SMT = Surface Mount Technology, SMT is currently the most popular technology and process in the electronic assembly industry. The electronic manufacturing industry is experiencing rapid development. SMT assembly, as the core technology of this transformation, is leading electronic manufacturing towards a new future.
SMT assembly is a technology that directly installs electronic components on the surface of printed circuit boards (PCBs). It achieves high-density, miniaturized, and lightweight electronic product assembly by fixing components onto PCBs using adhesives or welding materials. Compared with traditional manual welding, SMT technology has higher assembly density and reliability, making it widely used in the electronic manufacturing industry.
SMT assembly technology has a wide range of applications in various fields such as communication, healthcare, aerospace, and automotive electronics. With the continuous miniaturization of electronic products and the development towards lightweight and highly integrated direction, the application of SMT assembly is also expanding. Nowadays, almost all electronic products are assembled using SMT technology.
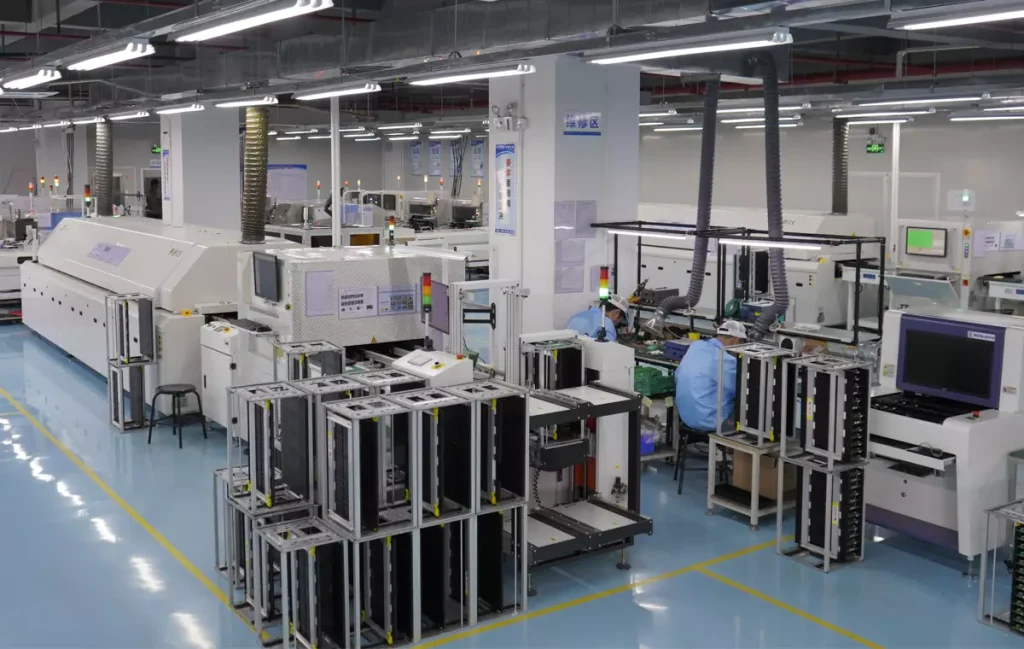
Compared with traditional through-hole insertion technology, SMT has the characteristics of higher assembly density, smaller volume and weight, faster production efficiency, and lower cost. The following are the advantages:
High density and miniaturization: SMT technology can achieve smaller component installation, improve assembly density, and make electronic products more miniaturized.
High reliability: It has higher reliability because components are achieved through precise positioning and bonding, rather than traditional welding.
High productivity: The use of automated equipment can greatly improve productivity and shorten time to market.
Low cost: Due to the ability of SMT technology to achieve high-density and high reliability assembly, it can significantly reduce production costs in large-scale production.
Environmental protection: SMT technology does not require the use of solder, making it more environmentally friendly and in line with the green development trend of modern manufacturing industry.
The process of SMT assembly
Printing (red glue/solder paste) ->Inspection (optional AOI fully automatic or visual inspection) ->Installation (first attach small components and then attach large components: divided into high-speed SMT and integrated circuit mounting) ->Inspection (optional AOI optical/visual inspection) ->Welding (using hot air reflow soldering for welding) ->Inspection (can be divided into AOI optical inspection for appearance and functional testing) ->Maintenance (using tools such as soldering stations and hot air desoldering stations) ->Splitting (manually or using a slitting machine for cutting)
The process of SMT flow is simplified as follows: printing ->SMT ->welding ->maintenance (each process can include a testing step to control quality)
Solder paste printing: Solder paste is a paste made by mixing solder powder with a paste solder that has soldering function. Usually, solder powder accounts for about 90%, while the rest is composed of chemical components. The function of solder paste printing is to imprint the solder paste at a 45 degree angle onto the solder pads of the PCB with a scraper, preparing for the soldering of components. The equipment used is a printing machine (solder paste printing machine), located at the forefront of the SMT production line.
Part mounting: Its function is to accurately install surface mounted components onto the fixed position of the PCB. The equipment used is the SMT mounting machine, located behind the printing machine in the SMT production line. It is generally used in combination with high-speed machines and general-purpose machines according to production needs.
Reflow soldering: A circuit assembly technique that involves soldering and assembling using methods such as reflow soldering or immersion soldering. The function of reflow soldering is to melt the solder paste and firmly solder the surface assembled components to the PCB. The equipment used is a reflow soldering furnace, located behind the SMT production line’s SMT mounting machine. The temperature requirements are quite strict and real-time temperature measurement is required. The measured temperature is reflected in the form of a profile.
Wave soldering: The most commonly used solder for wave soldering is eutectic tin lead alloy: tin 63%; Lead is 37%, and the temperature of the solder in the solder pot should be controlled at all times. The temperature should be 183 ℃ higher than the temperature of the alloy liquid, and the temperature should be uniform. In the past, a soldering pot temperature of 250 ℃ was considered standard. In the peak welding process, the peak is the core. Preheated, flux coated, and dirt free metal can be transported to the welding workstation via a conveyor belt to come into contact with solder at a certain temperature, and then heated. This way, the solder will undergo a chemical reaction, and the solder alloy will form an interconnection through peak force.
AOI optical inspection: Its function is to detect the welding quality of the soldered PCB. The equipment used is an automatic optical inspection machine (AOI), which can be configured in a suitable location on the production line according to the needs of the inspection. Some are before reflow soldering, while others are after reflow soldering.
NG repair: Its function is to repair the PCB that has been detected as faulty. The tools used are soldering iron, repair workstation, etc. Configure after AOI optical detection.
Splitting: Its function is to cut multiple PCBA boards into individual pieces, usually using V-cut and machine cutting methods.
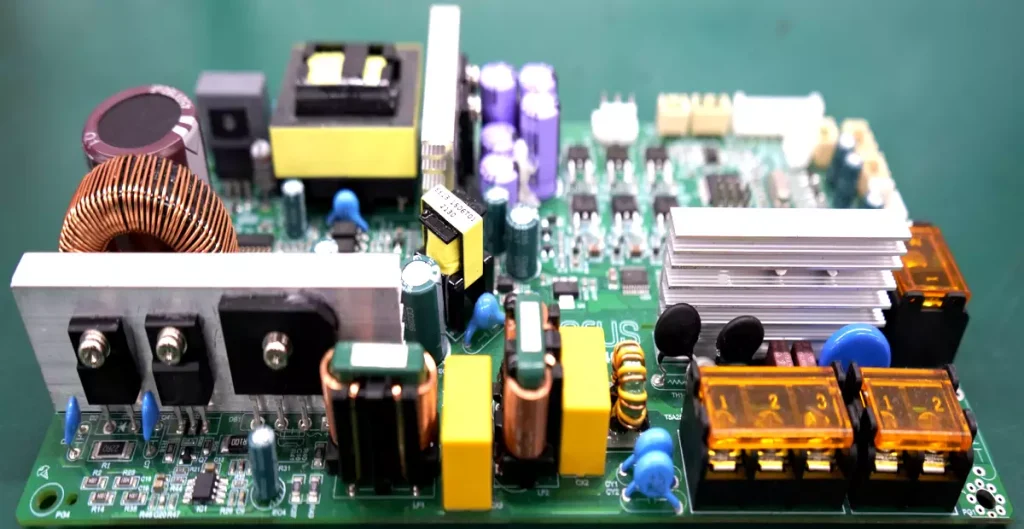
The SMT assembly process is closely related to every process step before welding, including investment in funds, PCB design, component solderability, assembly operations, flux selection, temperature/time control, solder and crystal structure, etc.
SMT is widely used in various electronic products such as mobile phones, computers, tablets, automotive electronics, medical devices, etc. With the advancement of technology and changes in market demand, SMT technology is also constantly developing and innovating. For example, SMT technology, high-precision mounting technology, and lead-free soldering technology for flexible circuit boards (FPCs) are current research hotspots and development trends. These new technologies will help further improve the production efficiency and quality of SMT, and promote the development of the electronic manufacturing industry.
SMT assembly as an advanced electronic manufacturing technology, has advantages such as high density, miniaturization, high reliability, high productivity, low cost, and environmental protection. With the continuous development of science and technology, it is believed that it will play a more important role in the future electronic manufacturing industry.