With the rapid development of electronic technology, more and more industries have continuously increased their requirements for product quality, especially in the production process of electronic products.
How to test efficiently and accurately has become a major challenge for technicians. In order to meet this demand, custom test fixtures have gradually become one of the indispensable and important tools in the electronic manufacturing industry. This article will explore the concept, application and future development direction of customized test fixtures to help readers better understand the advantages and value of this technology.
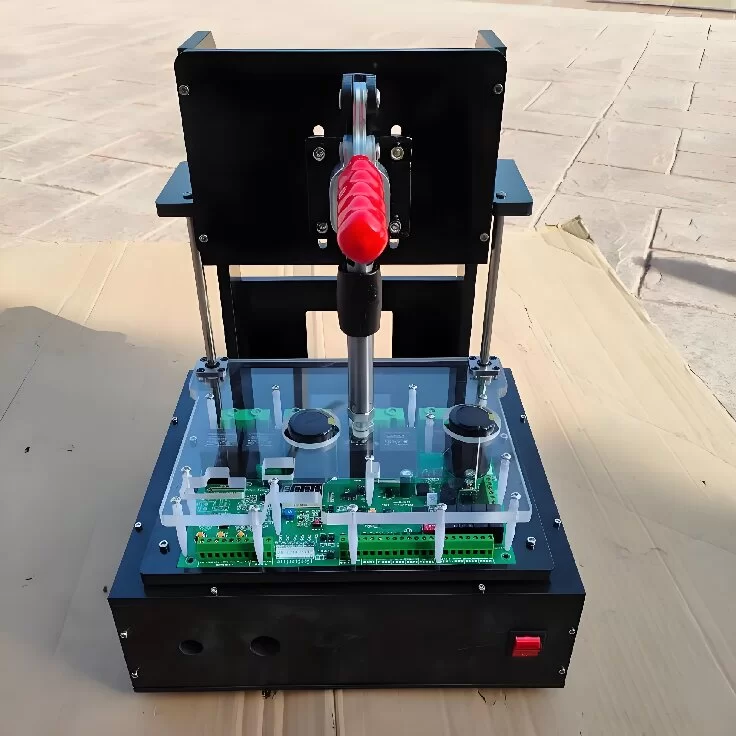
Definition and function of customized test fixtures
Customized test fixtures refer to a test tool specially designed and manufactured according to the special requirements of customer products. It is mainly used in the assembly, testing, and maintenance of electronic products. It can ensure the accuracy of various indicators of the product during the production process and avoid the emergence of unqualified products into the market. The design of the test fixture usually needs to be combined with the specific structure, function and production process of the tested product to ensure that it can operate efficiently and has high accuracy and stability.
The role of customized test fixtures:
Improve test efficiency: Through customized design, the test fixture can work closely with the automated equipment on the production line, greatly improving the speed and efficiency of the test.
Ensure test accuracy: The test fixture is designed according to the characteristics of the product, which can reduce human operation errors and improve the accuracy of the test results.
Reduce production costs: Through efficient testing processes, the defective rate of products can be reduced, thereby reducing rework costs and scrap rates.
Improve product quality: Ensure that each batch of products undergoes rigorous testing, improve the overall quality of products, and enhance market competitiveness.
Design principles for customized test fixtures
The design of customized test fixtures is not only to meet production needs, but also to take into account the diversity and complexity of products. Multiple factors need to be considered during the design process to ensure that the fixture can complete the test task efficiently and accurately. The following are several key principles for the design of customized test fixtures:
Strong adaptability: The design of the test fixture must be able to adapt to products of different specifications and models. With the continuous upgrading of electronic products, the test fixture needs to have a certain degree of flexibility to meet the testing needs of different products.
Easy to use: Although the test fixture usually needs to be customized according to the special requirements of the customer, the convenience of operation should be taken into account during the design, so that the operator can quickly master the use method and reduce the complexity of the operation.
High precision and stability: The test fixture must have high precision to ensure accuracy during the test process. In addition, the fixture should have strong stability during long-term use to avoid friction, aging and other factors affecting the test results.
Durability: Test fixtures are generally used for a long time, so their materials and manufacturing processes need to have strong durability. Common test fixture materials include aluminum alloy, stainless steel, and high-strength plastics, which have strong wear and corrosion resistance.
Comply with safety requirements: The design of the test fixture needs to comply with relevant safety standards to avoid safety accidents during operation. In addition, the fixture itself should also avoid any damage to the product under test.
Application areas of customized test fixtures
Customized test fixtures are widely used in many fields, especially in the electronics industry, automotive industry, and medical equipment industries, where their importance is becoming more and more prominent. The following are several major application areas:
Electronic industry: In the production process of electronic products, test fixtures are widely used in the welding, assembly, and functional testing of circuit boards. For example, in the testing of PCB boards, customized test fixtures can ensure that each component on the circuit board can be accurately tested to avoid functional failures caused by improper testing.
Automotive industry: In the process of automobile manufacturing, test fixtures are used to check the assembly accuracy of automotive parts and the function of electrical systems. Customized test fixtures can ensure the normal operation of various functions of automotive electronic systems during the production process.
Medical equipment: The production of medical equipment requires extremely high precision and reliability. Customized test fixtures can not only ensure product functions, but also meet the strict requirements of the medical industry for hygiene and safety.
Consumer electronics: In the production process of consumer electronic products such as smartphones, TVs, and home appliances, test fixtures can efficiently complete functional testing, performance testing, and durability testing to ensure that each product meets the predetermined quality standards.
Communications industry: With the rise of emerging technologies such as 5G and the Internet of Things, the demand for testing communication equipment is also increasing. Customized test fixtures can ensure that these high-precision and high-complexity communication devices are accurately tested during the production process.
Manufacturing process of customized test fixtures
The manufacturing process of customized test fixtures usually includes several links such as design, material selection, processing, and assembly. Each link requires fine operation to ensure that the test fixture can complete the task efficiently and accurately. The following are the main manufacturing processes of test fixtures:
Design stage: The design stage is the most critical step in the manufacturing process of test fixtures. Designers need to communicate closely with customers to understand the specific requirements of the product, and design a fixture that meets the requirements according to the size, shape, function and other characteristics of the tested product. During the design process, the application of computer-aided design (CAD) technology makes the design scheme more intuitive and accurate.
Material selection: The material selection of the test fixture is very important. It is necessary to consider the cost issue and ensure that the material can meet the strength, durability and precision requirements of the fixture. Commonly used materials include aluminum alloy, steel, stainless steel, plastic, etc.
Processing technology: Processing technology includes machining, injection molding, 3D printing and other methods. For fixtures with complex shapes, rapid prototyping can be carried out through 3D printing technology to reduce the development cycle. For fixtures with higher precision requirements, CNC machine tools are usually used for processing to ensure the accuracy of the fixture.
Assembly and debugging: After processing, the fixture needs to be assembled to ensure the matching accuracy between the components. After assembly, debugging is also required to ensure that the fixture can be used normally in actual work.
Challenges and development direction of customized test fixtures
Although customized test fixtures have significant advantages in improving production efficiency and ensuring product quality, they still face some challenges in practical applications. First, with the diversification of products, the design and manufacture of test fixtures require higher flexibility. How to quickly respond to the needs of different customers has become a problem that test fixture manufacturers need to solve.
Secondly, with the increase in product complexity, the accuracy requirements of test fixtures are also getting higher and higher. How to improve the accuracy and stability of fixtures while ensuring cost control is an important challenge facing the current industry.
In the future, the design and manufacture of customized test fixtures will develop in the direction of intelligence, automation and modularization. By introducing advanced technologies such as the Internet of Things and artificial intelligence, test fixtures can realize functions such as remote monitoring and automatic adjustment to improve test efficiency and accuracy. In addition, with the continuous maturity of 3D printing technology, the manufacturing cost and production cycle of customized test fixtures will also be greatly shortened, and more flexible and efficient services will be provided to customers in the future.
Application of customized test fixtures in future intelligent production
With the advancement of Industry 4.0 and the development of intelligent manufacturing technology, the application of customized test fixtures is also gradually developing in the direction of intelligence. Traditional test fixtures usually rely on manual operation and manual adjustment, which are relatively inefficient and easily affected by human factors. With the continuous advancement of automation and digitalization technology, intelligent test fixtures have gradually become a trend in the development of the industry. The following are the applications of customized test fixtures in intelligent production:
Automation function integration: Intelligent test fixtures can be deeply integrated with automated equipment on the production line (such as robots, automatic feeding systems), reducing the intervention of manual operations and improving the automation level of the production line. Automated test fixtures can autonomously identify products and automatically adjust the fixture position according to their specifications to complete accurate testing of products.
Data acquisition and analysis: Intelligent test fixtures record test data in real time through built-in sensors and data acquisition systems, and transmit data to the cloud or local database for analysis. These data can not only be used for real-time feedback of test results, but also provide decision support for production optimization, such as predicting equipment failures, analyzing production bottlenecks, and optimizing process flows.
Adaptive adjustment function: As product size and shape continue to change, traditional test fixtures usually require frequent manual adjustment. The intelligent test fixture has an adaptive adjustment function, which can automatically adjust the test parameters or the working state of the fixture according to the characteristics of different products, improving adaptability and flexibility.
Remote monitoring and maintenance: The intelligent test fixture can realize remote monitoring and diagnosis through the Internet, and the production management personnel can grasp the status of the test equipment in real time, and find and eliminate faults in time. In addition, remote monitoring can also help enterprises to remotely maintain and optimize the equipment, avoiding the risk of production suspension caused by equipment failure.
Application of customized test fixtures in different production stages
Customized test fixtures not only play an important role in the final testing stage of the product, but also are widely used in various links such as product design, production, assembly, and inspection. The following are the specific applications of customized test fixtures in different production stages:
Product design stage: In the research and development stage of the product, the test fixture is usually used as a verification tool to ensure the feasibility of the design. Through close cooperation with the design team, the test fixture can help engineers evaluate the rationality, manufacturability and test feasibility of the design scheme, laying the foundation for subsequent production.
Production process verification stage: In the production process verification stage, the test fixture is an important tool for trial production, which can ensure that all products meet the design requirements in the initial production process. Through the use of test fixtures, manufacturers can detect possible deviations in the production process and optimize the production process in time.
Production process monitoring stage: In the large-scale production process, test fixtures are used to comprehensively monitor each batch of products. It can quickly identify unqualified products in the production process and adjust the production process in time to ensure the quality of the final product.
Quality control stage: Customized test fixtures play a particularly prominent role in the quality control stage. By accurately measuring each indicator in the production process, test fixtures help companies ensure that every detail of the product meets the standards and improves the overall product quality.
Maintenance and service stage: Even products that have been delivered for use require regular maintenance and overhaul. Customized test fixtures can also provide effective support in the maintenance and service stage of the product. By using test fixtures, maintenance personnel can quickly diagnose the cause of the fault and repair it, thereby improving the maintenance efficiency of the equipment.
Cost management and optimization of customized test fixtures
In the production process, customized test fixtures are often one of the larger parts of the company’s investment. Therefore, how to optimize the design and manufacturing cost of test fixtures while ensuring the test quality has become a focus of many companies. Here are some strategies for cost optimization:
Modular design: By adopting modular design, companies can flexibly choose different module combinations according to the test requirements of different products, avoiding the need to redesign the entire fixture for each customization. This not only saves design costs, but also improves the versatility of the fixture and reduces manufacturing and maintenance costs in long-term production.
Use of standardized parts: In the manufacturing process of the fixture, the use of some standardized parts can greatly reduce production costs. Standardized parts usually have lower procurement costs and higher availability, which helps to reduce the overall cost of customized fixtures.
Lean production method: By implementing the lean production concept, companies can reduce waste and improve production efficiency in the process of designing and manufacturing test fixtures. For example, by analyzing the time consumption and resource usage of each link, process optimization can be carried out to reduce production costs.
Long-term cooperation and supply chain optimization: Establishing a long-term and stable cooperative relationship with professional test fixture manufacturers can obtain more favorable prices in mass production. At the same time, optimizing supply chain management, reducing material waste and inventory backlogs can also effectively control the cost of test fixtures.
Technological innovation: With the continuous advancement of manufacturing technology, some emerging production methods and materials are gradually being applied to the manufacture of test fixtures. For example, the use of 3D printing technology to manufacture test fixtures with complex shapes can greatly reduce the cost of mold manufacturing and production.
Sustainable development of customized test fixtures
With the continuous improvement of global environmental protection requirements, the sustainable development of customized test fixtures has also attracted the attention of more and more companies. In order to achieve green manufacturing, the design and production of test fixtures need to focus on the following aspects:
Use of environmentally friendly materials: The manufacturing materials of test fixtures need to select environmentally friendly and recyclable materials. With the research and development and application of sustainable materials, more and more test fixtures use non-toxic and pollution-free materials, reducing the negative impact on the environment.
Energy saving and consumption reduction: In the manufacturing process, by optimizing the process and improving the efficiency of equipment use, reducing energy consumption and reducing carbon emissions in the production process, it meets the requirements of green manufacturing.
Product life cycle management: The life cycle management of customized test fixtures is very important. By monitoring the use of fixtures, timely repairs and upgrades, and extending their service life, it reduces resource waste.
Waste treatment and recycling: With the strict implementation of environmental protection policies, the waste treatment and recycling of test fixtures have received increasing attention. Reasonable treatment of waste and waste products generated during the production process and recycling of valuable parts and materials can effectively reduce environmental pollution.
Summary
Customized test fixtures occupy a pivotal position in modern manufacturing, and their application range is wide, involving multiple industries. With the continuous improvement of production automation, intelligence and product quality requirements, the design and manufacture of customized test fixtures will become more complex and sophisticated. In the future development, customized test fixtures will not only continue to develop in the direction of intelligence, automation and modularization, but will also play a greater role in environmental protection, cost control and sustainable development.