Main Steps in Printed circuit board fabrication:
To get a clear picture of the printed circuit board fabrication process, let’s take a step-by-step look at how a PCB develops from an idea on paper to the final product. While delving deeper into the PCB manufacturing process, it is worth noting that there are many types of PCBs and different levels of complexity. The number of steps we need to complete is proportional to the complexity of the PCB board in question, as shown below:
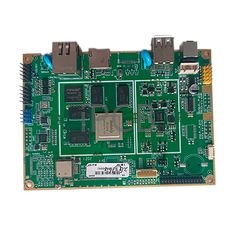
- PCB Layout Design:
Before any PCB board is manufactured, it needs to be laid out or designed. The layout of a PCB board is nothing but a circuit diagram in which each node has a clear path. The layout is not drawn with pen and paper but with the help of software such as Altium Designer, OrCAD, Pads, KiCad, Eagle CAD, and EasyEDA. Using software not only saves time but also makes it easier to make any last-minute changes to the layout. Once the design is completed, it is converted into the appropriate format for use in printed circuit board fabrication. The most commonly used extension of PCB layout drawings is the extension Gerber file. Each Gerber file marks the design of one PCB board. The Gerber file is DFM checked (Design for Manufacturing) in the hands of the manufacturer to check if it meets all industry standards. After approval, the layout is printed. A special type of printer called a plotter is used to print the PCB layout. The plotter is not an ordinary inkjet printer, but a special type of laser printer. The PCB layout cannot be printed on ordinary A4 paper, but only on some special films.
When connecting two or more traces on a printed circuit board design, you should avoid forming a 90-degree angle because it makes the traces more susceptible to corrosion and scab on the board. The 90-degree angle is also more susceptible to radio frequency, which reduces stability. In contrast, it has been found and tested that a 45-degree angle ensures that we get the most traces on the minimum area on the PCB board and is not prone to corrosion. In addition to this, we may have seen parallel lines on the PCB board that are parallel to each other but of different lengths. This is called length matching of traces. As the name suggests, it matches the length of the path so that two or more signals arrive at a certain node at the same time and accurately, so that sometimes we need the signal to arrive at a specific point at a specific time. - Substrate Cutting:
In this step, we cut the large sheet of PCB substrate into small pieces. Cutting the PCB will make it space more efficient and more uniform. In addition, cutting homemade PCBs allows you to save material costs. You can reuse the materials cut from the PCB and integrate them into other projects. For example, the substrate size is about 36×48 inches, and it is difficult to cut it into small pieces of 18×24 inches in PCB production. Its core consists of copper sheets and dielectric substrates. Epoxy resin (FR-4) is mainly used in multi-layer PCB board manufacturing, and fiberglass is used to make the board strong, durable and impact-resistant. Laminate is an ideal carrier for copper reception on both sides, also known as copper clad laminate (CCL). - Pattern Printing:
The PCB layout is printed by a plotter on a negative film, which is marked with different ink areas. These negative films are also layer-specific, that is, for the inner layers of the PCB board, the black ink represents the conductive path and the other areas represent the non-conductive path. However, for the outer layers of the PCB board, the meaning of the ink color is completely different. On the outer layer, black represents non-conductive paths and other areas mark conductive paths. - Photoresist coating:
After cleaning is completed, a layer of photoresist film is applied on the circuit board. Photoresist film consists of photoreactive chemicals that harden when exposed to ultraviolet light. Photoresist is applied in order to trace the conductive path from the negative film to the laminate with the help of ultraviolet light. A drilling machine is used to punch positioning holes on all holes to achieve perfect alignment of all layers. After that, chemical copper plating is made through the board so that the PCB conductivity of the entire board remains intact and both the top and bottom surfaces remain connected. - Tracing exposure:
In PCB construction, the most important process is the pattern tracing from the negative film to the copper clad laminate. As mentioned earlier, different areas are traced on the film. When the copper clad laminate and its corresponding layout are stacked on it, some visible areas appear. These areas mark the conductive traces. When ultraviolet light passes through, it passes through the visible area and reaches the photoresist film that is sensitive to ultraviolet light and immediately melts and hardens on the copper clad laminate. Only the photochemically hardened part is visible from the conductive traces of the film, the rest is blocked by the black ink and remains semi-liquid. After all the paths are successfully traced, the board is ready to be cleaned of the unwanted photoresist. For this, it passes through an alkaline solution, which cleans all the wet photoresist material on the PCB board, and the hardened photoresist covers the conductive paths. - Etching of the outer copper layer:
The PCB board is almost ready, and now the only unwanted thing on it is the copper in the non-conductive areas. This process is called etching. To easily remove the excess copper, prepare a ferrous chloride solution in a 1:1 ratio and let the board soak in it for a few hours. The solution removes the copper from the board, leaving only the copper covered with photoresist. To wash off the hardened photoresist, use acetone on the board first, and then water. - Alignment check:
To make sure that the locating holes are intact, a final check is required before all the layers are combined with each other. All the layers are placed inside a machine that uses the original Gerber files as a model to accurately check the location and alignment of the locating holes in all the layers. If no inaccuracies are found, the layers will go to the final stage of the PCB board manufacturing process; if inaccuracies are found, the inaccuracies will be displayed on the screen for the PCB manufacturer to fix. - Lamination:
Generally speaking, in the process, we will laminate the inner copper layer with the outer copper layer and put dielectric material between the copper layers, and then heat press them to bond them to each other. For example, when we purchase a four-layer PCB, we will first make the core board (copper layers 2 and 3), and then put thin layers of dielectric material (here we call it prepreg) and thin sheets on the top and bottom core boards, and then press them together through a press machine. - Drilling:
Now that a fully functional PCB board is ready with all layers intact, it is time to start drilling. Drilling is mainly used to connect all the layers. Drilling is done to solder components to the PCB board. Nowadays, most use surface mount devices (SMD), but this option is still retained. Holes are also punched to maintain the diversity of PCB uses. - Copper Plating:
Copper plating has two functions: first, it is used to plate copper into the walls of the drilled holes to connect all the copper layers; second, it will add thicker copper to the copper traces on the top and bottom layers. - Outer Layer Imaging and Etching:
During this process, the outer layers of the PCB board are traced in a similar manner to the inner layers. After the traces are completed, the unwanted copper and other materials are also etched in a similar manner. A protective layer is applied to the newly formed circuit boards to protect them from further etching processes, where the desired conductive paths may be damaged and may cause the board to malfunction. After all etching processes are completed, it is then removed by chemical methods. - Solder Mask:
It is usually the green mask we see on printed circuit boards. The solder mask is applied to the surface of the PCB to prevent oxidation and corrosion damage and to isolate it from other circuits during the PCB assembly process. - Silk Screen:
Finally, if there are any labels or icons in the layout design that need to be printed on the PCB board, this can be done through silk screen printing (inkjet printing). Silk screen printing is used for information graphics on PCB boards. - Surface treatment:
It is a layer of tin solder or silver, gold or other metals applied to the PCB board. This is done to provide the circuit board with additional protection against dust, moisture and oxidation, and also facilitates PCB assembly. - Electrical testing:
Before putting the circuit board on the market, all circuit boards will be electrically tested first, and some manufacturers sometimes provide some special tools to test. If the test results are suitable, the circuit board will be put on the market for innovators, engineers and all those who need it. - Final inspection:
After the test is completed, the production of the PCB board is basically completed. But before shipping, we still need to check for minor visual defects such as scratches through inspection machines or manually.
In addition, single-sided boards, double-sided boards, and multi-layer boards are classified according to the number of conductive pattern layers.
PCB with conductive patterns on only one side of the insulating substrate, the most basic printed circuit board. On a single-sided board, the parts are concentrated on one side, and the wires are concentrated on the other side. Because the wire only appears on one side, it is called a single-sided board. It is mainly used in earlier circuits or simple electronic products.
There are conductive patterns on both sides of the insulating substrate. Since there are conductive patterns on both sides, metallized holes are generally used to connect the conductive patterns on both sides. Since the wiring of the double-sided board can be interlaced with each other (it can go around to the other side), the difficulty of wiring is reduced compared to the single-sided board, so it can be used on more complex circuits than single-sided boards.
There are four or more layers of conductive patterns on the printed circuit board. The inner layer of the multilayer board is made of conductive patterns and insulating adhesive sheets laminated and pressed, and the outer layer is copper foil, which is pressed into a whole. In order to lead out the printed wires sandwiched in the middle of the insulating substrate, the holes (i.e. guide holes) for mounting components on the multilayer board need to be processed with metallized holes to connect them with the printed wires sandwiched in the insulating substrate. The number of layers of the multilayer board is usually an even number, and it includes the two outermost layers, which can be used for more complex circuits.
Summary
The above is all about the manufacture of printed circuit boards. The manufacture of printed circuit boards is a complex and delicate process, and every link requires strict control and management. With the development of science and technology, the circuit board manufacturing process is also constantly innovating and improving to meet the needs of continuous upgrading of electronic products. In the future, printed circuit board fabrication will develop in the direction of higher precision, higher efficiency and more environmental protection, providing strong support for the development of the electronics industry.