The temperature to melt solder is the point at which the solder changes from a solid to a liquid during the heating process. The selection of this temperature point needs to take into account a number of factors, including the nature of the material to be soldered, the soldering environment, and the requirements of the soldering process. The appropriate solder melting temperature can ensure that the solder in the welding process can fully flow, fill the welding gap, the formation of a strong welded joint.
The most commonly used solder, solder wire, solder bar, is made of tin and lead two metals, according to a certain proportion of the fusion of tin-lead alloy, of which tin is the main material, so people call it “solder”.
Tin (Sn), is silver-white, shiny, ductile, brittle, in the air is not easy to oxidize the metal, melting point of 232 ℃.
Because pure tin, brittle, and can be fused with most metals to form alloys, so in order to make tin-based solder with toughness, while lowering the melting point, must be fused with another metal to improve the soldering performance of tin solder.
Lead (Pb), a greenish-gray, soft, dense, ductile, toxic, and easily oxidized metal in air, has a melting point of 327 degrees Celsius.
However, Pb is a good additive to tin solder, and when melted and mixed with tin in a proportionate manner, the commonly used ‘leaded solder’ is obtained.
This ‘leaded tin solder’, the melting point becomes low, conducive to low-temperature soldering, can be easily combined with most of the metal (i.e.: easy on the solder), and the price is low, good conductivity, reliable solder joints.
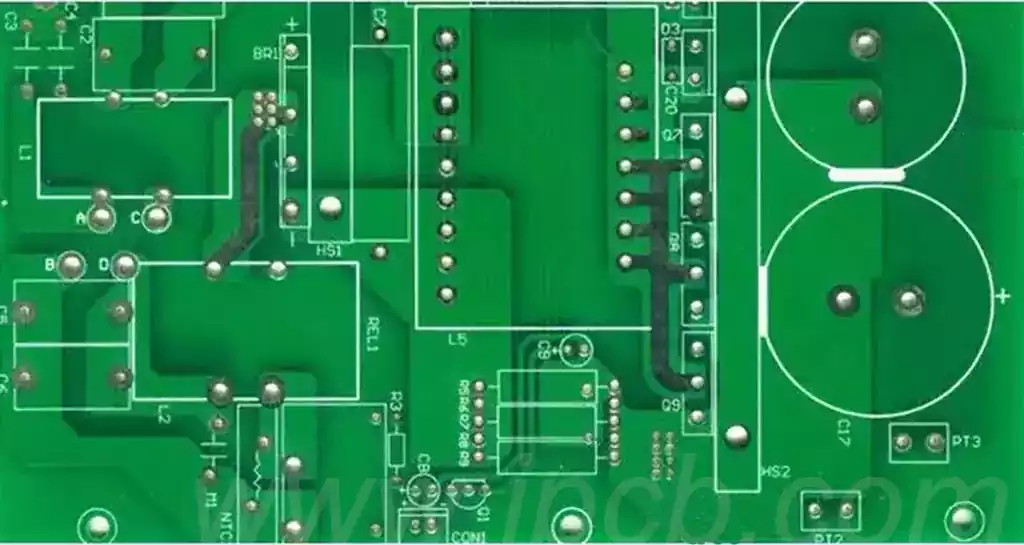
The relationship between the composition and melting point of tin solder
Tin solder, tin and lead in different proportions, the melting temperature is different, but its melting temperature is always lower than the composition of the alloy of any one of the pure metal melting temperature.
For different soldered parts and soldering environments, it is necessary to select solder with different melting temperatures and use suitable soldering methods.
Appropriate operating temperatures for various types of soldering work:
Normal melting point of solder wire: 183°C – 215°C (approx. 361°F – 419°F)
Normal operating temperature: 270°C – 320°C (approx. 518°F – 608°F)
Production line operating temperature: 300℃ – 380℃ (approx. 572℉ – 716℉)
Suction working temperature (small solder joints): 315°C (approx. 600°F)
Suction working temperature (large solder joints): 400°C (approx. 752°F)
The choice of solder melting temperature has an important effect on solder quality. If the solder melting temperature is too low, the solder may not be able to melt sufficiently, resulting in a weak soldered joint, which is prone to problems such as false soldering and cold soldering. While the solder melting temperature is too high, it may lead to excessive heat generated during the welding process, causing thermal damage to electronic components, and even cause fire and other safety accidents. Therefore, choosing the proper solder melting temperature is crucial to ensure the quality of soldering.
The temperature to melt solder as a core element in the electronic manufacturing process, its selection not only about the quality of soldering, but also directly affect the production efficiency and safety. Choose the right temperature, not only to ensure that the solder can fully flow, fill the welding gap, the formation of a solid welded joints, but also to avoid too high a temperature on the electronic components caused by thermal damage.