Introduction: In recent years, the electronics manufacturing industry has witnessed a profound transformation driven by the growing emphasis on environmental sustainability and regulatory compliance. One of the key developments in this evolution is the widespread adoption of lead-free assembly processes in Printed Circuit Board (PCB) manufacturing. This article explores the significance, challenges, and advancements associated with lead-free assembly, shedding light on its pivotal role in shaping a greener and safer future for the industry.
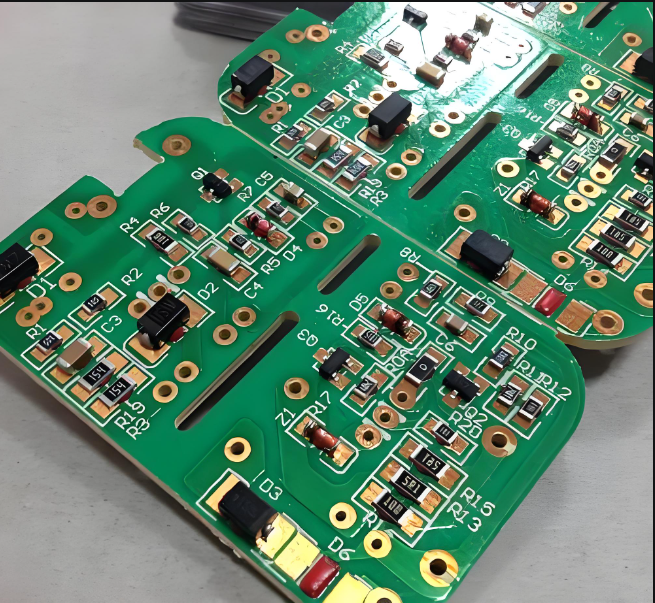
The Environmental Imperative: The transition to lead-free assembly is driven by an urgent need to mitigate the environmental impact of electronic waste. Lead, a common component in traditional soldering materials, poses significant risks to ecosystems and human health. Recognizing these risks, regulatory bodies worldwide have imposed restrictions on the use of lead in electronic products. The Restriction of Hazardous Substances (RoHS) directive in the European Union is a prime example of legislation aimed at reducing the environmental footprint of electronics manufacturing.
Understanding Lead-Free Assembly: Lead-free assembly involves the substitution of lead-based solder materials with alternative alloys that comply with regulatory standards. Commonly used lead-free solder alloys include tin-silver-copper (SnAgCu), tin-silver (SnAg), and tin-copper (SnCu). These alloys offer comparable mechanical and electrical properties to traditional lead-based solders while meeting environmental requirements. The transition to lead-free assembly requires adjustments in equipment, processes, and quality control measures. Manufacturers invest in research and development to optimize lead-free solder formulations and ensure compatibility with existing production technologies.
Health and Safety Considerations: In addition to environmental benefits, lead-free assembly prioritizes the health and safety of manufacturing personnel. Exposure to lead can lead to severe health complications, including neurological disorders and reproductive issues. By eliminating lead from the production environment, manufacturers create safer workplaces and uphold their duty of care towards employees.
Challenges and Solutions: The transition to lead-free assembly presents a range of challenges that require innovative solutions. One of the primary challenges is the higher processing temperatures associated with lead-free soldering, which can impact the thermal stress on electronic components and substrates. To address this issue, manufacturers employ advanced thermal management techniques and optimize material selection to ensure product reliability and longevity. Furthermore, lead-free assembly may require adjustments in equipment and process parameters to achieve optimal results. Manufacturers collaborate with suppliers and industry partners to develop best practices and overcome technical barriers associated with the transition.
Technological Advancements: The adoption of lead-free assembly has spurred technological advancements in soldering materials, equipment, and processes. Researchers and manufacturers collaborate to develop novel solder formulations with improved properties such as wetting behavior, solder joint strength, and resistance to thermal cycling. Additionally, advancements in soldering equipment and techniques enhance process efficiency, yield, and quality control. Automated optical inspection (AOI) systems and X-ray inspection technologies enable manufacturers to detect defects and ensure the reliability of lead-free solder joints. Furthermore, advances in surface mount technology (SMT) and through-hole assembly processes facilitate the integration of lead-free components into PCBs with high precision and reliability.
Economic Considerations: While the transition to lead-free assembly involves upfront costs and technical challenges, it also presents economic opportunities for manufacturers. By embracing lead-free assembly, companies can enhance their competitiveness in the global marketplace and gain access to new markets with stringent environmental regulations. Additionally, the adoption of lead-free assembly can drive innovation and differentiation, enabling manufacturers to offer environmentally sustainable products that meet the evolving needs of customers. Furthermore, the shift towards lead-free assembly aligns with corporate sustainability goals and enhances brand reputation, contributing to long-term business success.
Future Trends and Outlook: Looking ahead, the future of lead-free assembly is shaped by ongoing advancements in materials science, manufacturing technologies, and regulatory frameworks. Manufacturers continue to innovate and optimize lead-free assembly processes to improve product performance, reliability, and cost-effectiveness. Furthermore, the emergence of Industry 4.0 technologies, such as artificial intelligence (AI), internet of things (IoT), and big data analytics, promises to revolutionize electronics manufacturing and accelerate the adoption of lead-free assembly. By harnessing the power of digitalization and automation, manufacturers can achieve greater efficiency, flexibility, and sustainability in their operations.
Conclusion: In conclusion, lead-free assembly represents a transformative shift in PCB manufacturing towards environmental sustainability and human well-being. By embracing lead-free soldering materials and processes, manufacturers uphold their commitment to responsible production practices and contribute to a cleaner, safer, and more sustainable future for generations to come. Despite the challenges posed by the transition, the benefits of lead-free assembly far outweigh the costs, positioning it as a cornerstone of sustainable electronics manufacturing in the 21st century. As the industry continues to evolve and innovate, lead-free assembly will remain a driving force for positive change, shaping the future of electronics manufacturing in a rapidly changing world.