Copper black pcb is high-performance pcb circuit characterised by a black surface, consisting of a copper layer, a substrate and a surface treatment layer.
The copper layer of the PCB is susceptible to oxidation when exposed to the air without the application of soldermask, and both sides of the PCB circuits are covered with a copper layer that is smooth and unprotected, whether it is prepared by additive or subtractive methods.
Although the chemical activity of copper compared to aluminium, iron, magnesium and other metals is slightly inferior, but in the presence of moisture in the environment, pure copper once in contact with oxygen, it is very easy to oxidation reaction. Given that the air is always filled with oxygen and water vapour, pure copper surface in the air after exposure, will quickly trigger the oxidation process.
Given that the thickness of the copper layer in the PCB circuit is very thin, once the copper oxidation occurs, its conductivity will be greatly reduced, which in turn will have a serious impact on the electrical performance of the entire PCB circuit.
In order to effectively curb the oxidation process of copper, and to ensure that the circut board in the soldering process of the soldering and non-soldering areas can be clearly distinguished, and to further protect the PCB surface layer, engineers have developed a unique coating. This coating can be easily applied to the surface of the PCB circuit and forms a protective barrier with a corresponding thickness, effectively isolating the copper from the air. This coating is known as the soldermask, and its preparation material is soldermask paint.
Since it is called paint, there are naturally a variety of colour options. In fact, the original soldermask can be made colorless and transparent, but for the convenience of PCB manufacturing, maintenance and sales considerations, it is often necessary to print fine text information on the board surface. Transparent soldermask can only show the base colour of the PCB, which is not aesthetically pleasing to the eye in manufacturing, maintenance and sales. Therefore, engineers have incorporated a variety of colours into the soldermask to create circut boards in different colours such as black, red or blue.
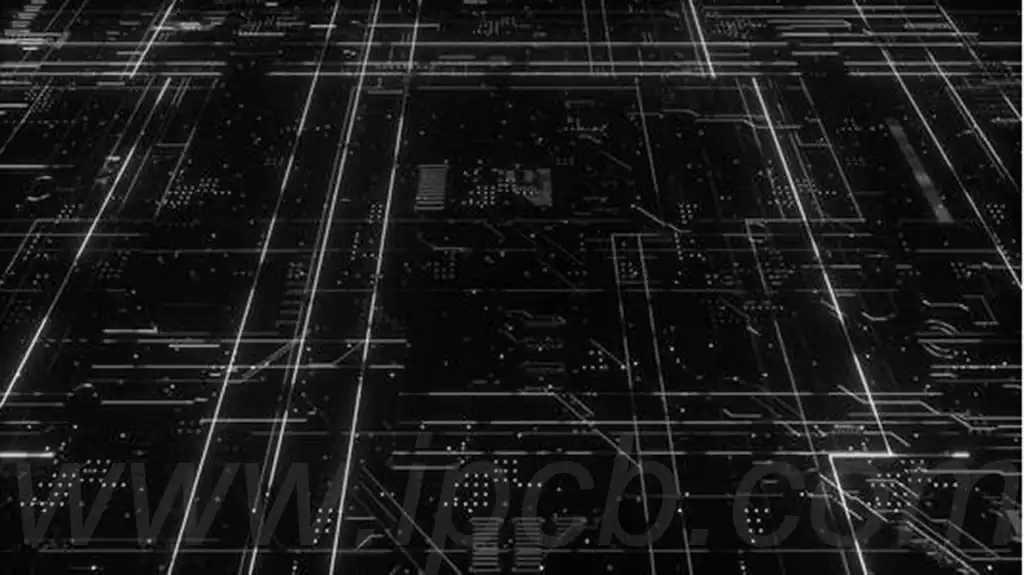
Differences between PCB circuit board of different colours
Process Complexity
Copper black pcb manufacturing: The manufacturing process for copper black pcb is challenging. Due to the highly light-absorbing properties of black dyes, the process is often challenged by insufficient light during the production process, especially during the exposure and development phases. This can lead to problems such as blurring of the circuit pattern and reduced alignment of the soldermask to the circuit, which in turn increases the defect rate. For this reason, copper black pcb are mostly found in high-end products, and their manufacturing requires a higher level of technology and more sophisticated process control, and the cost has also risen.
Green circuit board (PCB) manufacturing: In contrast, the green PCB manufacturing process is more mature and stable. Green dyes in the light absorption and reflection of balanced performance, so that the exposure and development and other steps easier to control, lower defective rate, process difficulty is relatively low, thus reducing production costs. Therefore, green PCBs are widely used in the large-scale production of various electronic products.
Thermal Performance
Copper black pcb: From a theoretical perspective, black objects are strong in the absorption and emission of thermal radiation. However, in practical PCB applications, the thermal performance of copper black pcb does not significantly exceed that of printed circuit board of other colours, because the heat dissipation of printed wiring board depends on the layout of the copper clad lines, the design of the metal heat dissipation layer, and external means of heat exchange such as air convection, thermal conductive silicone, and other means of heat dissipation, and is not purely dependent on the colour factor.
Metallic-coloured circuit boards (e.g. silver): Some PCB boards with metallic colours, such as silver, may have an advantage in terms of thermal efficiency. This is due to the fact that they are usually constructed with a metal coating or metal substrate. The metal itself, due to its excellent thermal conductivity, is able to conduct heat away from the PCB circuit more efficiently, thus improving the thermal efficiency of the entire PCB board.
Maintainability
Green Circuit Board (PCB): Green PCB is easier to observe and identify component markings, line paths, etc. during maintenance operations due to its light colour. This allows maintenance personnel to have a clearer view of all components on the circuit board, making it easier to perform tasks such as fault detection and component replacement, which in turn improves the efficiency and accuracy of maintenance.
Copper black pcb:it present a greater challenge when it comes to maintenance. Their dark colour makes component and circuit markings difficult to identify, especially in low-light environments, and maintenance personnel need to look more closely and use specialised lighting equipment to carry out maintenance work, which undoubtedly prolongs the maintenance time and makes it more difficult.
Copper black pcb plays a vital role in electronic products due to their distinctive black appearance and high performance. However, the manufacturing process of copper black pcb is relatively complex and technically demanding, and the defective rate may increase due to the difficulty of the process, resulting in relatively high costs.
Although copper black pcb does not exhibit significant advantages in terms of thermal efficiency, their unique visual effect and application in certain high-end products still make them attractive in the market. In the future, with the continuous development of technology and the continuous expansion of application areas, it is expected to show its unique advantages and value in more areas.