Rigid flex PCB is a special type of printed circuit board that combines the characteristics of rigid and flex PCBs. It uses a flexible material, such as polyimide or polyester film, as the substrate and a rigid material, such as glass fiber-reinforced epoxy resin, as the backing layer. By combining a flexible substrate with a rigid base layer, a rigid-flex PCB has both the mechanical strength and stability of a rigid board and the bendability and twistability of a flexible board.
There are significant differences between rigid flex PCB and normal rigid PCB. It uses a flexible material, such as polyimide or polyester film, as the substrate and a rigid material, such as glass fiber-reinforced epoxy, as the backing. This makes rigid-flex PCBs both rigid and flexible. In contrast, ordinary rigid printed circuit boards use only rigid materials such as FR4 or aluminum substrates.
The manufacturing process for rigid-flex PCBs is relatively complex and involves a combination of materials and processes. The following are the main process steps for general rigid-flex PCB manufacturing:
Material Preparation:
Flexible material: Select a suitable flexible material, such as polyimide or polyester film, as the substrate for the circuit board.
Rigid materials: choose a rigid material such as glass fiber-reinforced epoxy resin as the substrate.
Cleaning and surface treatment:
Cleaning: Ensure that the surface of the substrate is free of dust, oil, and other impurities.
Surface treatment: Surface treatment is performed on the substrate to provide adhesion for the subsequent attachment of circuit layers and protective layers.
Inner layer manufacturing:
A dry film (photoresist) is applied to cover the flexible material as an anti-corrosion layer.
Using photolithography, the desired circuit pattern is formed on the inner layer.
An etching process is performed to remove the copper foil that is not covered by the anti-corrosion layer to form the conductive path.
Outer layer fabrication:
Prepare protective and conductive layers on rigid materials.
Photolithography and etching techniques form The desired circuit board pattern on the outer layer.
Lamination process:
Laminates the flexible and rigid material to form a rigid-flex circuit board.
Ensures a tight fit between layers without air bubbles or gaps.
Drilling and Through-Hole Plating:
Drill holes in the rigid-flex circuit board to create connections between the layers.
Plating of the drilled holes creates conductive pathways.
Surface Preparation and Soldermask Fabrication:
Surface treatments are applied to the circuit board to improve its conductivity and corrosion resistance.
Solder mask is produced at locations where soldering is required to protect the circuit from erosion by substances such as solder.
Screen Printing Characters and Markings:
Silkscreen necessary characters, symbols, or markings on circuit boards to facilitate identification and assembly.
Testing & Inspection:
Performs electrical performance tests on rigid-flex circuit boards to ensure proper operation.
Perform appearance inspection and dimensional measurements to ensure compliance with design requirements.
Packaging & Shipping: Package qualified rigid-flex circuit boards to prevent damage during transportation and storage. Make shipment arrangements according to customer requirements.
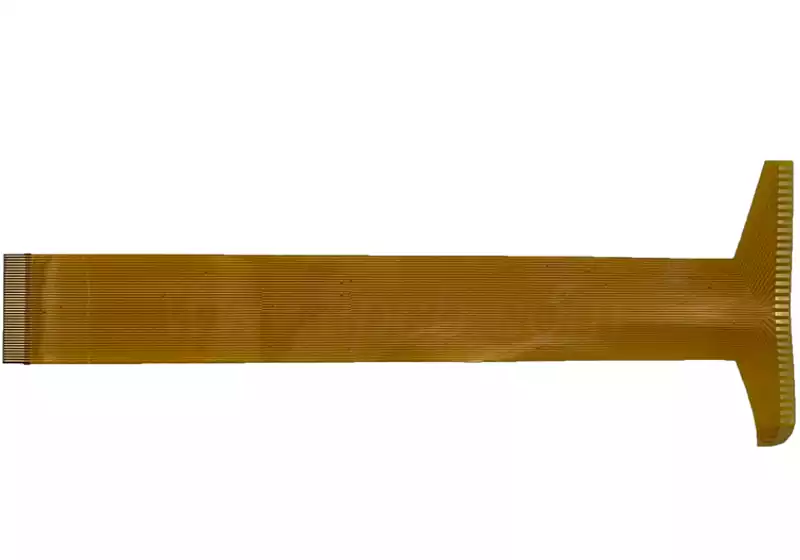
Rigid Flex Printed Circuit Boards have the following advantages:
Thin and flexible: lightweight, small size, can be folded, bent, and curled, easy to process, bending, easy to three-dimensional combination.
Cost-effective: low cost, suitable for mass production.
Excellent electrical properties and heat resistance: Flexible printed circuit boards use a flexible substrate instead of the traditional rigid substrate, with good electrical and dielectric properties and heat resistance.
High assembly reliability and assembly operability: Reduced hardware required for internal connections improves assembly reliability and quality.
Good heat dissipation: allows for three-dimensional connection and mounting, increasing the freedom of electrical and mechanical design.
Favorable thermal diffusion: Favorable thermal diffusion improves system reliability.
Disadvantages:
High one-time initial cost: Since flex pcb is designed and manufactured for special applications, the initial cost required for circuit design, wiring and photographic backing is high.
Difficulty in making changes: Once made, changes must begin with the base map and preparation of the photolithography program, so changes are not easy to make. The surface of the printed circuit board is covered with a protective film, which needs to be removed before repair and restored after repair, making this process more difficult.
Size constraints: Because of the wide variety of specifications of flexible printed circuit boards, generally used in intermittent process manufacturing, and therefore subject to production conditions, can not prepare large-size flexible printed circuit boards.
Easily damaged during assembly: Due to its small size and lightweight, it is easily damaged during assembly.
Rigid-flex printed circuit boards are used in a wide range of application scenarios:
Mobile devices: smartphones, tablet PCs, and other mobile devices that require lightweight, flexible circuit boards.
Medical devices: various medical monitoring instruments, medical probes, surgical machinery, and other medical devices that require bending, winding, and folding.
Vehicle electronics: automobiles, airplanes, ships, and other carriers of the circuit board must meet the extreme temperature and vibration with the carrier changes, flexible printed circuit boards can reduce the mechanical role, and improve system reliability.
Wearable Devices: Various wearable electronic devices, fitness monitors, etc. require flexible and comfortable circuit boards.
Aerospace: Rigid-flex printed circuit boards are also used in aerospace applications.
Automotive Electronics: Rigid-flex PCBs are also widely used in automotive electronics.
Rigid flex pcb occupies an important position in the electronics industry with its unique properties and wide range of applications. In the future, with the continuous progress of technology and growing demand for applications, it is expected to be more widely used and more in-depth research.