Alumina board,the main component of which is aluminium oxide (Al₂O₃), is a ceramic material made by high temperature sintering. With its excellent physicochemical properties,it shows a strong potential for application in a number of fields.
The wide range of applications for alumina board stems from a number of excellent properties:
High hardness and wear resistance: Alumina is second only to diamond in terms of hardness and has very high wear resistance, making it excellent for applications where resistance to abrasion is required.
High strength and rigidity: Aluminium oxide has a high compressive and bending strength and can withstand large mechanical loads without deformation.
Excellent heat resistance: Alumina has a high melting point of 2050°C, which makes it suitable for use in high-temperature equipment and environments, as its physical and chemical properties remain stable at high temperatures.
Good chemical stability: Alumina has excellent corrosion resistance,can resist the erosion of acids, alkalis and other chemical substances, suitable for the chemical industry.
Good insulation: Alumina has a high resistivity, is an excellent insulating material, widely used in the electronics industry.
Alumina PCB is a kind of printed circuit board with Aluminium Oxide (Al2O3) or Aluminium Nitride as the substrate.Compared with the traditional FR-4 PCB, alumina PCB has higher thermal conductivity,better electrical insulation,lower dielectric constant and dielectric loss,and higher mechanical strength and chemical stability.Currently, aluminium oxide is the most commonly used material in alumina PCBs.
Advantages of Alumina board
High thermal conductivity:Alumina ceramics have excellent thermal conductivity,can be effective in the heat generated by the electronic components to emit, reduce the operating temperature of the components, improve product reliability and life.
High insulation: alumina ceramics have good electrical insulation properties, can effectively prevent short circuits and interference between the circuit to ensure the normal operation of the circuit.
Low dielectric constant and dielectric loss: alumina ceramics have a low dielectric constant and dielectric loss, in high-frequency circuits to reduce signal delay and loss, improve signal transmission speed and quality.
High mechanical strength and chemical stability: alumina ceramics have high mechanical strength and chemical stability, can withstand greater mechanical stress and harsh environmental conditions, to ensure product stability and reliability.
High cost-effective: Alumina ceramic PCB has a high cost-effective ratio in the electronic packaging industry due to sufficient raw materials, affordable price and perfect manufacturing and processing system.
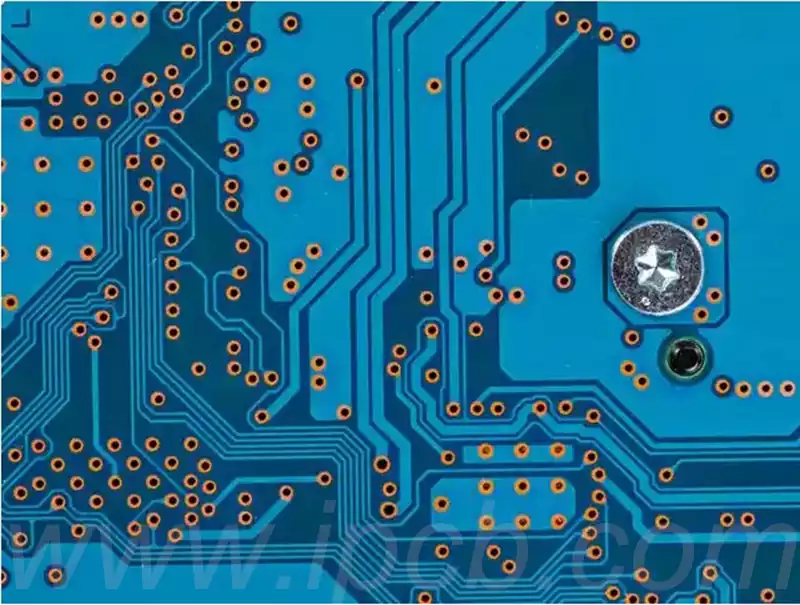
Alumina board has been widely used in the following fields due to its excellent performance:
High-power electronic devices Alumina board is suitable for the manufacture of high-power LED lighting, power amplifiers, power modules and other high-power electronic devices.
High-frequency circuits: Alumina board is suitable for the manufacture of microwave circuits, radio frequency circuits, antennas and other high-frequency circuits.
Optoelectronic devices: Alumina board has high optical transparency and chemical stability, and are widely used in the manufacture of lasers and LEDs and other optoelectronic devices.
Automotive electronics: Aluminium oxide PCB is suitable for the manufacture of automotive engine control unit (ECU), on-board power supply, sensors and other automotive electronics.
Medical equipment: Aluminium oxide PCBs are suitable for the manufacture of medical imaging equipment, diagnostic equipment, therapeutic equipment and other medical equipment.
Manufacturing process of alumina board:
Selection and preparation of raw materials
The manufacture of alumina board begins with a rigorous selection of raw materials. High purity alumina powder is the key to manufacturing high quality alumina substrates, and its purity and particle size distribution can significantly affect the quality of the substrate.Typically,the particle size of the powder should be less than 1 micron. For subsequent moulding,binders and plasticisers may need to be added to the powder, depending on the specific moulding method, such as extrusion or injection moulding. For example,extrusion or injection moulding typically requires the addition of 10-30% by weight of thermoplastic or resin to the powder. For dry compression moulding, spray granulation is required to improve the flow of the powder and lubricants are added to reduce friction between the powder and the mould wall.
Forming methods
Alumina ceramics can be formed by a variety of methods, including dry pressing, slurrying, extrusion,cold isostatic pressing,injection moulding, casting, hot pressing and hot isostatic pressing. Different moulding methods are suitable for products of different shapes, sizes and complexity.
Dry pressing technology:Dry pressing technology is suitable for simple shapes with a wall thickness of more than 1mm and an L/D ratio of not more than 4:1.
Slurry forming Slurry forming was the first forming method used for alumina ceramics and is suitable for the manufacture of large and complex parts, but the key lies in the preparation of the alumina slurry.
Other moulding methods:There are also new technologies such as filter press moulding, direct solidification injection moulding, gel injection moulding, centrifugal injection moulding and solid free-form manufacturing.
Sintering
Sintering is the process of densifying ceramic particles to form a solid material by eliminating inter-particle voids as well as gases, impurities and organic matter, allowing the particles to grow and combine to form a new material. Alumina ceramics are usually sintered at temperatures between 1450 and 1800°C with the addition of sintering aids such as clay, MgO, CaO and TiO. Sintering methods include atmospheric pressure sintering, hot pressure sintering, electric field sintering, ultra-high pressure sintering and atmosphere sintering. Hot isostatic pressure sintering uses high-temperature and high-pressure gas as the pressure medium to make the heating uniform, which is suitable for parts with complex shapes and can significantly improve the material properties.
Post-processing
After sintering,alumina ceramics may require finishing. For example, products used as artificial bone require highly polished surfaces to improve lubricity. Due to the high hardness of alumina ceramic materials, harder grinding and polishing materials such as SiC, B₄C or diamond are required. Finishing techniques include diamond grinding, laser processing and ultrasonic grinding and polishing.
Quality control
Quality control is an integral part of the aluminium oxide board manufacturing process. Finished PCBs are visually inspected to detect any potential defects. In addition to visual inspection, rigorous electrical testing is performed to check circuit continuity and isolation.
Overall, the manufacturing process for alumina board is complex and delicate, and requires strict control over each step of the process to produce high-performance boards that meet the needs of specific applications.