What is an AOI?AOI, or Automated Optical Inspection, is a device based on optical principles to detect common defects encountered in welding production. It is a newly emerging, but rapidly growing, new testing technology. When automatic inspection is performed, the machine automatically scans the PCB with a camera, captures images, compares the tested solder joints with the qualified parameters in the database, and after image processing, checks for defects on the PCB and displays/labels the defects through a monitor or an automatic sign for repairers to fix.
AOI technology can detect many types of defects, such as missing parts, wrong parts, offsets, standing monuments, bridging, false soldering and so on. These defects, if not detected and dealt with in time, may lead to unstable board performance or even cause failures. Therefore, AOI technology has an important application value in SMT processing.
The working principle of AOI (Automatic Optical Inspection) is mainly based on machine vision technology , which realizes efficient and accurate inspection by simulating the manual inspection process. The operation process is as follows.
Image Acquisition.AOI equipment uses a camera to acquire images of the object to be inspected, such as component locations, markings, solder joints, etc. on the PCB . This process requires the camera to have high resolution in order to capture subtle defects.
Image processing and analysis. The captured images are processed by specialized algorithms that are used to analyze the features in the images, such as component position, rotation angle, solder joint quality, etc. These algorithms are able to detect and quantify these features for comparison with predetermined criteria.
Comparison and Determination. the AOI equipment compares the captured image data to predetermined standards or specifications to determine if there are any non-conforming components or soldering issues. Any out-of-specification issues are logged and alarms are triggered.
Feedback and Repair. Once a problem is detected, the AOI can automatically shut down, alert the operator to perform a manual inspection or repair, thus minimizing the generation of nonconforming products.
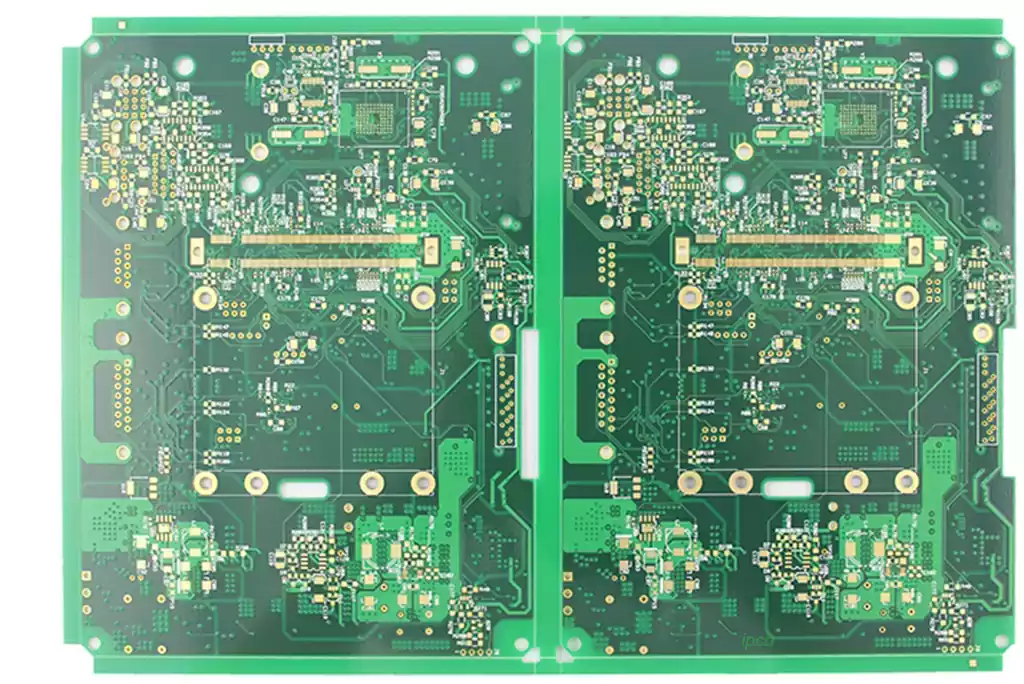
Application Scope of AOI
AOI equipment is widely used in all stages of SMT processing, including:
a. Placement stage: In the component placement stage, AOI equipment can check whether the position, polarity and rotation angle of the components are correct to ensure that they are correctly attached to the PCB.
b. Soldering Stage: AOI equipment is also used in the soldering stage to check the quality of the solder joints, including the integrity of the solder, the amount of solder, and solder defects.
c. Final Inspection Stage: Finally, AOI equipment is usually used in the final inspection stage to ensure the quality of the entire PCBA board, including the correct position of components, polarity, solder quality, and the absence of other potential problems.
In PCBA chip processing, AOI technology is mainly used in the following aspects:
- Pre-soldering inspection: Before soldering, AOI technology can inspect the pins and pads of components to ensure that their size, shape, etc. comply with the design requirements, to avoid soldering defects caused by bad pins or pads.
- Post-soldering inspection: After the welding is completed, AOI technology can inspect the solder joints to identify whether there are defects such as false soldering, fake soldering, cold soldering, etc., and feedback the defective information to the operator for timely repair.
- Process monitoring: In the production process, AOI technology can monitor the welding quality in real time, and discover and deal with potential quality problems in time. This not only improves product quality, but also reduces rework and scrap rates and production costs.
AOI technology plays a pivotal role in the field of SMT processing with its efficient and accurate detection capability. Whether it is component positioning inspection at the placement stage, solder joint quality assessment at the soldering stage, or even total quality inspection at the final inspection stage, it can provide reliable solutions.