:
Is to make the PCB substrate surface in 60 ~ 90s to 150 degrees Celsius, and holding about 90s, which not only reduces the thermal shock of the PCB and components, more mainly to ensure that the solvent of the solder paste can be partially volatile not to be in the reflow soldering, due to the rapid increase in temperature appeared to be too much solvent and caused by splashing, so that the paste rushes out of the pad and the formation of tin beads. Therefore, attention should usually be paid to the rate of heating, and take moderate preheating, and a good platform to make most of the solvent volatilization, thereby inhibiting the generation of tin beads. - The quality of solder paste:
Solder paste in the metal content is usually (90 ± 0.5) %, the metal content is too low will lead to too much flux components, so too much flux will be due to the preheating stage is not easy to evaporate and cause flying beads.
Increased water vapor oxygen content in solder paste. Since solder paste is usually refrigerated, when it is taken out of the refrigerator, recovery time is not ensured, so it can lead to the entry of water vapor. In addition, the lid of the solder paste bottle should be tightened after each use, and if it is not covered tightly in time, it can also lead to the entry of water vapor.
Placed on the template printed solder paste in the completion of the remaining part should be handled separately, if put back into the original bottle, will cause deterioration of the bottle of solder paste, but also produce tin beads. - Printing and patching:
Solder paste in the printing process, due to the template and pad alignment offset, if the offset is too large will lead to solder paste dip flow to the pad outside, easy to appear tin beads after heating.
Therefore, the template should be carefully adjusted clamping, there should be no loose phenomenon, in addition to the printing of the working environment is not good will also lead to the generation of tin beads, the ideal ambient temperature (25 ± 3) degrees Celsius, relative humidity of 50% ~ 65%.
Patch process Z direction of the pressure is caused by an important reason for tin beads, often do not cause people to pay attention to, part of the mounter due to the Z-axis head is based on the thickness of the components to locate, so it will cause components pasted to the PCB plate in a flash will be squeezed to the pad outside the phenomenon, this part of the solder paste will obviously cause tin beads. This situation produces a slightly larger size of tin beads, usually just re-adjust the height of the Z-axis can prevent the production of tin beads. - Stencil thickness and opening size:
Stencil thickness and opening size is too large will lead to an increase in the amount of solder paste, but also cause solder paste diffusion to the pad outside, especially with chemical etching method of manufacturing the template.
The solution is to choose the appropriate thickness of the template and opening size design, general template opening area of 90% of the pad size.
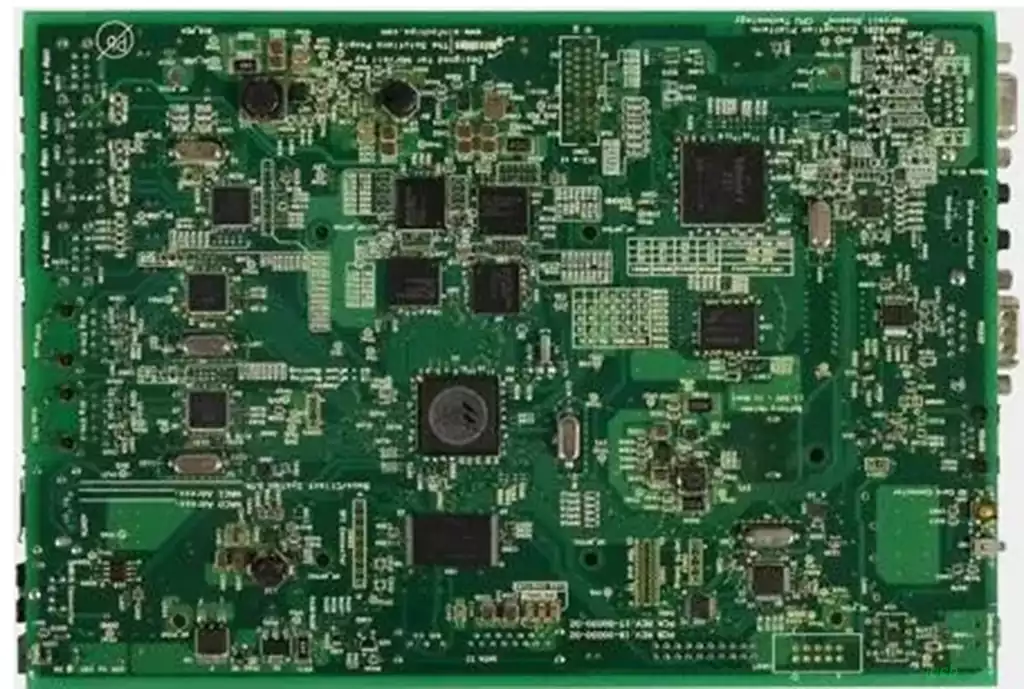
Reduce the generation of tin beads:
- Select the appropriate soldermask can prevent the generation of tin balls.
- The use of some specially designed flux can also avoid the formation of tin balls.
- Minimize the temperature of the solder product.
- Use enough flux to prevent the formation of tin balls.
- Maximize the preheating temperature, but pay attention to the flux preheating parameters to prevent the flux activation period from being too short.
- Maximize conveyor speed.
With the continuous progress of science and technology and the continuous innovation of welding process, we believe that there will be more effective solutions to deal with the problem of pewter beads. Electronic manufacturing enterprises should continue to pay attention to industry dynamics and technological development, and actively introduce and apply new technologies and processes to improve product quality and production efficiency, and win the competitive advantage in the market.